石油修井用动力钳检测的重要性与核心项目
在石油修井作业中,动力钳作为关键设备之一,承担着管柱连接、拆卸及扭矩控制等重要任务。其性能直接关系到作业效率、人员安全和设备使用寿命。由于动力钳长期处于高压、高负荷及复杂工况下运行,若出现故障可能导致严重事故。因此,定期开展动力钳的专业检测是石油行业设备管理中不可或缺的环节。通过系统化的检测,可有效预防设备失效、优化维护策略,并确保其符合API(美国石油学会)及行业安全标准要求。
石油修井用动力钳的核心检测项目
1. 外观与结构完整性检测
检测人员需对动力钳的壳体、钳头、传动部件进行目视检查,确认是否存在裂纹、变形或腐蚀现象。同时检查螺栓连接紧固性、防护罩完整性及润滑系统密封性,确保设备整体结构无安全隐患。
2. 扭矩性能测试
通过专业扭矩测试仪模拟实际工况,检测动力钳的**最大输出扭矩**、**扭矩精度**及**稳定性**。需对照设备铭牌参数,验证其是否满足API SPEC 7K标准要求的±5%误差范围,并记录不同转速下的扭矩波动值。
3. 液压系统检测
检查液压泵、马达和阀组的运行状态,测试系统压力是否达到设计值(通常为10-35MPa)。通过流量计监测液压油循环效率,分析是否存在内泄或堵塞问题。同时检测液压油清洁度及油温控制功能,确保系统响应灵敏且无异常噪音。
4. 安全装置功能验证
