抽油杆及组件在石油开采中的重要性
抽油杆作为机械采油系统的核心传动部件,承担着将地面动力传递至井下泵筒的重要功能。在持续往复运动和复杂工况下,抽油杆及其接箍、螺纹等组件承受着交变载荷、腐蚀介质和极端温度的多重考验。据统计,油田每年因抽油杆失效导致的停机损失超过12亿美元,其中80%的事故源于检测不及时或标准执行偏差。为保障油气生产安全、延长设备使用寿命,建立科学的抽油杆及组件检测体系已成为石油行业的基础性技术规范。
核心检测项目与技术指标
1. 表面质量检测
采用磁粉探伤(MT)和超声波探伤(UT)相结合的方式,重点检查杆体表面裂纹、腐蚀坑、机械损伤等缺陷。对杆端螺纹区域进行100%渗透检测,确保螺距误差不超过±0.02mm,牙型角偏差控制在±1°范围内。
2. 几何尺寸检测
使用激光测量仪和专用量规对抽油杆直径、直线度、椭圆度进行三维扫描,杆体直径允许偏差为±0.15mm,全长直线度误差≤2mm/m。接箍外径尺寸需符合API 11B标准,内螺纹锥度误差不得超过1:16±0.0003in/in。
3. 材料性能检测
通过拉伸试验机测定抗拉强度(≥965MPa)、屈服强度(≥795MPa)和延伸率(≥10%),冲击试验评估-20℃低温韧性(≥27J),硬度检测确保HRC值在22-32区间。采用金相显微镜分析显微组织,杜绝过热、脱碳等冶金缺陷。
