组合泵筒管式抽油泵检测
组合泵筒管式抽油泵是石油开采中广泛应用的核心设备,其性能直接影响油井产量和系统运行效率。由于长期处于高温、高压、高腐蚀的复杂工况环境中,其内部结构(如泵筒、柱塞、阀组等)易发生磨损、变形或密封失效等问题。因此,定期开展科学规范的检测项目至关重要,既可预防突发故障导致的生产停滞,又能延长设备使用寿命,降低运维成本。检测工作需涵盖几何精度、材料性能、动态运行状态及环境适应性等维度,并结合行业标准(如API Spec 11AX、GB/T 18607等)进行综合评估。
关键检测项目及内容
1. **尺寸精度检测** 使用千分尺、内径量表等工具测量泵筒内径、柱塞外径的圆度、圆柱度及配合间隙,确保符合API标准规定的公差范围(通常为±0.025mm)。同时检查螺纹连接部位的啮合长度和垂直度,防止因安装偏差导致的泄漏风险。
2. **密封性能检测** 通过液压试验台模拟工作压力(最高可达35MPa),测试泵筒与柱塞间的静态密封性及动态泄漏量。采用荧光检漏剂或氦质谱仪定位微渗漏点,并评估阀球与阀座的密封接触面磨损情况,确保阀组启闭响应灵敏。
