航天滚动轴承检测关键技术解析
在航天工业领域中,滚动轴承作为运载火箭发动机、卫星姿态控制机构及空间站机械臂等核心部件的关键传动单元,其性能稳定性直接关系着航天器的运行安全与任务成功率。由于航天器需经历发射阶段的剧烈振动、太空极端温度(-180℃至+300℃)以及超高真空等严苛环境考验,对滚动轴承的检测提出了远超民用标准的特殊要求。目前国际航天领域已形成包含材料特性、几何精度、动态性能三大维度共26项专项检测指标体系,通过多维立体化检测手段确保轴承在寿命周期内的零失效表现。
1. 材料微观组织检测
采用场发射扫描电镜(FE-SEM)和透射电镜(TEM)对轴承钢的晶粒度(要求优于ASTM 12级)、碳化物分布(尺寸≤0.5μm)及残余奥氏体含量(控制在3-8%)进行纳米级观测。同步开展X射线衍射残余应力分析,确保表层残余压应力值≥1200MPa。针对新型陶瓷混合轴承,需进行能谱分析(EDS)验证氮化硅材料的氧含量≤0.15wt%,并利用激光共聚焦显微镜检测表面微裂纹(阈值≤2μm)。
2. 几何精度数字孪生检测
基于ISO 12181标准构建轴承全参数三维模型,采用白光干涉仪实现沟道曲率半径(公差±0.5μm)、滚道波纹度(W值≤0.05μm)的亚微米级测量。配置六轴工业机器人搭载激光跟踪仪,对大型轴承组件(如直径2.4米的空间机械臂轴承)进行动态形变监测,采样频率达2000Hz时可捕捉0.8μm级的瞬时变形量。开发专用算法对1.5TB/小时的点云数据进行实时处理,构建数字孪生体进行虚拟装配验证。
