机床主轴用双向推力角接触球轴承检测的重要性
机床主轴作为精密加工设备的核心部件,其性能直接决定了加工精度、稳定性和使用寿命。双向推力角接触球轴承是主轴系统中的关键组件,负责承受轴向和径向复合载荷,同时确保高转速下的动态平衡。随着数控机床、高速加工中心等设备对精度要求的不断提升,轴承的制造质量需通过严格的检测流程来验证。检测不仅能发现加工缺陷、材料问题,还能评估轴承的承载能力、旋转精度和疲劳寿命,为机床主轴的可靠运行提供技术保障。因此,针对此类轴承的检测项目需覆盖几何参数、物理性能及动态特性等多个维度。
核心检测项目及方法
1. 外观与表面质量检测
通过目视或显微镜观察轴承内外圈、滚动体及保持架的表面状态,检查是否存在划痕、锈蚀、裂纹或剥落等缺陷。采用工业相机配合图像处理技术可量化分析表面粗糙度,确保沟道和接触面的光洁度符合ISO 3290标准。
2. 几何尺寸精度检测
使用精密测量仪器(如三坐标测量机、千分尺)对轴承内径、外径、宽度、沟道曲率半径等关键尺寸进行检测。重点关注轴承装配高度的公差(通常要求±0.005mm)及接触角的对称性,确保与主轴系统的匹配精度。
3. 旋转精度与跳动量测试
在专用旋转测试台上模拟实际工况,测量轴承的轴向跳动和径向跳动。通过激光位移传感器或电容式测头采集数据,分析高速旋转时轴承的动态偏心量。根据JIS B1514标准,精密级轴承的全跳动应小于5μm。
4. 预紧力与刚性检测
