泥浆泵双金属缸套检测的重要性与实施方法
泥浆泵双金属缸套作为石油钻井、矿山开采等领域的关键部件,其性能直接影响设备运行效率和使用寿命。由于长期处于高压、高温、强磨损和腐蚀性介质的工作环境中,缸套易出现内壁磨损、金属层剥离、裂纹等缺陷。通过科学系统的检测手段,可有效评估其服役状态,预防突发故障,降低维护成本。本文将围绕双金属缸套的核心检测项目展开详细说明。
一、关键检测项目及方法
1. 尺寸精度检测
使用三坐标测量仪或激光扫描设备对缸套内径、外径、同心度等几何参数进行测量,误差需控制在±0.05mm以内。重点关注缸套与活塞配合面的尺寸匹配性,确保密封性能。
2. 表面质量检测
采用磁粉探伤(MT)或渗透探伤(PT)检查表面裂纹;通过粗糙度仪测试内壁Ra值(一般要求≤0.8μm),并使用显微镜观察镀层均匀性,避免存在气孔、夹杂等缺陷。
3. 材料成分分析
利用光谱仪对基体(通常为球墨铸铁)和耐磨层(多为高铬合金)进行成分检验,确保碳、铬、钼等元素的含量符合GB/T 9439、ASTM A532标准要求。
4. 硬度梯度测试
采用显微硬度计从内壁耐磨层到基体进行多点测量,典型要求为:表面硬度≥58HRC,过渡区硬度梯度平缓(变化率<5HRC/mm),基体硬度控制在28-32HRC。
5. 结合强度检测
