装甲车辆滚动轴承检测的关键项目与技术规范
装甲车辆作为军事装备的核心组成部分,其传动系统的可靠性直接关系到战场机动性与任务执行效率。滚动轴承作为传动装置中的核心部件,承担着支撑轴系、降低摩擦损耗及传递动力的重要功能。在极端工况下(如高载荷、震动、沙尘环境),轴承的失效可能导致传动系统瘫痪,甚至引发车辆事故。因此,建立科学的滚动轴承检测体系,对装甲车辆的运维保障具有战略意义。
一、外观与缺陷检测
采用目视检查与仪器辅助相结合的方式,重点检测滚道剥落、裂纹、锈蚀等表面损伤。通过磁粉探伤技术可发现微米级裂纹,荧光渗透检测则适用于非磁性材料。近年引入的工业内窥镜技术,可实现复杂装配结构中轴承的360°无死角观测,显著提升缺陷检出率。
二、尺寸精度检测
使用三坐标测量机(CMM)对轴承内径、外径、圆度及沟道位置进行微米级计量。针对装甲车辆常用的双列圆锥滚子轴承,需特别检测滚子锥角偏差及保持架间隙。根据GJB 3239-1998军用标准,径向游隙应控制在0.05-0.15mm范围内,轴向游隙不超过0.3mm。
三、材料性能检测
通过金相分析仪检测材料晶粒度(要求5-8级),采用洛氏硬度计测量轴承钢表面硬度(HRC58-62)。利用超声波探伤仪检测内部夹杂物,依据MIL-STD-2154标准,当缺陷尺寸超过0.8mm时需判定为不合格。针对特殊涂层轴承,需进行盐雾试验验证耐腐蚀性能。
