全量程指标偏差检测的技术解析
全量程指标偏差检测是工业制造、仪器仪表校准和精密设备维护中的核心环节,其核心目标是通过系统化的测试验证被测对象在整个量程范围内的性能稳定性与测量准确性。不同于常规的点校准或局部区间测试,全量程检测要求从最小值到最大值区间内设置多个特征检测点,通过对比理论值与实测值的偏差曲线,全面评估设备线性度、重复性、迟滞性等关键参数。这种检测方法广泛应用于压力传感器、流量计、温度控制器等精密仪器,以及医疗设备、航空航天仪表等高精度领域,为设备性能优化和故障诊断提供量化依据。
全量程检测的核心项目
1. 零点校准与满量程验证: 在空载或基准状态下进行零点偏差测定,同时在最大量程点加载标准信号源,验证设备在极限工况下的输出稳定性。这两个端点数据为全量程分析建立基础坐标系。
2. 线性度测试: 选取量程范围内不少于10个等分点(如量程的10%、30%、50%、70%、90%等),通过对比输入标准值与设备输出值的拟合曲线,计算非线性误差率。对于高精度设备需采用三次样条插值法进行曲线修正。
3. 重复性检测: 在相同环境条件下,对特定检测点进行连续10次加载-卸载循环测试,通过统计学方法计算标准偏差和变异系数,评估设备测量结果的一致性。
4. 迟滞效应分析: 采用正反向加载模式(如从0→100%→0量程),对比上行与下行曲线间的最大偏差值,重点检测机械结构弹性形变或电子元件响应延迟带来的测量误差。
