整机性能检测:全方位保障设备效能的核心手段
整机性能检测是通过系统化测试流程对计算机、工业设备或智能终端的综合运行能力进行量化评估的过程。在电子产品迭代加速、工业设备智能化升级的背景下,这项检测成为衡量设备可靠性、发现潜在缺陷、验证技术参数的核心手段。无论是新机组装后的出厂检验、二手设备的性能评估,还是使用过程中的定期维护,整机性能检测都能通过多维度的数据指标,精准呈现设备当前状态,为使用者提供决策依据。
核心检测项目解析
1. 硬件性能基准测试
通过运行Cinebench、3DMark等专业测试软件,对CPU多核运算能力、GPU图形渲染性能、内存读写速度进行量化评估。存储设备需使用CrystalDiskMark检测连续/随机读写性能,同时验证NVMe协议支持情况。检测过程中需关注硬件温度曲线,确保各组件在持续负载下不超过安全阈值。
2. 系统稳定性压力测试
使用Prime95、AIDA64等工具进行72小时不间断压力测试,模拟极端工作负载。重点观察是否出现蓝屏、死机、进程崩溃等异常现象,记录系统资源占用率波动曲线。工业设备还需增加振动测试模块,检测机械结构在长期运行中的稳定性。
3. 散热效能评估体系
通过红外热成像仪配合HWMonitor软件,建立三维温度分布图谱。测试需包含空载、满载、动态负载三种状态,评估散热模组的导热效率与风道设计合理性。笔记本电脑需额外检测散热系统噪音值,确保符合人体工程学标准。