通过扭矩传感器和加载装置测试轴承的预紧力,验证其是否达到设计要求。同时利用动态刚度测试仪评估轴承在轴向和径向载荷下的变形量,确保主轴系统在高负载下的稳定性。
5. 材料性能与耐久性试验
采用金相显微镜分析轴承钢的微观组织,检测是否存在碳化物偏析或晶粒粗大问题。通过洛氏硬度计测定材料硬度(通常要求HRC 58-62),并进行高温耐久试验(如10,000小时寿命测试),模拟长期使用后的磨损和疲劳特性。
6. 振动与噪声特性分析
在消声室中使用加速度传感器和声级计采集轴承运转时的振动频谱和噪声值。通过FFT(快速傅里叶变换)识别异常频率成分,判断是否存在装配误差或局部损伤。高速轴承的振动加速度级需满足GB/T 24610.3的A级标准。
7. 密封与润滑效能验证
针对带密封结构的轴承,进行粉尘侵入试验和脂泄漏测试。使用光学粒子计数器评估密封件的防污染能力,同时通过温升试验(80℃/500rpm连续运行)检测润滑脂的氧化稳定性和高温保持性。
检测结果的应用与改进
通过上述系统性检测,可建立轴承质量数据库并输出SPC(统计过程控制)报告,用于优化制造工艺。对于超差批次,需追溯热处理、磨削或装配环节的工艺参数,针对性调整沟道超精研时间、预紧力加载方式等关键技术指标,最终实现主轴轴承性能的全面达标。
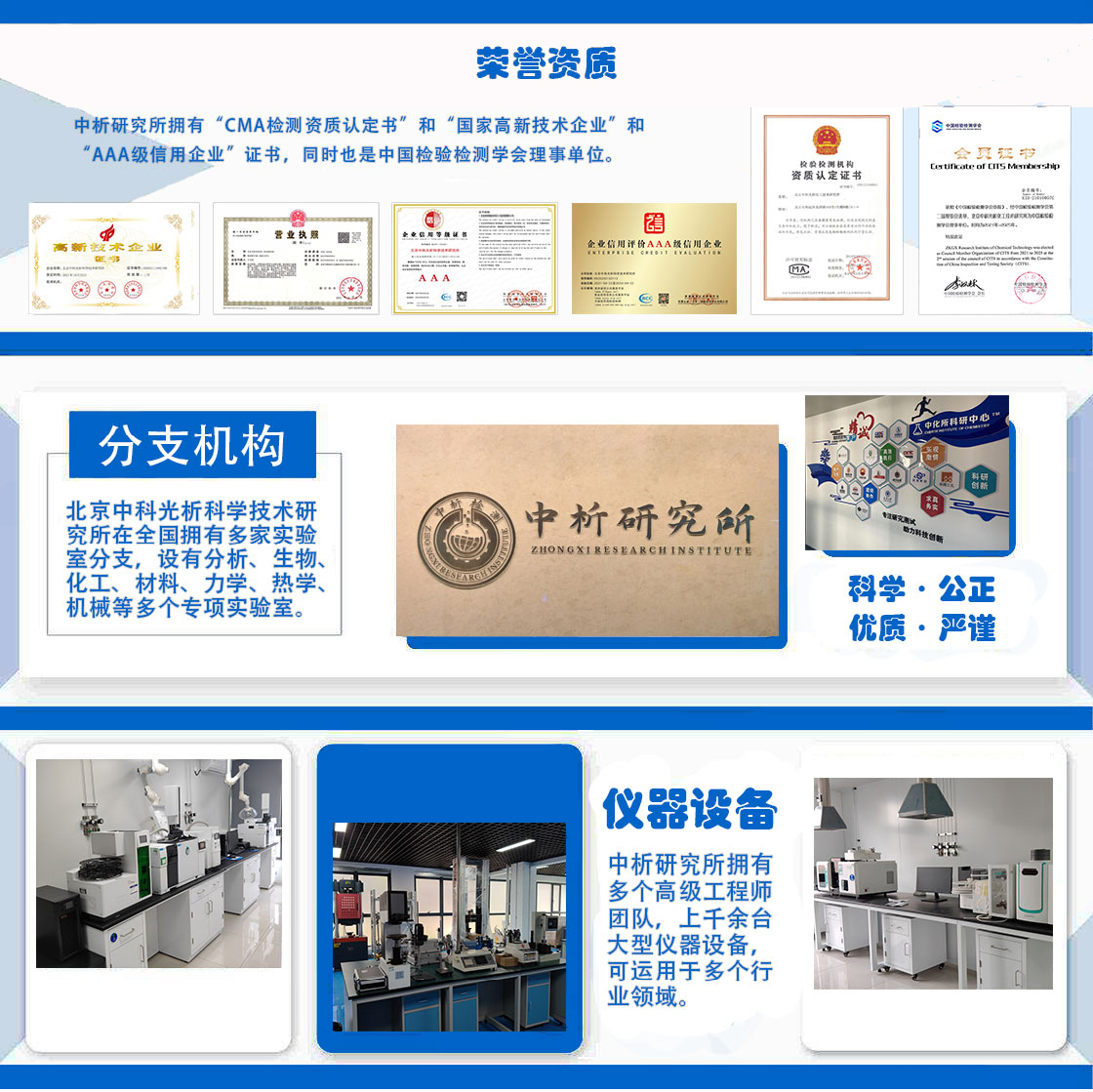
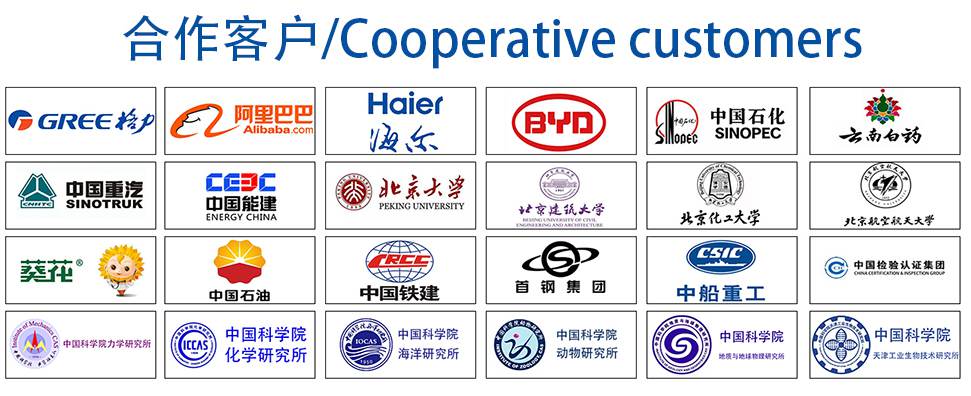