航空航天系列自润滑衬套检测的重要性
在航空航天领域,自润滑衬套作为关键运动部件的核心元件,广泛应用于起落架、发动机、舵机等系统中,承担着降低摩擦、减少磨损、延长使用寿命的重要作用。由于航空航天装备对可靠性和安全性的要求极高,自润滑衬套的检测成为确保飞行器性能稳定、避免故障的核心环节。通过系统化的检测项目,可以验证材料的自润滑性能、耐高温性、抗疲劳强度以及极端环境下的可靠性,从而降低因材料失效引发的安全风险,同时满足国际适航标准(如AS9100、NASA技术规范等)。
自润滑衬套核心检测项目
1. 材料成分与微观结构分析
通过光谱分析仪(如ICP-OES)和扫描电镜(SEM),验证衬套基体材料(如铜合金、聚酰亚胺复合材料)的化学成分是否符合设计要求。同时检测固体润滑剂(石墨、二硫化钼等)的分布均匀性,确保微观孔隙结构能有效储存润滑介质。
2. 摩擦磨损性能测试
使用摩擦磨损试验机(如UMT TriboLab)模拟实际工况,检测衬套在高速、高载荷下的摩擦系数(要求通常≤0.15)和磨损量(如单位时间体积损失<0.02mm³/N·m)。需覆盖常温、低温(-60℃)及高温(300℃)环境,验证宽温域润滑稳定性。
3. 承载能力与疲劳寿命评估
