油气井用射孔枪检测的重要性与核心内容
油气井用射孔枪作为石油天然气开采的关键工具,其性能直接关系到井下作业的安全性和油气产能效率。射孔枪的主要作用是通过高能炸药或聚能射流在套管、水泥环及地层中形成稳定的油气流通通道。受高温、高压、腐蚀性介质等多重复杂环境影响,射孔枪需具备极高的机械强度、密封性和抗疲劳能力。因此,定期开展系统化检测是保障设备可靠性、延长使用寿命、避免井筒事故的必要手段。检测工作需覆盖材料特性、结构完整性、功能稳定性等多个维度,并通过标准化流程确保结果的可追溯性。
核心检测项目与技术要求
1. 材料性能检测
射孔枪主体材料的力学性能与耐腐蚀性是检测重点,需通过化学成分分析、拉伸试验、冲击韧性测试验证钢材是否符合API 5CT标准。针对高温高压井,还需进行金相组织观察和H2S应力腐蚀试验(NACE TM0177),确保材料在硫化氢环境下的稳定性。
2. 结构尺寸精度检测
使用三维激光扫描仪或高精度卡尺对枪体外径、壁厚、螺纹参数进行全尺寸测量,偏差需控制在±0.1mm以内。孔眼排列角度、间距及深度需通过数字化投影仪验证,确保射孔弹起爆后形成的孔道满足设计流量要求。
3. 密封性能测试
