特殊取心工具检测的重要性与技术要点
在地质勘探、油气开发及矿产资源勘查领域,特殊取心工具是获取地下岩层原始样本的核心装备。其性能直接影响岩心质量、作业效率及数据可靠性。由于取心工具需在高温高压、强腐蚀性等复杂工况下运行,针对其关键参数的检测成为保障作业安全、延长工具寿命的核心环节。根据行业统计,约30%的井下事故与取心工具性能失效直接相关,因此建立系统化的检测体系对降低勘探风险、提升数据精度具有重要意义。
核心检测项目详解
1. 机械性能检测
通过万能材料试验机进行抗拉强度(≥900MPa)和屈服强度测试,使用布氏硬度计检测表面硬度(HRC38-42)。重点关注工具接头的疲劳寿命,模拟井下振动工况进行500万次循环载荷测试,确保结构完整性。
2. 密封系统检测
采用氦质谱检漏仪进行气密性测试,泄漏率需≤1×10-7 Pa·m3/s。高压密封测试在35MPa压力下持续2小时,结合温度循环试验(-20℃至150℃),验证O型圈与金属密封的复合密封效能。
3. 切削结构检测
使用三坐标测量仪对PDC齿/孕镶金刚石排列进行0.01mm级精度检测,确保切削剖面角度误差≤0.5°。运用数字图像相关技术(DIC)分析岩心抓取机构的应力分布,优化卡簧片接触压力均匀性。
