自动分检衡器检测的重要性与技术要点
自动分检衡器作为现代工业生产与物流分拣领域的核心设备,其精准性和可靠性直接影响产品质量、生产效率和成本控制。这类设备通过集成称重、分类、数据传输等功能,广泛应用于食品加工、快递物流、医药制造及化工原料等行业。为确保其长期稳定运行并符合行业标准,定期开展全面的检测项目是必要流程。检测不仅能验证设备的计量性能,还能发现潜在问题,避免因误差累积导致的经济损失或安全隐患。
检测项目一:计量性能校准
作为衡器的核心功能,称重精度检测是首要环节。检测时需使用标准砝码对静态和动态称重模式分别测试:在静态模式下验证零点漂移、线性误差和重复性指标;动态模式下模拟实际物料流动状态,评估设备在连续分拣过程中的响应速度和误差范围。根据OIML R51国际建议,最大允许误差(MPE)需控制在物料标称值的0.1%-1.5%之间。
检测项目二:分拣机构效能验证
自动分检衡器的核心价值在于准确分类不同质量区间的物品。检测需涵盖分拣动作的触发灵敏度、机械臂或推杆的执行精度,以及高速运行下的误判率。通过设置不同重量阈值(如500g±5g、1kg±10g),统计设备在1小时连续作业中的正确分拣次数与错误动作次数,确保其分拣准确率高于99.5%。
检测项目三:环境适应性测试
