高压锅炉给水泵检测的重要性与必要性
高压锅炉给水泵是火力发电厂、化工企业以及工业锅炉系统的核心设备之一,其主要功能是将除氧后的高温高压水输送至锅炉系统,保障锅炉的稳定运行。由于长期处于高温、高压、高速运转的严苛工况下,泵体及配套部件易出现磨损、腐蚀、泄漏等问题,一旦发生故障可能引发停机事故甚至安全隐患。因此,定期开展高压锅炉给水泵的全面检测,是确保设备安全运行、延长使用寿命、提高能源效率的关键环节。
高压锅炉给水泵主要检测项目
1. 外观与结构检查
重点检查泵体、叶轮、轴套等部件是否存在裂纹、变形或腐蚀,密封件是否老化,连接螺栓是否松动。通过目视检查、渗透探伤(PT)或磁粉检测(MT)等手段,确保关键部位无结构性缺陷。
2. 振动与噪音监测
使用振动分析仪测量泵体各部位的振动值,对比ISO 10816标准判断是否超标。同时采集运行噪音频谱,分析轴承、叶轮等部件是否存在异常磨损或气蚀现象。
3. 温度检测与热成像分析
通过红外热像仪监测轴承箱、机械密封、电机绕组等部位的温度分布,轴承温度不应超过75℃(环境温度40℃时)。异常温升可能预示润滑不良或摩擦加剧。
4. 压力与流量性能测试
在额定工况下检测出口压力、流量与设计值偏差,效率下降超过5%时需排查叶轮磨损或间隙异常。采用超声波流量计和压力变送器进行动态数据采集。
5. 密封系统专项检测