4. 动态特性检测
在模拟井筒装置中开展多轴振动测试,频率范围覆盖5-200Hz,通过加速度传感器采集振动谱图。重点监测工具共振点,要求避开常规钻井转速对应的20-120Hz危险频段。
5. 耐腐蚀检测
参照NACE TM0177标准进行硫化氢应力腐蚀试验,在H2S分压0.1MPa、pH3.5的模拟溶液中持续720小时。同时进行电化学阻抗谱(EIS)分析,评估涂层在Cl-浓度20万ppm环境中的防护效能。
智能化检测技术应用
引入工业CT断层扫描技术,实现取心筒体内部结构的非破坏性检测,可识别≥0.1mm的隐性裂纹。结合数字孪生技术构建工具全生命周期模型,通过应力场仿真预测薄弱环节,检测效率提升40%以上。
特殊取心工具的检测体系正朝着多参数耦合检测方向发展,通过集成声发射监测、微应变传感等新技术,构建涵盖设计验证、制造质控、现场维护的全流程检测方案,为复杂地层勘探提供可靠保障。
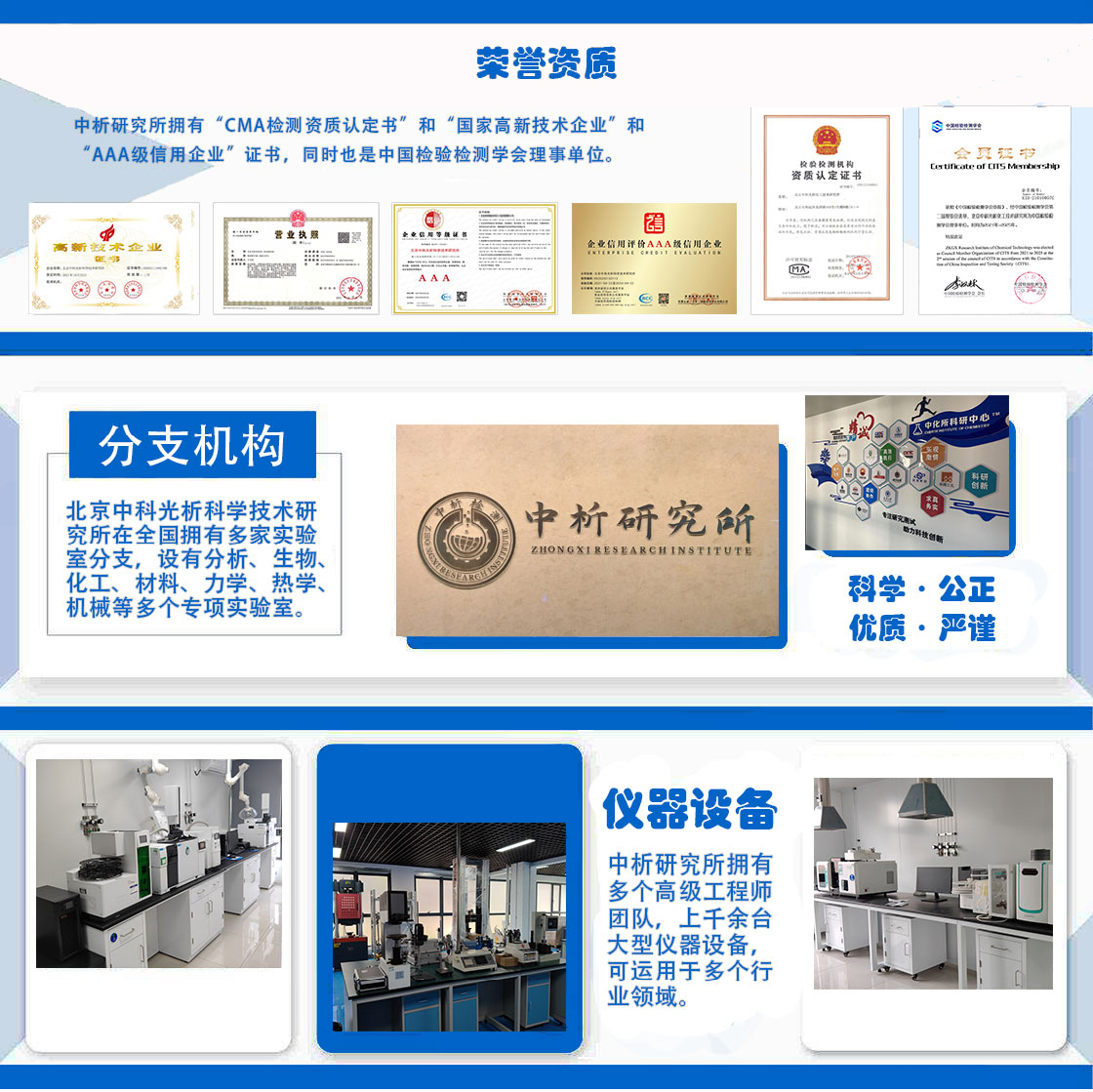
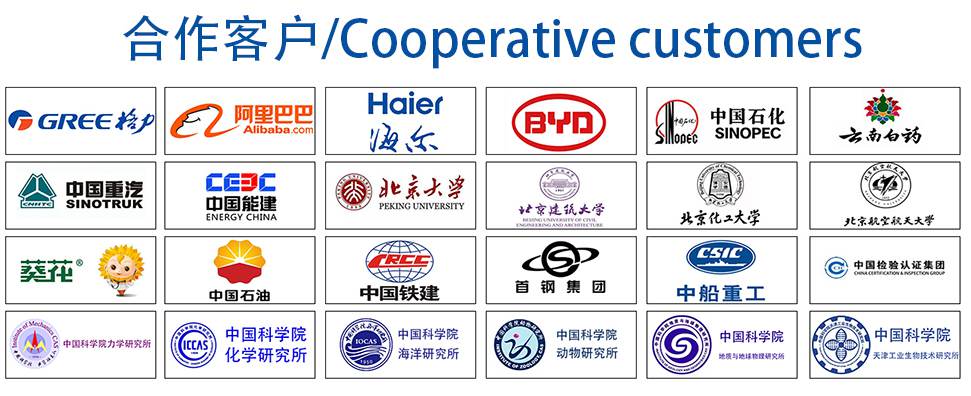