针对设备实际运行环境,需模拟高温(+50℃)、低温(-10℃)、湿度(90%RH)、振动(5-50Hz)等极端条件,持续监测称重系统的稳定性。特别是在冷链物流或粉尘车间等特殊场景中,需额外验证防潮、防震、抗干扰等防护设计的有效性。
检测项目四:数据追溯与系统集成
现代自动分检衡器多与MES、ERP系统联网,检测需包含数据采集完整性和传输稳定性评估。通过模拟发送1000组连续称重数据,检查时间戳准确性、数据丢失率及异常值告警功能。同时需验证设备接口协议(如MODBUS、Profinet)与工厂控制系统的兼容性。
检测项目五:安全防护功能核查
针对设备机械运动部件和电气系统,需进行急停按钮响应测试、过载保护触发试验以及绝缘电阻检测(≥10MΩ)。在金属探测功能集成的机型中,还需验证异物识别的灵敏度和剔除动作的同步性。
周期性维护与检测计划制定
建议企业建立三级检测体系:每日运行前进行零点校准与分拣动作自检;每月开展标准砝码比对测试;每年由法定计量机构实施强制检定。检测数据应形成电子化档案,通过趋势分析预判传感器老化、机械磨损等潜在风险。
通过系统化的检测流程,企业不仅能确保自动分检衡器持续满足生产需求,更能通过数据优化分拣策略,在质量控制与成本控制之间实现精准平衡。
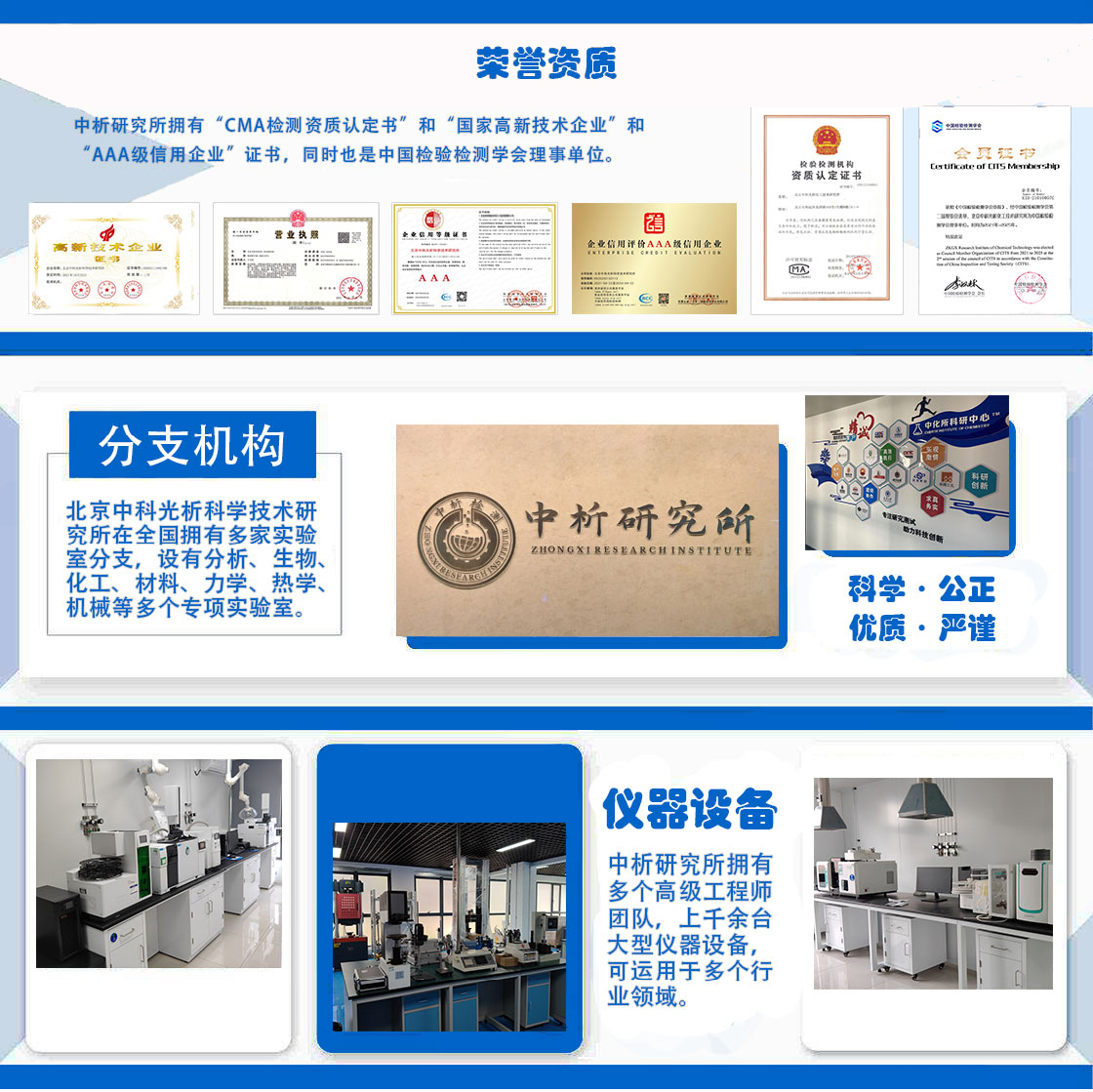
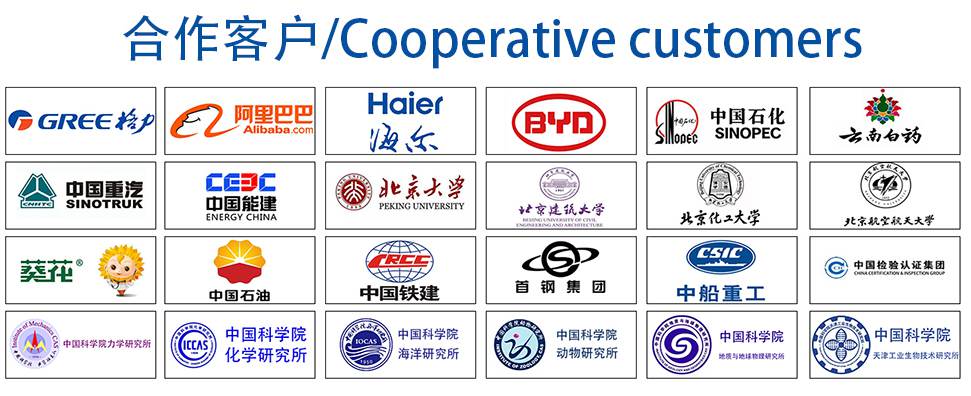