对机械密封或填料密封进行泄漏量检测,高压侧泄漏量超过50mL/h需立即维护。检查冲洗管路、冷却系统是否通畅,密封腔压力是否符合设计要求。
6. 电气系统与绝缘测试
测量电机绕组绝缘电阻(不低于1MΩ)、三相电流平衡度(偏差<5%),检查控制柜继电器、变频器等元件的工作状态,确保电气保护功能有效。
7. 润滑油与轴承状态评估
取样分析润滑油粘度、水分含量及金属磨粒浓度,使用冲击脉冲法检测轴承损伤程度。对于滑动轴承,还需检查巴氏合金层与轴颈的配合间隙。
8. 材料腐蚀与壁厚检测
对泵壳、进出口管道进行超声波测厚,壁厚减薄量超过原厚度10%需预警。针对高温区段,采用金相分析评估材料蠕变损伤情况。
检测周期与标准依据
常规检测建议每季度进行1次状态监测,年度大修时开展全面检测。需执行GB/T 3215《石油、重化学和天然气工业用离心泵》、ASME PTC 8.2《给水泵试验规程》等标准,并结合设备制造商的技术规范。
检测结果分析与处理
通过综合检测数据建立设备健康档案,采用趋势分析法预测剩余寿命。对发现的早期故障(如轴承轻微剥落、叶轮轻微气蚀),可通过在线修复或备件更换及时处理;出现严重结构损伤时,应强制停机大修。
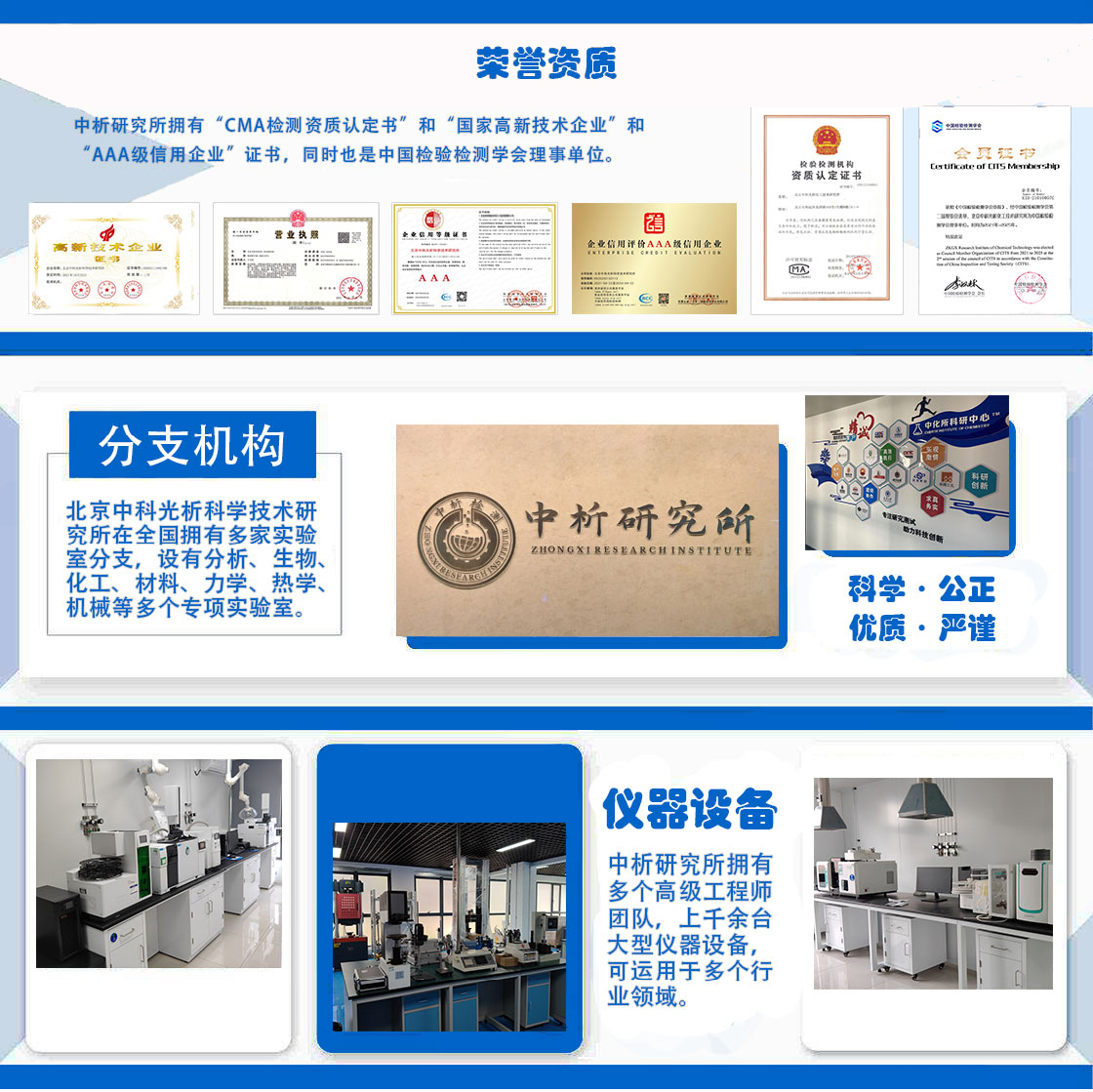
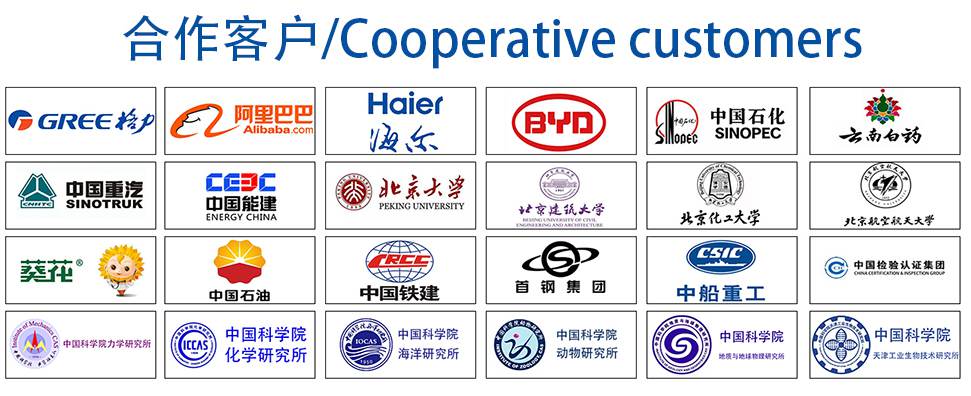