扩展检测维度
环境适应性测试: 在温度(-20℃~+60℃)、湿度(20%~95%RH)、振动(5Hz~500Hz)等变量条件下重复全量程测试,绘制环境干扰因子与测量偏差的关联矩阵。
长期稳定性监测: 通过72小时连续负载测试或周期性复测(如每月1次持续半年),建立设备性能衰减模型,为预防性维护提供数据支持。
检测流程规范化
典型检测流程包含四个阶段:1)设备预热与系统初始化;2)按ISO/IEC标准搭建检测平台;3)采用自动采集系统完成多维度数据记录;4)运用MES系统进行偏差趋势分析并生成三维误差分布图。现代检测体系普遍集成机器学习算法,可自动识别异常波动模式并预警潜在故障。
行业应用场景
在智能制造领域,工业机器人关节力矩传感器的全量程检测可提升装配精度0.02mm;在能源行业,输油管道压力变送器的全量程验证能将泄漏检测灵敏度提高40%;医疗领域呼吸机的流量传感器通过全量程校准,可使潮气量控制误差≤±3%。这些应用实例凸显了全量程指标偏差检测在保障设备可靠性和提升系统性能中的关键作用。
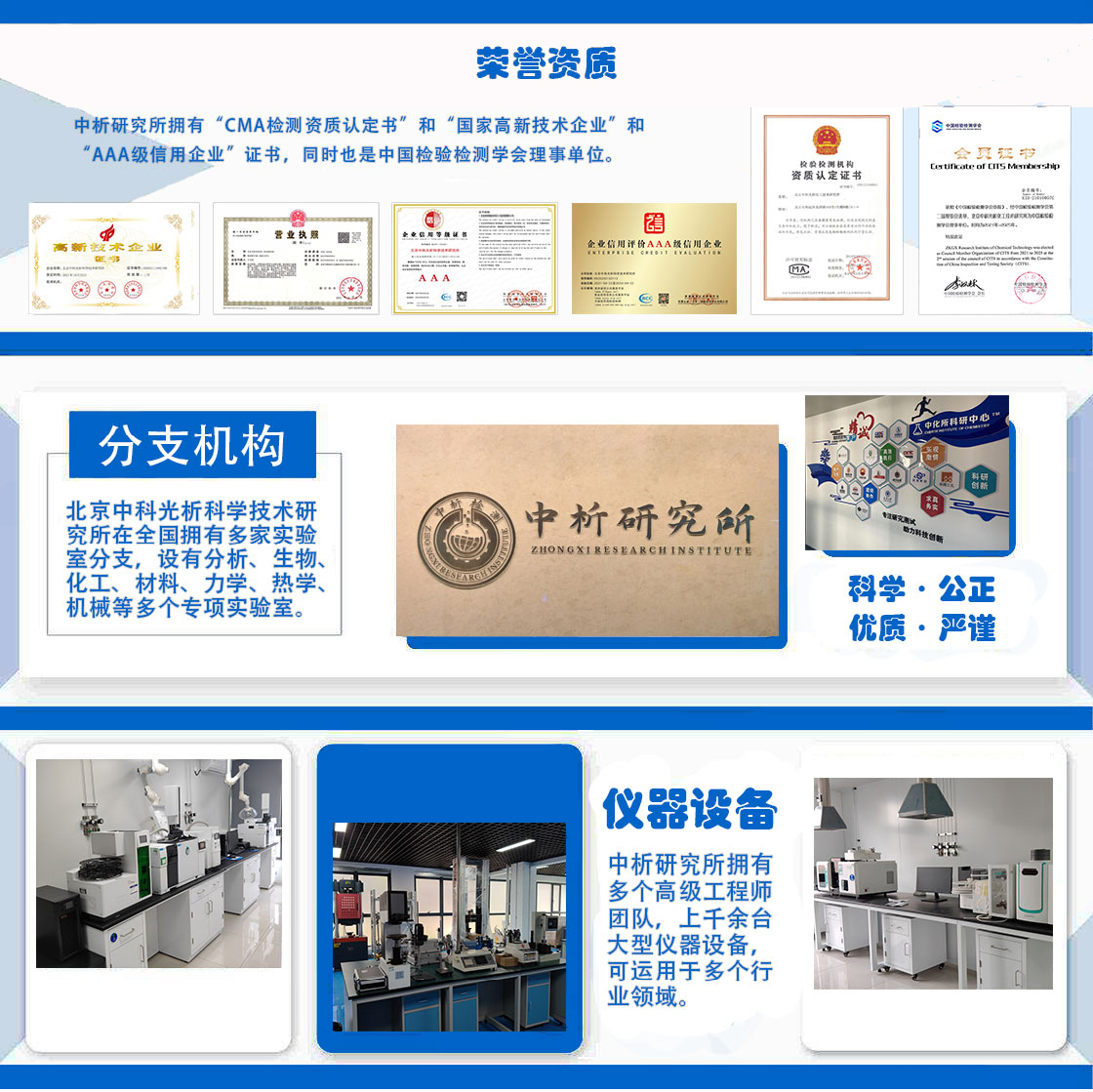
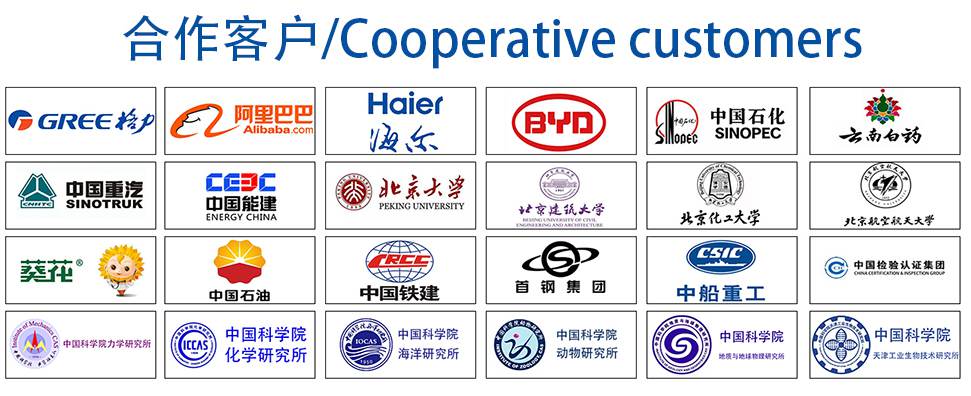