四、动态特性测试
在专用试验台上模拟实际工况,监测轴承的振动加速度值(≤4.5m/s²)、温升曲线(ΔT<45℃)及噪声频谱。采用加速度传感器捕捉异常振动信号,通过FFT分析识别故障特征频率。对于高速重载轴承,需进行200小时持续加载试验验证疲劳寿命。
五、润滑状态监测
运用油液光谱分析技术检测润滑油中Fe、Cr元素含量,预警异常磨损。采用铁谱仪分析磨粒形态,区分正常磨合与故障磨损阶段。根据GJB 2373A规范,当油液内金属颗粒浓度超过15ppm时,需立即进行轴承更换。
六、智能化检测技术应用
新型智能轴承通过嵌入MEMS传感器实现实时状态监测,可采集温度、振动、载荷等多维度数据。结合大数据分析平台,建立轴承健康度评估模型,精确预测剩余使用寿命(RUL)。某型装甲车已试点应用该技术,使轴承故障预警提前时间达到200工作小时。
现代装甲车辆滚动轴承检测已形成从宏观到微观、静态到动态的完整技术体系。通过多参数融合分析与智能诊断,可将轴承故障率降低68%以上。未来随着太赫兹成像、数字孪生等新技术的应用,检测精度与效率将实现跨越式提升,为装甲装备的可靠运行提供更强保障。
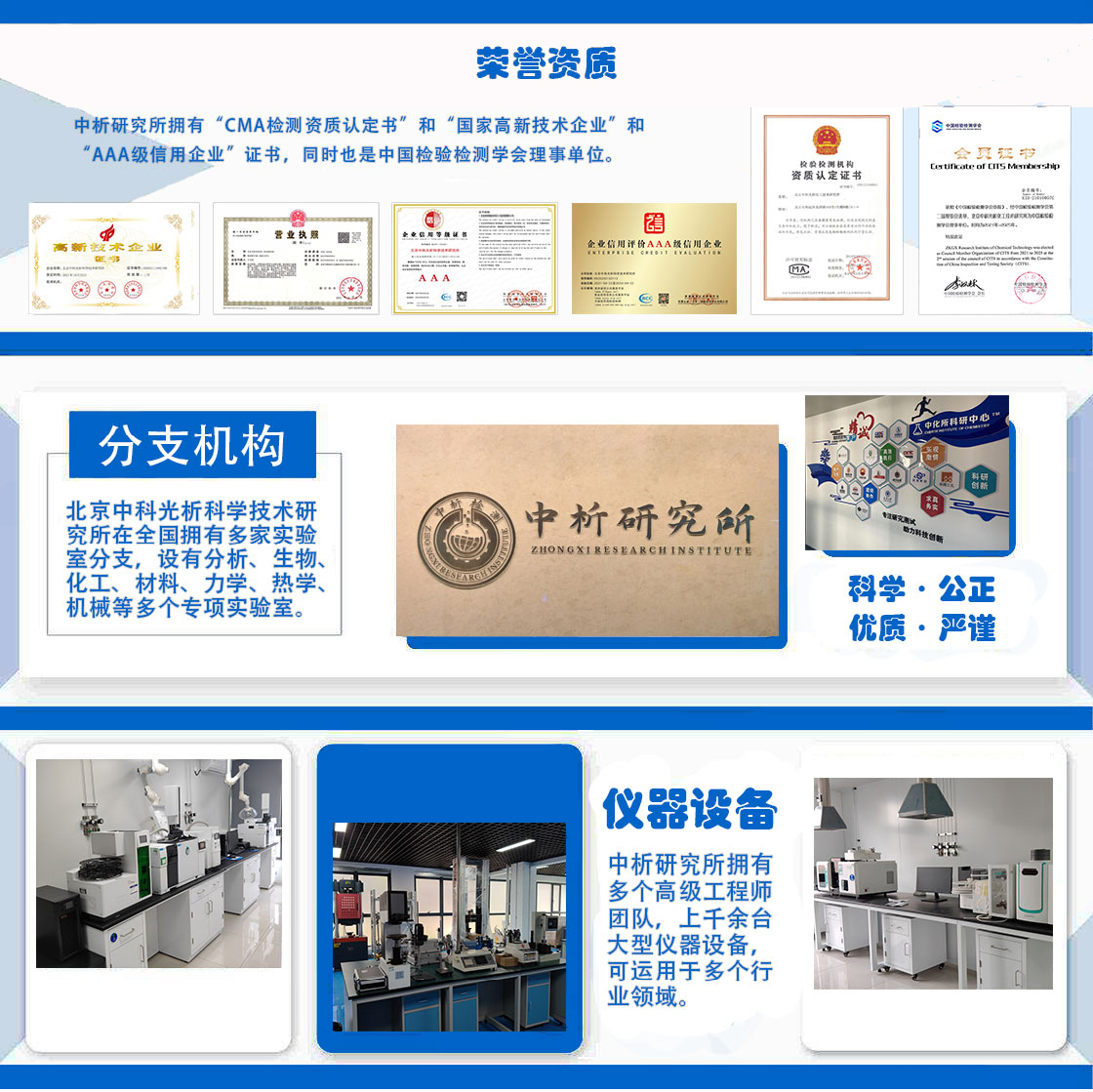
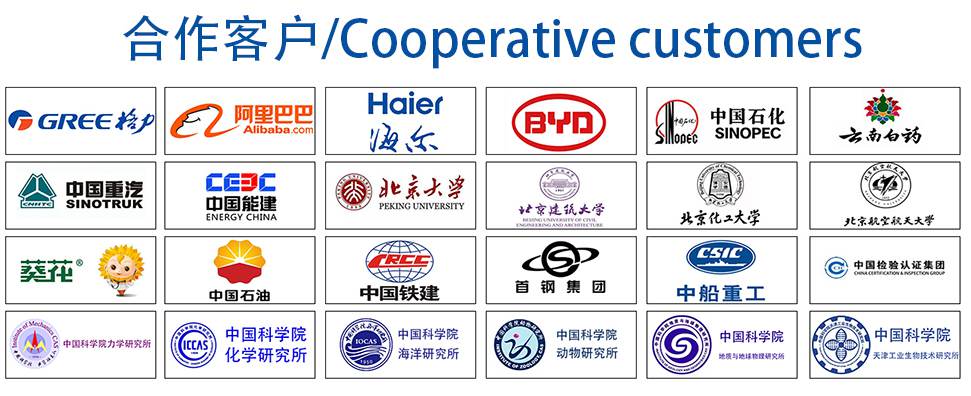