采用水压试验机对组装后的射孔枪进行分级加压,最高压力需达到额定工作压力的1.5倍(ASTM D3967)。保压30分钟后检查焊缝、螺纹连接处是否渗漏,并配合氦质谱检漏仪检测微泄漏量(≤1×10^-7 Pa·m³/s)。
4. 动态性能模拟试验
在高温高压试验舱中模拟井下环境(温度150℃、压力80MPa),通过高速摄像机记录射孔弹起爆瞬间的冲击波传播路径,分析枪体形变量是否超出安全阈值(≤0.5%)。同步监测射流穿透深度和孔径均匀性,确保破岩效率达标。
5. 安全性能综合评估
包含抗爆能力测试(GB/T 228.1)、残余应力检测(X射线衍射法)及爆炸后残渣清理难度评估。重点检查盲孔端部应力集中区域,避免发生脆性断裂风险,同时验证哑弹率是否低于行业标准0.3%。
检测数据管理与应用
所有检测结果需录入MES系统生成数字化报告,结合ISO 9001质量体系进行统计过程控制(SPC)。对于失效样品,须采用扫描电镜(SEM)和能谱分析(EDS)追溯失效机理,为工艺改进提供数据支持。通过检测数据的长期积累,可建立射孔枪全生命周期预测模型,实现预防性维护管理。
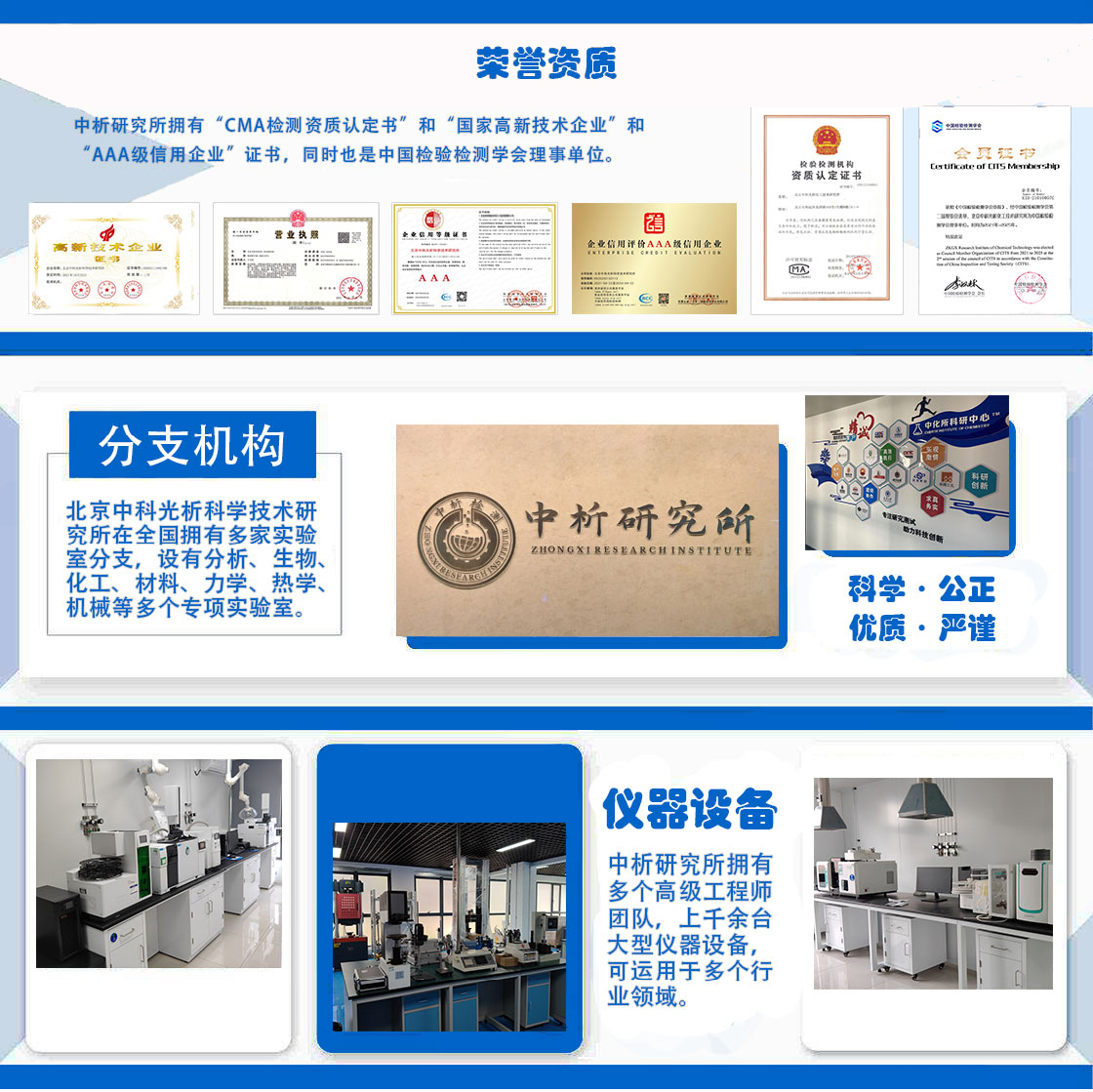
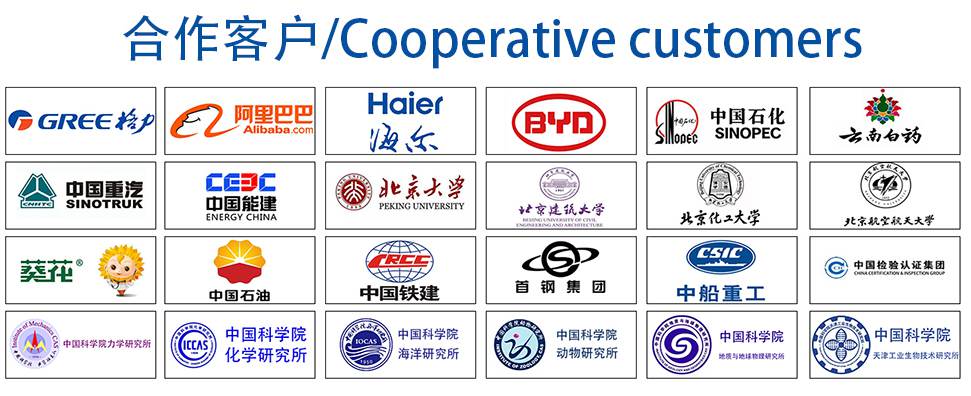