通过液压伺服疲劳试验机进行动态载荷测试,验证衬套在循环应力(如100MPa~300MPa)下的抗压强度和疲劳寿命(需超过10⁷次循环无裂纹)。结合有限元分析(FEA),预测极端负载(如飞行器着陆冲击)下的形变阈值。
4. 耐环境适应性检测
包括盐雾试验(ASTM B117)、湿热老化(85℃/85%RH)、真空辐照(模拟太空环境)等,评估衬套在腐蚀性介质、高湿度及辐射条件下的性能衰减率,确保其满足30年以上的服役寿命要求。
5. 无损检测与缺陷定位
采用X射线断层扫描(CT)和超声波探伤技术(UT),检测衬套内部的气孔、夹杂、层间剥离等缺陷。缺陷尺寸需严格控制在0.1mm以下,避免应力集中导致的突然失效。
检测流程与技术规范
航空航天自润滑衬套的检测需遵循严格的流程:从原材料入库检验→加工过程监控→成品性能测试→环境模拟验证→终检报告生成。检测标准涵盖SAE AS81820、AMS 7908等专用规范,同时需结合型号任务书进行定制化测试设计。
结语
通过上述多维度的检测项目,可全面确保自润滑衬套在航空航天极端工况下的可靠性。随着新材料和新工艺的迭代,检测技术也需同步升级,例如引入智能传感器实时监测磨损状态,进一步推动行业向高精度、长寿命、低维护的方向发展。
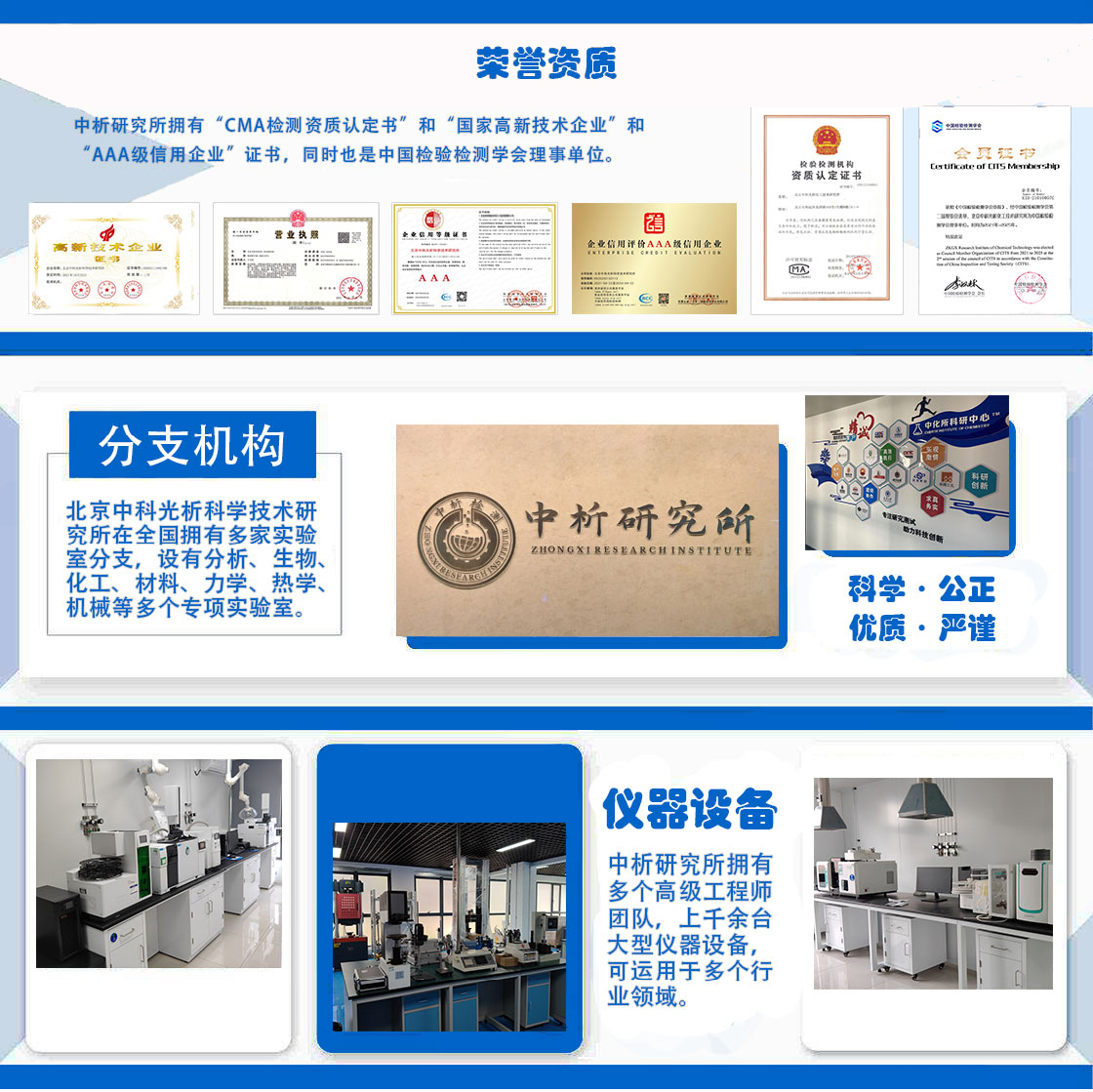
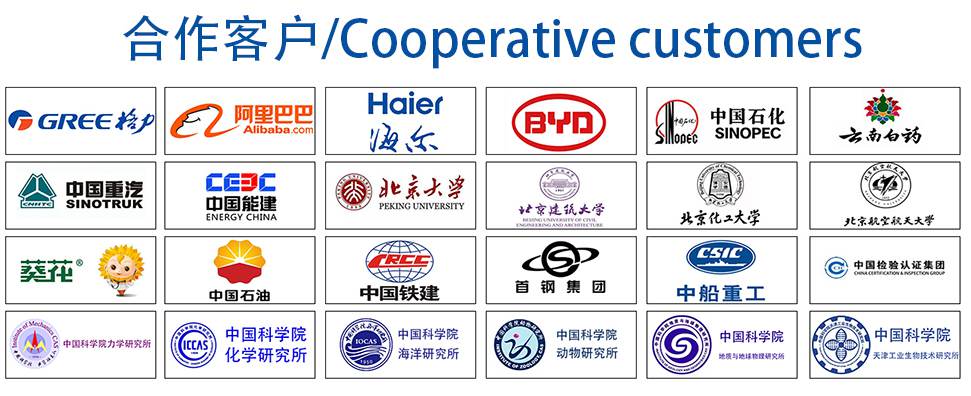