4. 装配质量检测
使用扭矩测试仪验证接箍装配扭矩(参考API 11BX标准),配套电子塞规检测螺纹配合紧密度。对组装后的抽油杆进行0.6MPa压力密封测试,确保30分钟内压降不超过初始值的5%。
5. 无损检测新技术应用
引入相控阵超声检测(PAUT)实现缺陷三维成像,电磁涡流检测(ECT)快速筛查表面微裂纹。采用数字射线检测(DR)技术对修复区进行壁厚测量,检测精度可达±0.1mm,较传统方法提升40%效率。
检测周期与维护策略
根据API RP 11BR规范,常规检测应每12个月实施全项目检测,高强度作业井需缩短至6个月。建立基于大数据的剩余寿命预测模型,当累计行程超过500万次或杆体腐蚀减薄量达到原始壁厚10%时,强制进入修复/更换流程。
标准化检测流程的意义
完整的检测体系可使抽油杆故障率降低65%,平均使用寿命延长至5-7年。通过精确识别早期缺陷,避免因杆断造成的井下事故,单井年维护成本可节约12-18万元。目前国际主流油服公司已普遍推行数字化检测报告系统,实现全生命周期质量追溯。
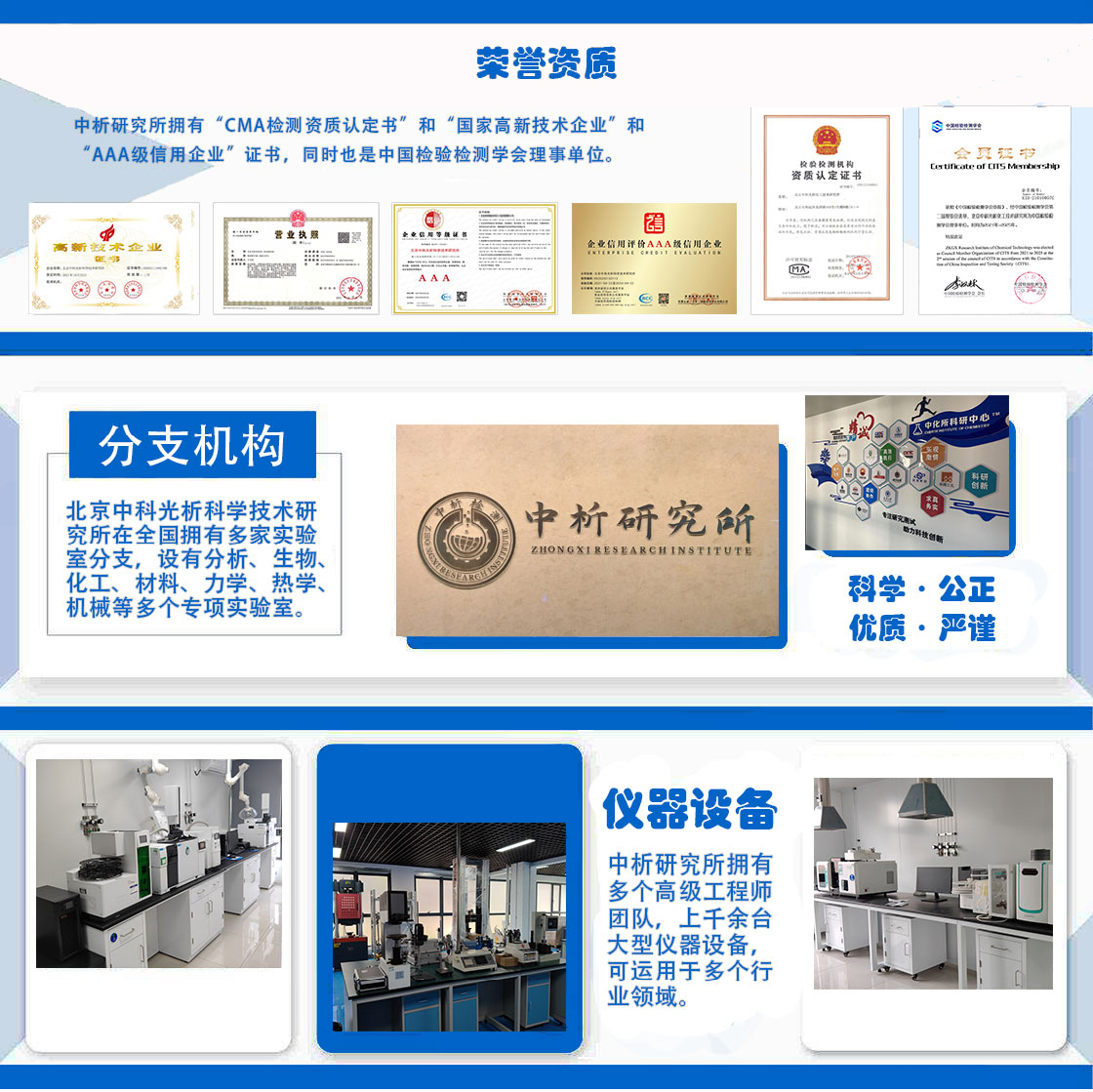
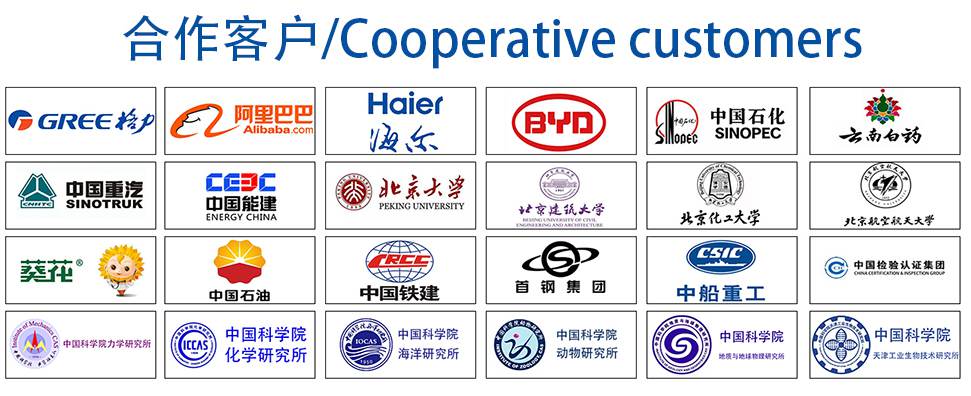