3. 极端工况模拟试验
在真空热试验舱内(极限真空度5×10^-7Pa)进行-196℃(液氮冷却)至+350℃(红外加热)的2000次温度循环试验,监测保持架间隙变化率(标准值≤0.3%)。采用电磁振动台模拟发射阶段的25g/2000Hz随机振动,通过光纤Bragg光栅传感器网络实时采集256通道应变数据。针对深空探测任务,设计10^-12torr级超高真空摩擦试验台,持续监测20000rpm转速下的扭矩波动(允许偏差±1.5%)。
4. 智能健康监测系统
植入MEMS传感器阵列(尺寸3×3×1mm³)实现轴承运行状态在线监测,包括:
• 声发射系统捕捉早期剥落信号(特征频率50-150kHz)
• 电容式油膜厚度传感器(分辨率10nm)
• 分布式光纤测温(空间分辨率1cm)
通过BP神经网络对多源异构数据进行融合分析,建立剩余寿命预测模型(误差≤5%),成功应用于长征五号火箭涡轮泵轴承的在轨健康管理。
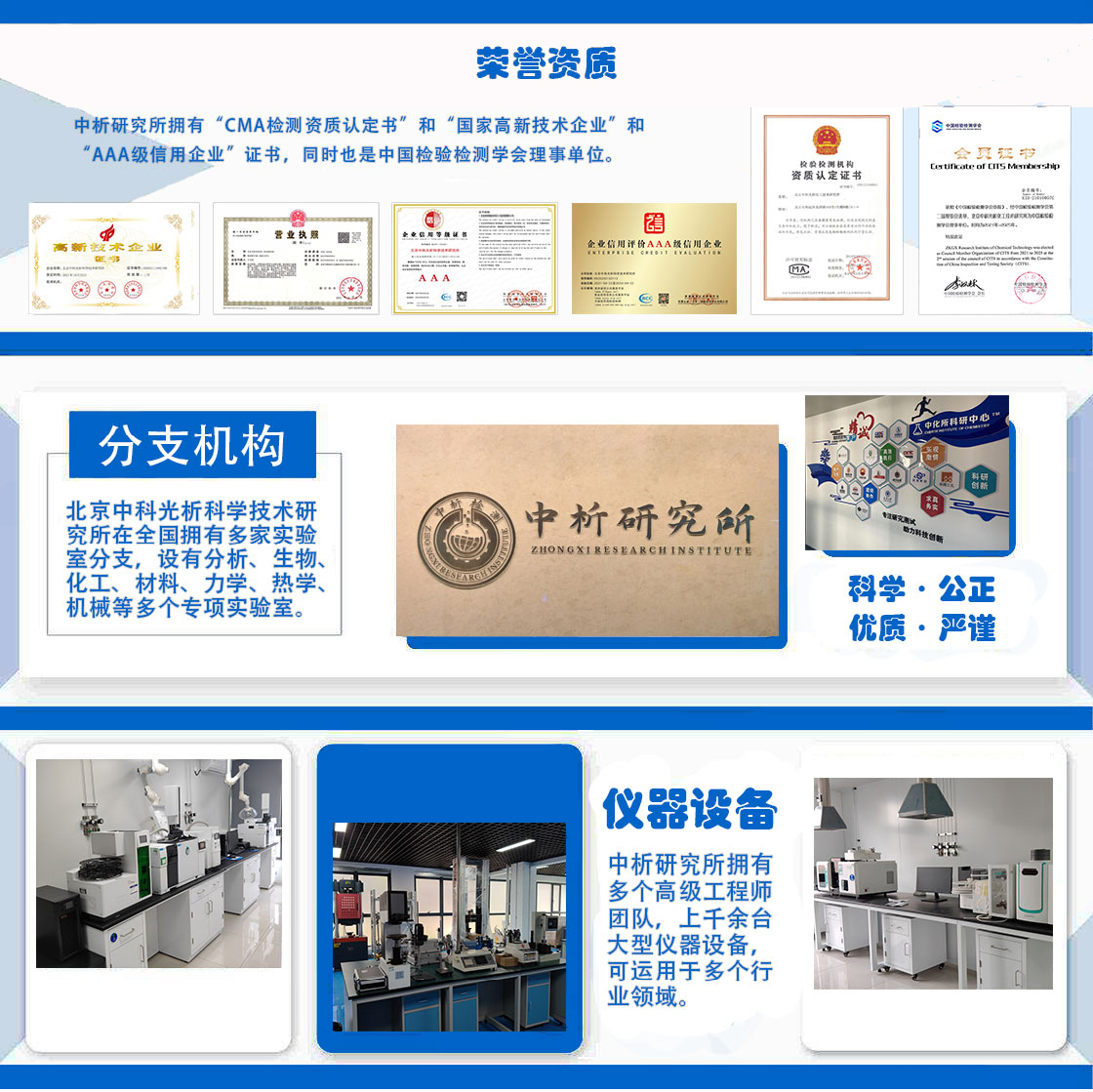
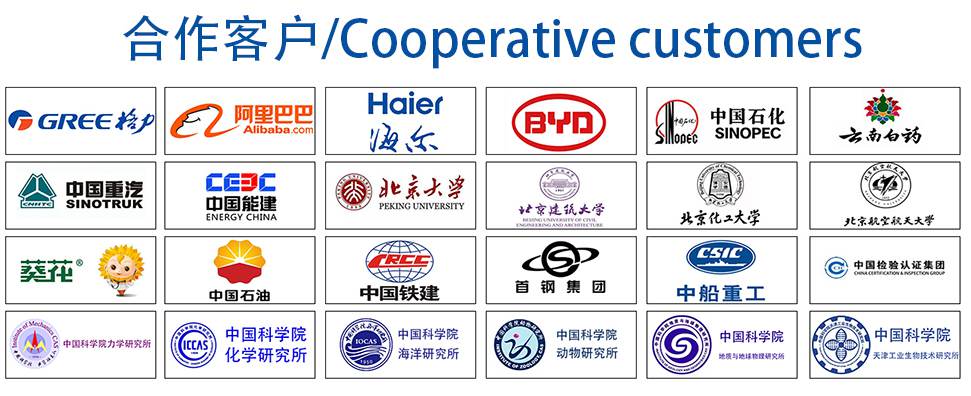