数控重型立柱移动式立式车床检测的核心意义
数控重型立柱移动式立式车床作为高端装备制造业的核心设备,广泛应用于能源电力、船舶制造、航空航天等领域的超大直径零件加工。其结构特点决定了立柱移动式设计能承载百吨级工件,而数控系统则需确保微米级加工精度。针对这类设备的系统化检测,不仅是设备出厂验收的必要环节,更是保障加工精度、延长设备寿命、预防生产事故的关键技术手段。通过科学的检测流程,可精准定位设备安装误差、运动副磨损、控制系统偏差等隐患,为复杂工况下设备性能的稳定性提供数据支撑。
核心检测项目体系
几何精度检测
采用激光干涉仪与电子水平仪进行多维空间精度验证:工作台端面平面度误差需控制在0.02mm/m以内;立柱导轨在X/Z轴方向的垂直度偏差不超过0.015mm/1000mm;滑枕移动直线度采用自准直仪检测,全程波动值应≤0.008mm。特殊工况下还需进行热变形补偿测试,监测连续加工8小时后主要结构件的温度-形变耦合效应。
动态性能检测
通过振动频谱分析系统评估设备动态特性:主轴在额定转速下的径向跳动须≤0.005mm;轴向窜动测试采用电容式位移传感器,标准值为0.003mm;刀架快速移动时加速度波动不应超过设定值的15%。针对重型切削工况,需特别进行切削抗力模拟测试,验证横梁-立柱系统在极限载荷下的结构稳定性。