通过剪切试验或热震试验验证双金属界面结合力,剪切强度应≥220MPa。热震试验需在300℃温差下循环5次无剥离现象。
6. 密封性能试验
在专用压力测试台上进行液压密封测试,加载压力为额定工作压力的1.5倍(通常≥35MPa),保压30分钟无渗漏,同时监测变形量是否超标。
二、进阶检测技术应用
1. 金相组织分析
通过金相显微镜观察基体珠光体含量(需>95%)和碳化物分布状态,评估热处理工艺有效性。耐磨层应呈现细小弥散的M7C3型碳化物组织。
2. 超声波无损检测
采用相控阵超声波技术(PAUT)检测缸套内部结合面缺陷,可发现深度≥0.5mm的分层缺陷,检测精度较传统UT提高40%以上。
3. 台架模拟试验
在模拟工况下进行500小时连续运转测试,监测温度、振动、泄漏量等参数,评估实际工况下的耐磨性能(磨损量≤0.15mm/1000h)。
三、检测周期与标准依据
新制缸套需进行全项目检测,服役中的缸套应每2000小时进行尺寸复测和表面探伤。检测标准主要参照API 7C-11F、SY/T 6422-2018以及ISO 13709等规范,确保检测结果具有国际可比性。
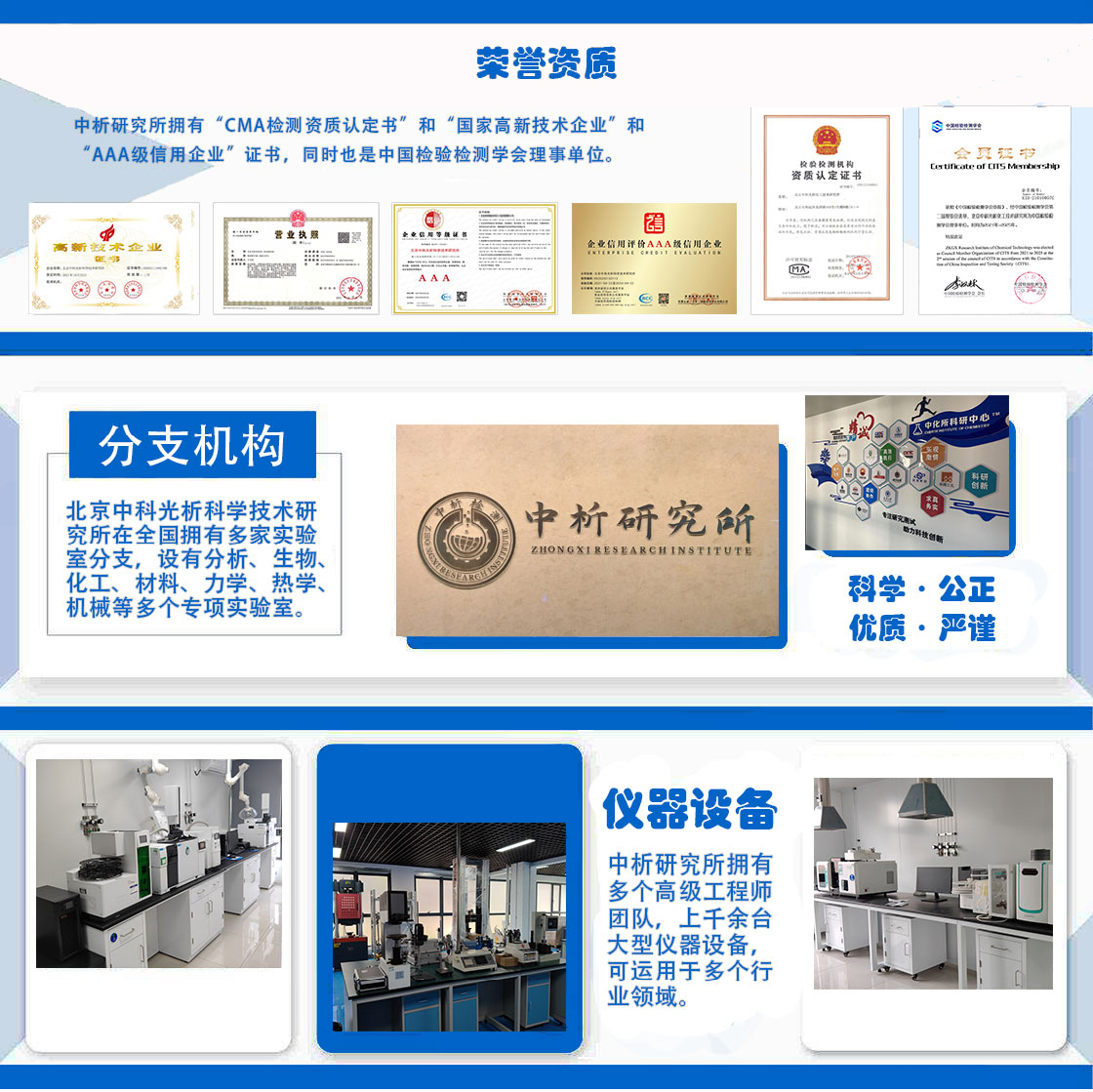
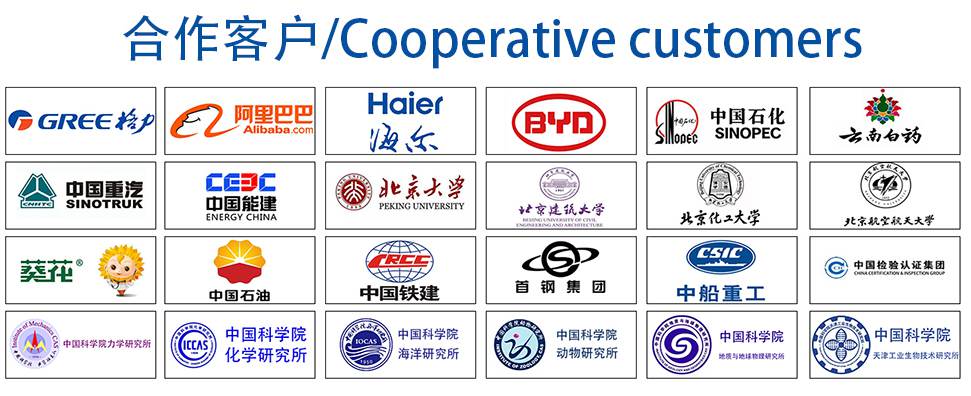