重点测试动力钳的过载保护装置、紧急制动系统及防反转机构。在模拟超负荷工况下,确认安全阀能否及时泄压,制动响应时间是否小于0.5秒,并验证防反转锁止功能的可靠性。
5. 关键零部件磨损检测
使用超声波测厚仪测量钳牙、齿轮、轴承等易损件的磨损量,结合三维扫描技术分析齿面啮合精度。对于磨损量超过允许值(通常为原始尺寸的3%-5%)的部件,需立即更换以保证动力钳的夹持力与传动效率。
6. 操作控制系统检测
对动力钳的远程控制模块、传感器及PLC系统进行联调测试,验证操作指令的传输延迟是否在50ms以内。同时检查故障报警系统的灵敏性,确保压力异常、温度过高等情况能触发准确声光警示。
7. 综合耐久性测试
通过连续运行试验模拟实际工况循环,监测设备在持续作业下的性能衰减情况。要求动力钳在额定载荷下连续运行4小时以上,关键部位温升不超过45℃,且无漏油、异响等异常现象。
结语
石油修井用动力钳的检测需遵循全生命周期管理理念,建议每季度开展一次常规检测,大修后或作业环境突变时需增加专项检测频次。通过科学的检测数据分析,可建立设备健康档案,预测剩余寿命,为油田安全生产提供坚实保障。同时,检测结果应作为设备维修、改造或报废决策的重要依据,推动石油装备管理向数字化、智能化方向发展。
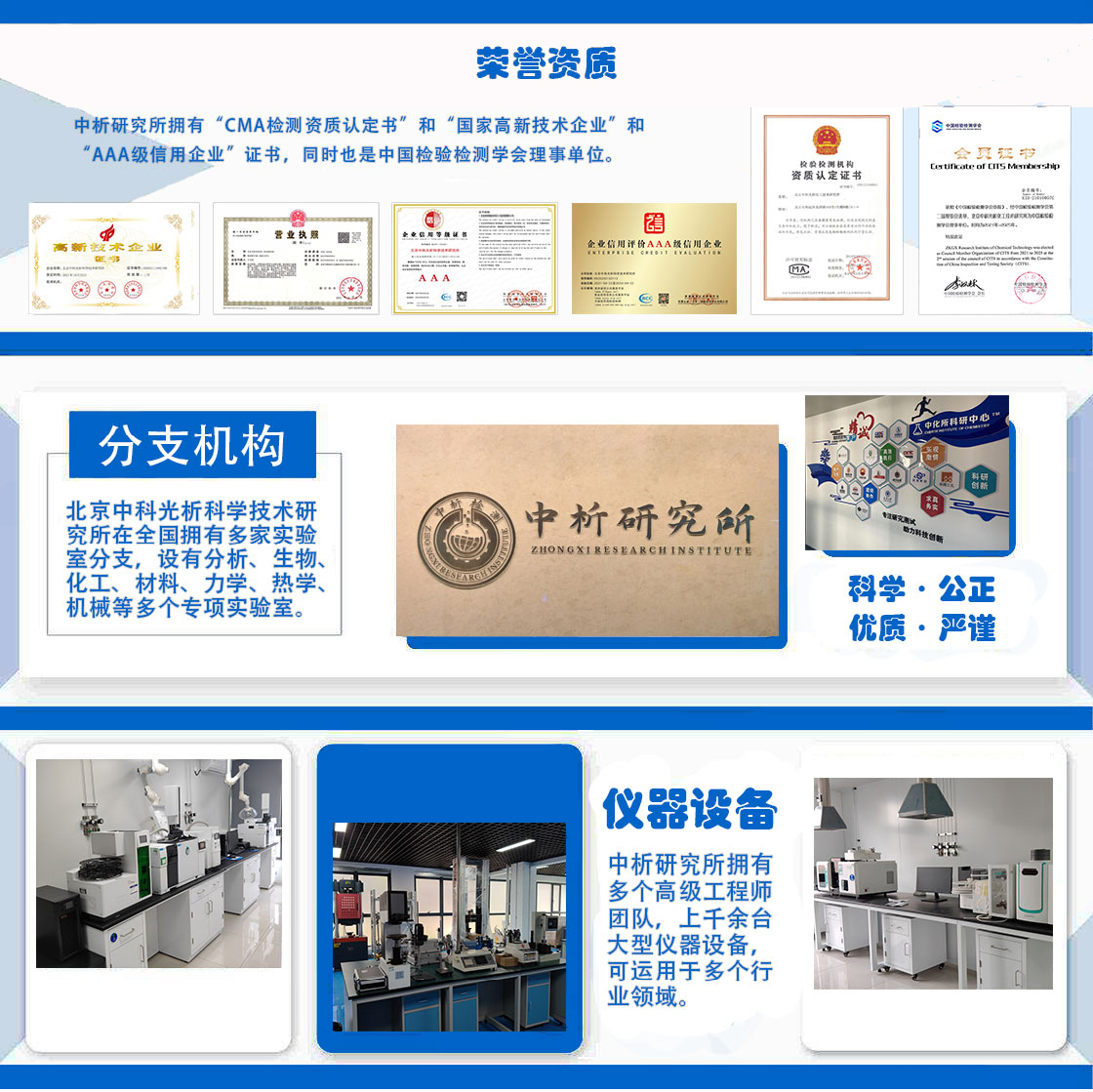
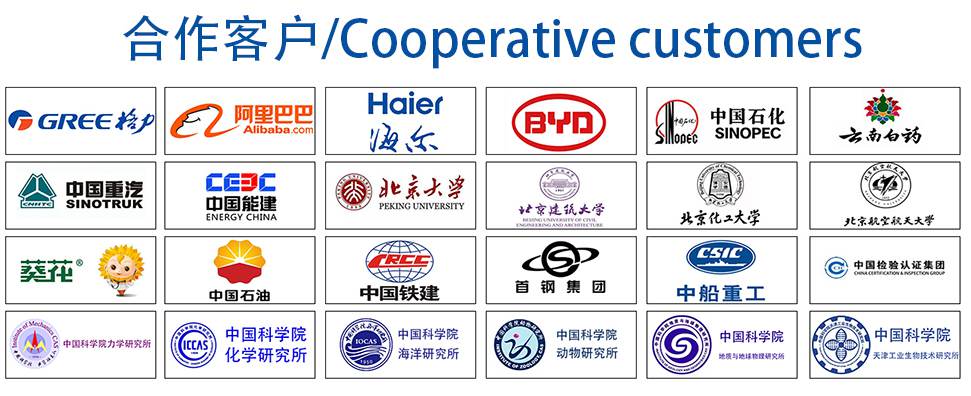