3. **材料性能分析** 利用硬度计、金相显微镜对泵筒和柱塞的基体材料进行硬度测试(洛氏硬度HRC≥55)及金相组织观察,确认是否存在热处理缺陷。同时通过盐雾试验、电化学腐蚀试验评估材料耐腐蚀性,避免因点蚀或应力腐蚀导致的早期失效。
运动特性与表面质量检测
4. **运动配合试验** 在模拟工况下运行抽油泵,使用高速摄像机和振动传感器记录柱塞往复运动的平稳性,分析是否存在卡滞或异常摩擦。通过激光测距仪实时监测柱塞行程误差,确保冲程损失率低于3%。
5. **表面粗糙度与缺陷检测** 采用表面粗糙度仪测量泵筒内壁Ra值(一般要求≤0.4μm),保障润滑膜的有效形成。结合磁粉探伤(MT)或超声波探伤(UT)技术,排查泵筒焊接部位、阀罩等区域的裂纹、气孔等缺陷。
综合评定与维护建议
检测完成后需生成包含数据对比、失效模式分析及剩余寿命预测的报告。对于轻微磨损的柱塞可建议表面镀铬修复,严重变形的泵筒则需整体更换。同时提出优化注油频率、调整冲次参数等操作建议,确保抽油泵在最佳工况下运行。
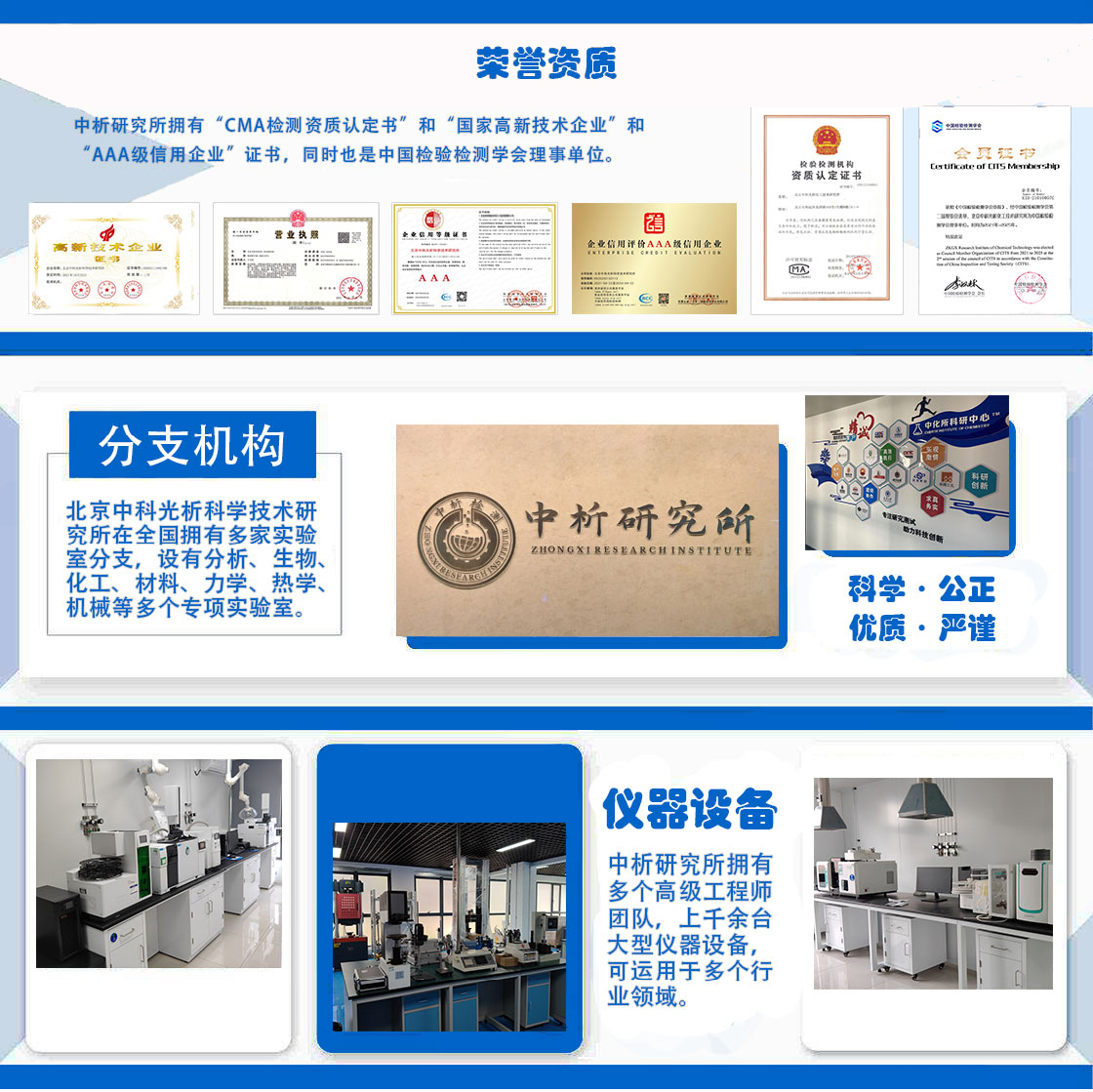
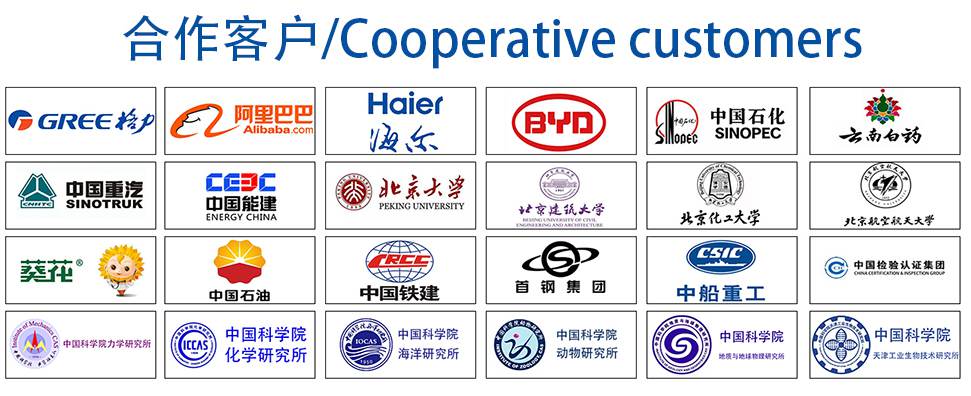