陶瓷球检测:守护精密工业的核心元件
在精密机械、航空航天、医疗器械等领域,陶瓷球作为关键零部件,其性能直接影响着设备运转精度与使用寿命。与传统的金属材料相比,氧化锆、氮化硅等陶瓷材料凭借高硬度、耐磨损、抗腐蚀等特性,在高转速、高温高压等极端工况中展现出显著优势。然而,陶瓷球的微小缺陷可能导致轴承卡死、仪器失准甚至设备报废,因此建立完善的陶瓷球检测体系成为保障工业安全的重要防线。
核心检测项目解析
1. 尺寸与形位公差检测
采用激光扫描仪与三坐标测量机(CMM)进行直径、圆度、球度、表面波纹度的精密测量,确保尺寸误差≤0.1μm,球度偏差控制在ISO3290标准G5级以内。特别关注批量生产时的尺寸一致性,防止装配过程中出现间隙异常。
2. 表面完整性检测
通过3D表面轮廓仪和电子显微镜(SEM)进行微裂纹、气孔、划痕的纳米级检测,重点分析Ra≤0.01μm的表面粗糙度要求。采用渗透探伤技术排查亚表面缺陷,利用X射线衍射仪检测残余应力分布,预防脆性断裂风险。
3. 材料性能验证
执行维氏硬度测试(≥1500HV)、三点抗弯强度试验(≥800MPa)以及压痕断裂韧性评估。通过热膨胀系数测定(CTE 6.5-10×10⁻⁶/℃)和高温氧化实验(1200℃/100h),验证材料在极端温度下的稳定性。