数控系统功能验证
运用球杆仪进行圆度测试,综合评估插补精度与反向间隙补偿效果,循环圆度误差应<5μm;多轴同步精度测试需验证C轴与Z轴的联动偏差,通过标准为±2角秒。同时需检测急停响应时间(≤70ms)、过载保护触发阈值等安全功能参数,确保符合ISO 23125标准要求。
辅助系统检测
液压系统压力稳定性测试要求波动范围≤±0.2MPa;自动润滑系统需验证各润滑点流量均匀性,偏差不超过15%。针对重型设备特有的静压导轨系统,需专门检测油膜刚度,在最大载荷下油膜厚度变化应控制在初始值的20%以内。
全生命周期检测策略
建立三级检测体系:首次安装执行72小时连续空载跑合检测,采集各系统基准数据;周期性维护检测每2000工作小时开展动态精度复检;大修后检测需完整恢复出厂精度标准。应用工业物联网技术构建设备健康管理系统,通过振动、温度、电流等多源信号融合分析,实现预测性维护的精准决策。
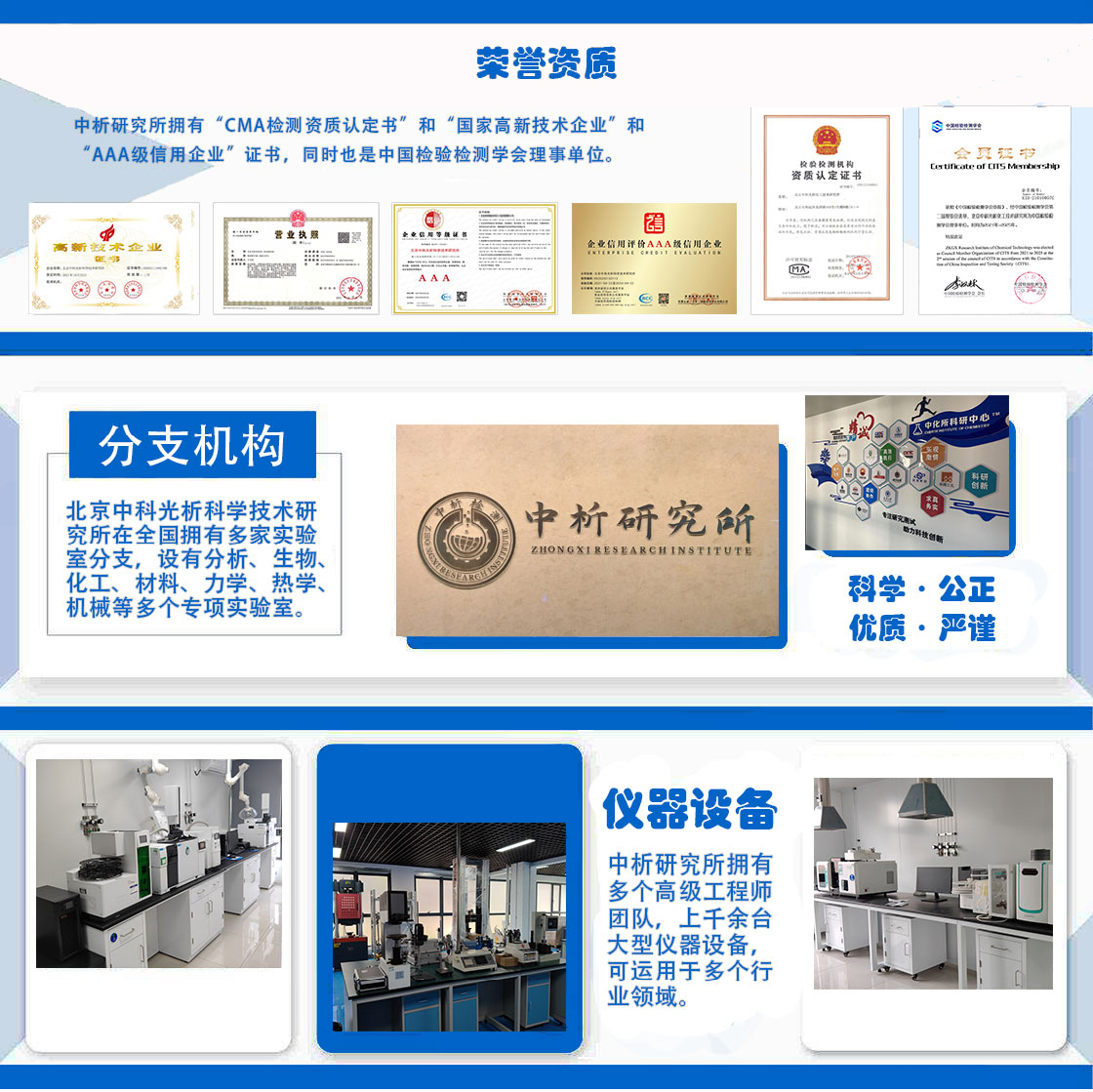
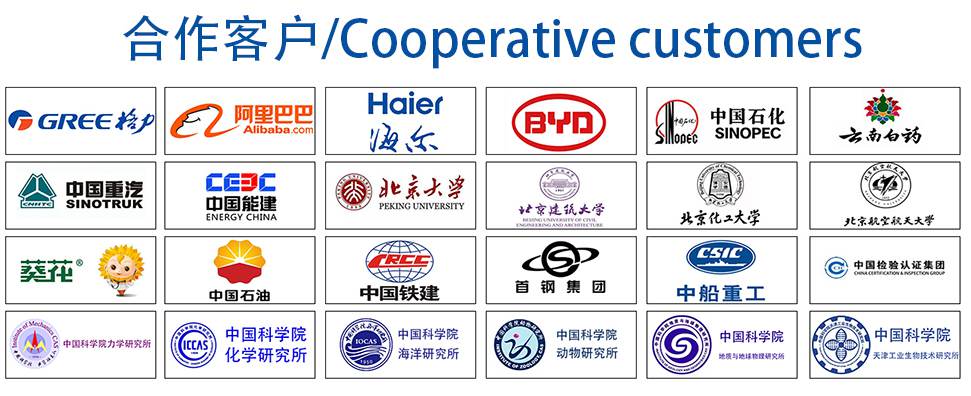