4. 能效比综合测算
使用高精度功率计测量整机在不同工作模式下的功耗,结合性能测试数据计算能效比值。服务器设备需着重检测电源转换效率,确保80Plus金牌以上认证标准;移动设备则需评估单位电量下的续航表现。
5. 兼容性验证矩阵
构建包含主流操作系统、驱动程序、外设接口的测试环境,验证硬件组件的兼容范围。重点检测PCIe通道分配、USB协议支持、多屏输出稳定性等关键项目,对工业控制设备还需测试与PLC、传感器等专业硬件的协作能力。
智能检测的技术演进
随着AI技术的渗透,现代整机检测开始引入机器学习算法。通过建立设备性能数据库,系统可自动识别异常数据模式,实现故障预判。部分高端检测平台已支持自动化测试脚本生成,能够根据设备配置自动适配最优检测方案,将传统需要数天完成的检测流程压缩至6-8小时。
规范的整机性能检测不仅能够延长设备使用寿命,更能通过量化数据帮助用户实现精准的性能调优。建议每季度执行基础检测,在系统重大更新或硬件改动后必须进行完整检测,确保设备始终处于最佳运行状态。
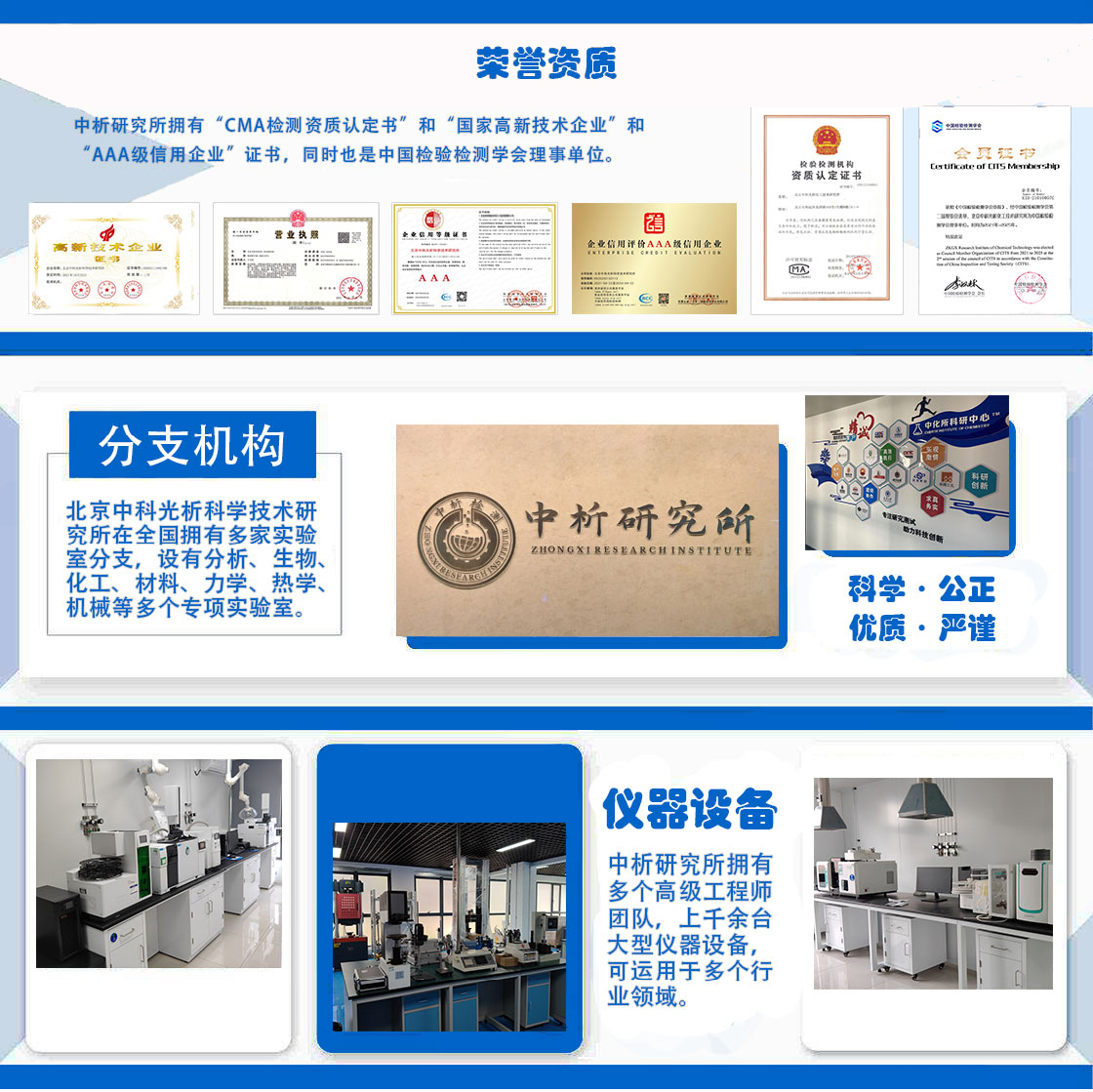
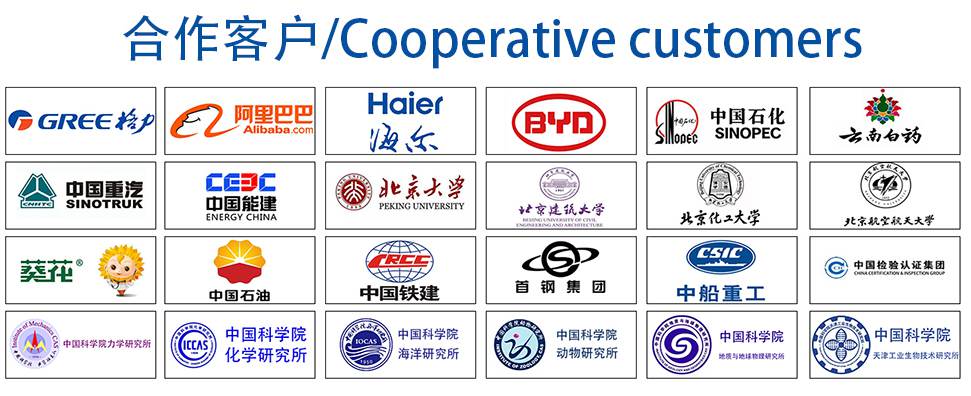