4. 动态性能测试
在模拟工况的轴承试验台上进行10⁷次循环疲劳测试,监测振动加速度值变化(≤0.5m/s²)。采用高速摄像机捕捉转速超过50,000rpm时的运动轨迹,分析陶瓷球的动态平衡性能与摩擦系数波动。
5. 环境适应性检测
开展酸碱盐雾腐蚀试验(按ASTM B117标准)、氢渗透测试(针对化工设备)以及真空环境下的放气率测定。对于生物医疗应用场景,额外增加细胞毒性测试与高温高压灭菌验证。
检测技术创新趋势
随着工业4.0的发展,陶瓷球检测正逐步实现智能化升级。基于机器视觉的在线分选系统可达到每分钟300颗的检测速度,AI算法对缺陷的识别准确率提升至99.7%。同步辐射CT技术可重构内部三维结构,而太赫兹波检测则为非接触式亚表面探伤提供了新方案。
通过构建覆盖原料筛选、过程监控、成品检验的全流程质量体系,陶瓷球制造企业可将产品不良率控制在0.01%以下。这不仅推动了精密制造业的技术革新,更为半导体光刻机、航天导航系统等高端装备的国产化突破提供了关键支撑。
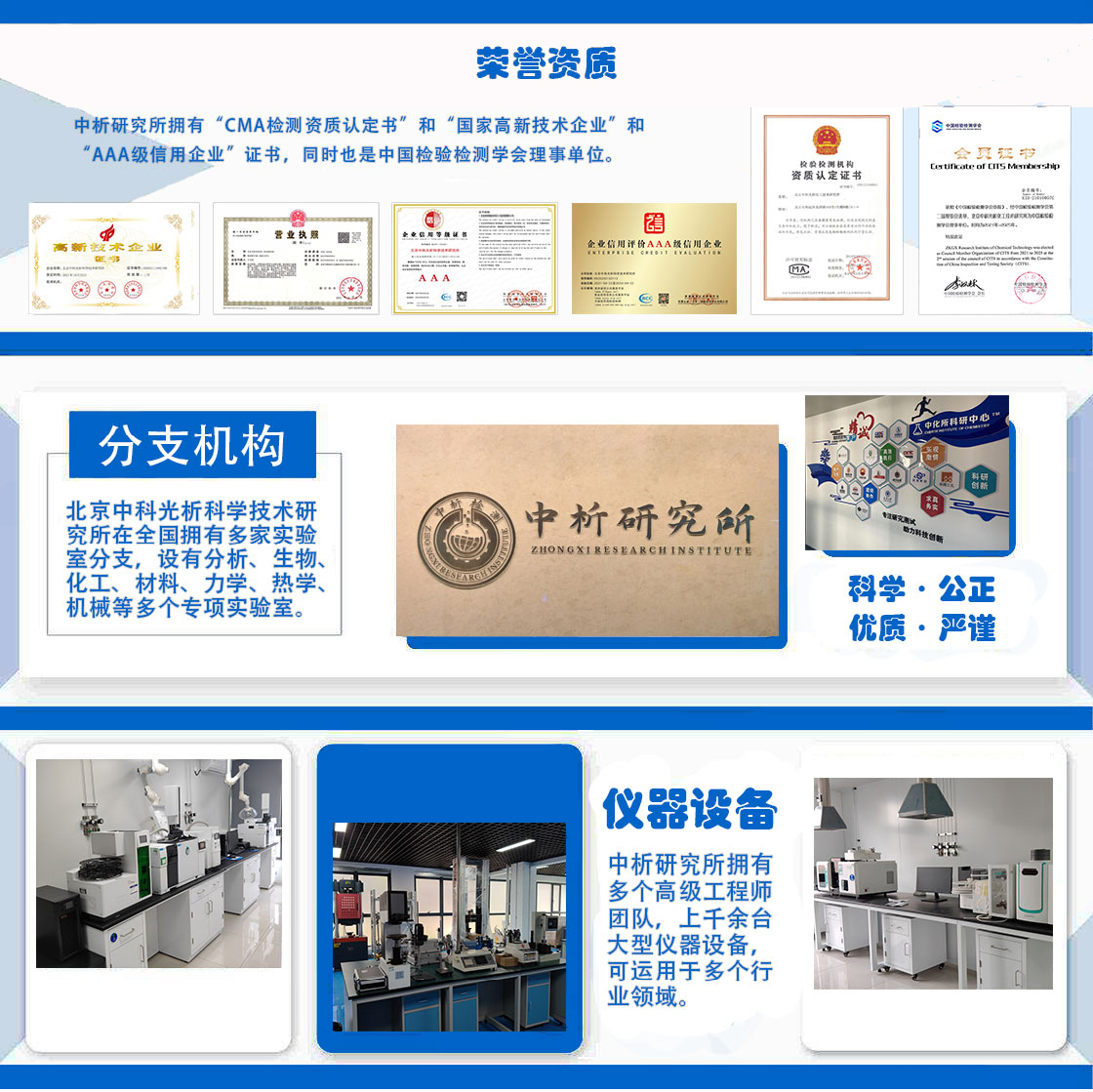
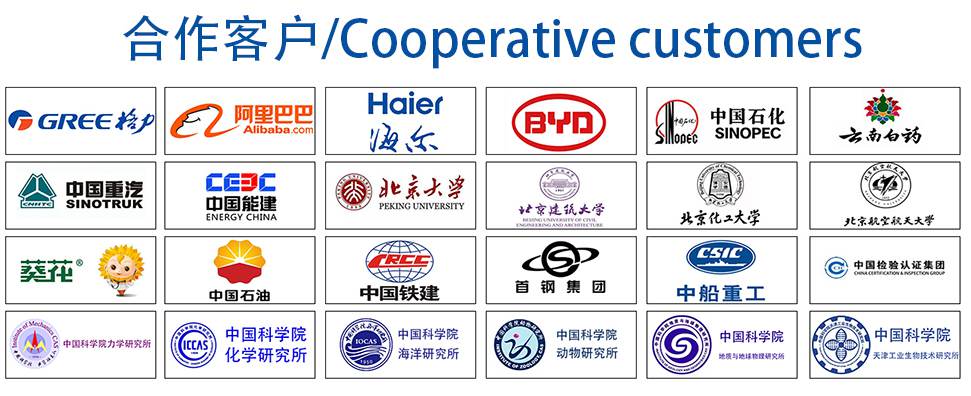