汽车发电机轴承检测的重要性与检测项目解析
汽车发电机轴承作为发电机核心部件之一,承担着支撑转子旋转、降低摩擦损耗的重要作用。据统计,约35%的发电机故障源于轴承异常,轻则导致异响、发电量下降,重则引发转子卡死甚至发动机熄火。因此,定期开展轴承检测是保障车辆电力系统稳定运行的关键环节。本文将从静态检测到动态性能分析,系统梳理发电机轴承检测的核心项目与技术要点。
一、外观与尺寸精度检测
通过目视和测量工具检查轴承表面是否存在划痕、锈蚀、变形等缺陷,使用千分尺测量内外圈直径、宽度及滚道圆度。允许公差需参照ISO 492标准,轴向游隙应控制在0.05-0.15mm范围内。特殊情况下需通过三维坐标仪对轴承座进行同心度扫描,确保安装面的同轴度误差≤0.03mm。
二、运转性能动态检测
在模拟负载条件下,采用振动加速度传感器(频率范围5-10kHz)监测轴承运行状态。正常工况下振动值应低于4.5mm/s(RMS值),若出现高频尖峰则提示滚道剥落。同步使用红外热像仪监测温升,连续运转30分钟后温度不得超过环境温度+45℃。对于带密封件的轴承,还需检测旋转扭矩变化,异常阻力增大可能预示润滑失效。
三、润滑状态与材料分析
通过光谱仪检测润滑脂中的金属磨粒成分,铁元素含量超过150ppm即需预警。采用傅里叶红外光谱分析润滑剂氧化程度,酸值(TAN)升高0.5mgKOH/g表明需更换油脂。对于高里程轴承,可取样进行金相检测,观察是否存在显微裂纹或贝氏体转变等材料劣化现象。
四、智能化检测技术应用
新型MEMS传感器可实时监测轴承运行参数,结合机器学习算法实现早期故障预警。实验数据显示,基于声发射技术的检测系统对微点蚀的识别准确率达92%,比传统方法提前300小时发现异常。此外,采用工业内窥镜可对装机轴承进行免拆解检查,大幅提升检测效率。
通过上述多维度的检测体系,可精准判断轴承剩余寿命,建议每行驶5万公里或出现异常噪音时进行专项检测。规范的检测流程不仅能预防突发故障,更能延长发电机整体使用寿命30%以上,为行车安全提供可靠保障。
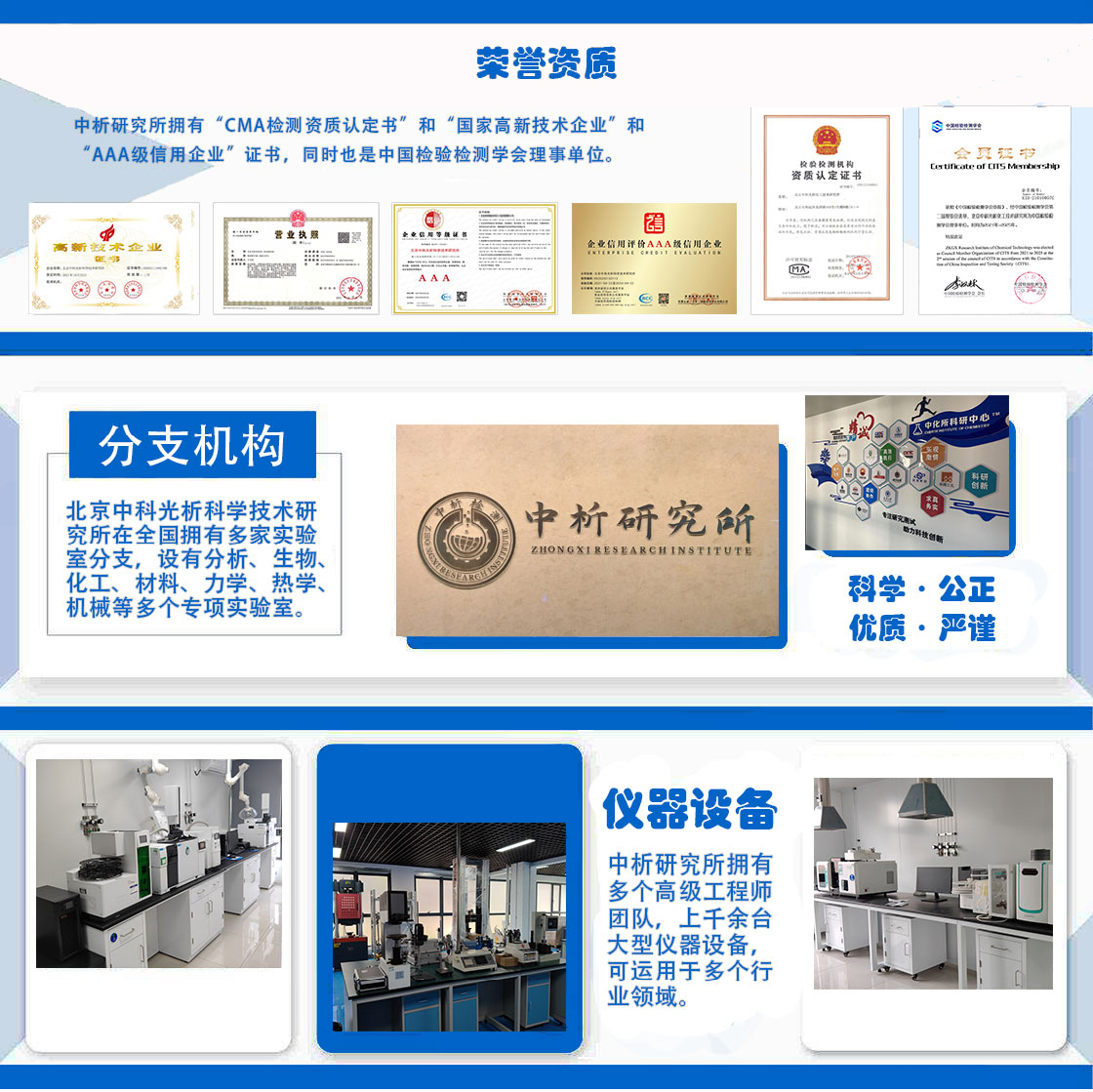
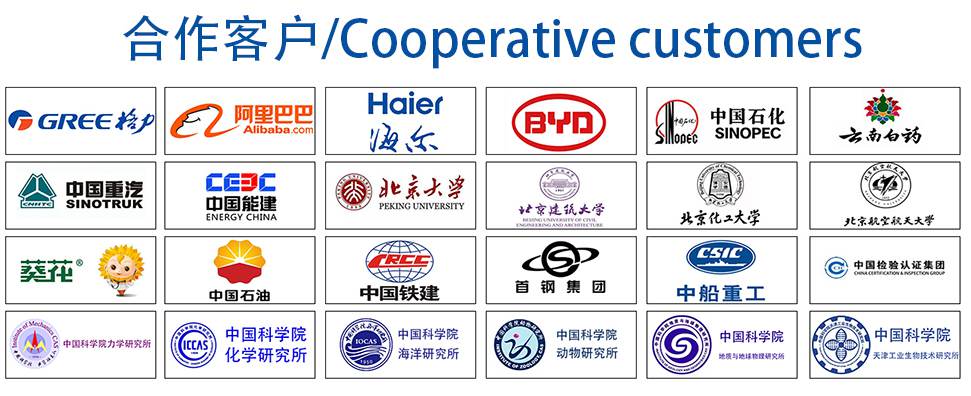