制动蹄组件检测的重要性与技术要求
制动蹄组件作为车辆制动系统的核心部件,直接关系行车安全与制动效能。其结构由制动蹄片、摩擦材料、铆接/黏接组件及支撑机构组成,在高温、高压、高频振动的工况下需保持稳定性能。根据GB 5763-2018《汽车用制动器衬片》及ISO 26867摩擦材料测试标准,专业检测需覆盖材料特性、机械强度、耐久性等20余项关键指标,确保制动蹄组件在紧急制动、连续坡道等极端场景下不发生断裂、变形或摩擦系数突变。
主要检测项目体系
1. 外观与尺寸检测
使用三维影像测量仪对制动蹄弧度半径(公差±0.15mm)、蹄片厚度(误差≤0.5mm)进行数字化检测,配合磁粉探伤排查表面裂纹。重点检查摩擦材料与背板结合处,要求黏接面积≥95%,边缘溢胶宽度≤1.5mm,确保无分层现象。
2. 摩擦材料性能测试
依据SAE J661标准,在克劳斯试验机上模拟0-300℃温变环境,检测摩擦系数(μ≥0.35)、磨损率(≤0.5cm³/MJ)。通过能谱分析仪验证材料配方,确认无石棉成分,重金属含量符合ECE R90法规要求。
3. 力学性能试验
使用100kN伺服液压试验机进行三点弯曲测试,背板抗弯强度需>480MPa。振动疲劳试验模拟20万次制动循环后,铆钉剪切强度衰减应<15%,螺栓预紧力矩保持90%以上初始值。
4. 热力学特性验证
在热冲击试验箱中执行-40℃至350℃的100次循环测试后,组件变形量需<0.3mm。红外热像仪监测制动过程温度场分布,摩擦表面热点温差应控制在50℃以内,避免局部过热导致热衰退。
5. 环境适应性检测
盐雾试验箱模拟沿海气候,240小时测试后金属件锈蚀面积<5%。泥水喷射试验验证泥沙侵入防护性能,制动效能下降幅度需≤8%。同步进行湿热老化试验(85℃/85%RH),确保橡胶件无硬化龟裂。
智能检测技术应用
新型检测体系引入AI视觉检测系统,通过卷积神经网络识别微米级表面缺陷,检测效率提升3倍。激光位移传感器实现0.01mm精度的动态形变监测,配合大数据平台建立质量预测模型,使不良品拦截率提升至99.7%。
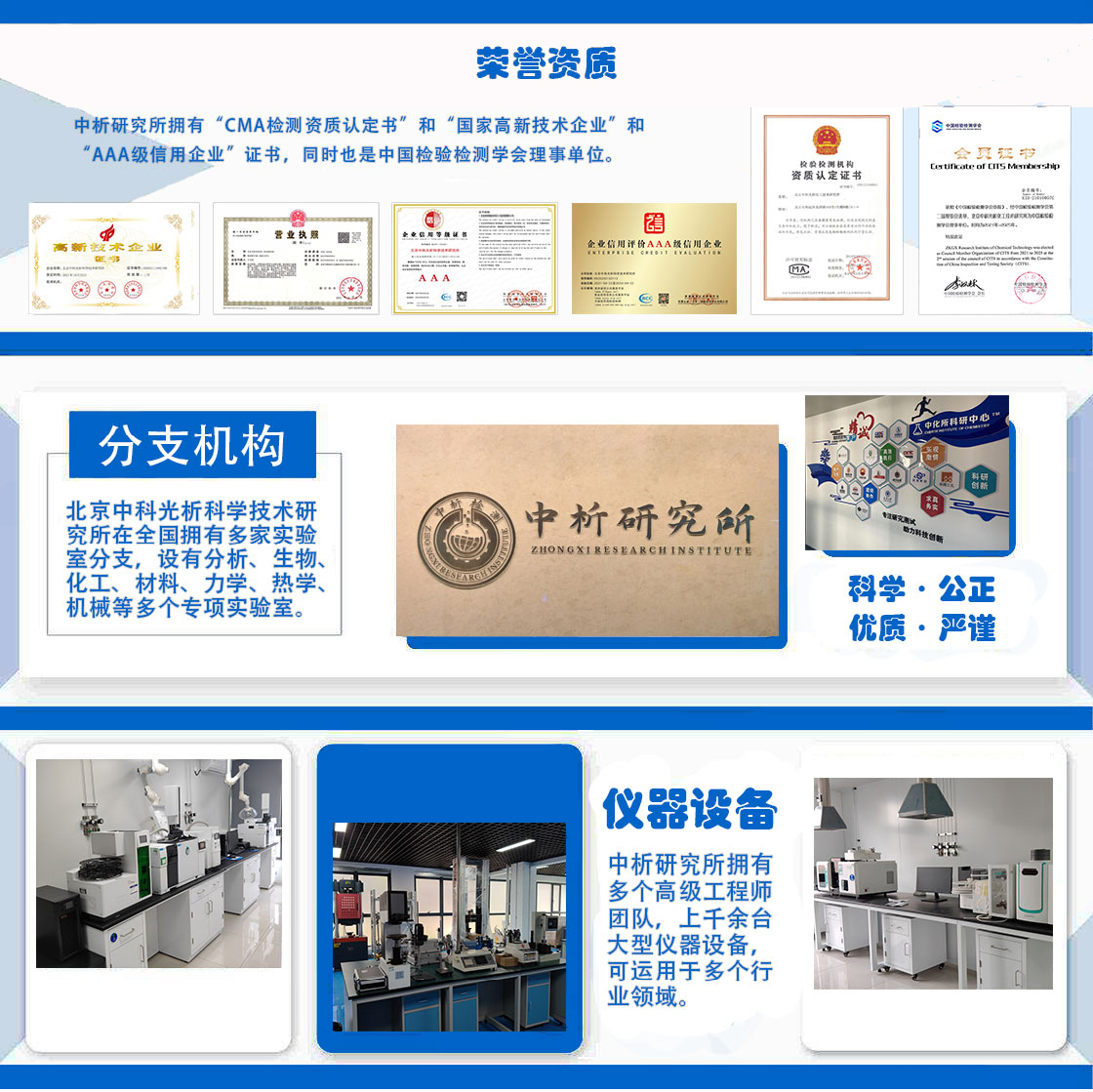
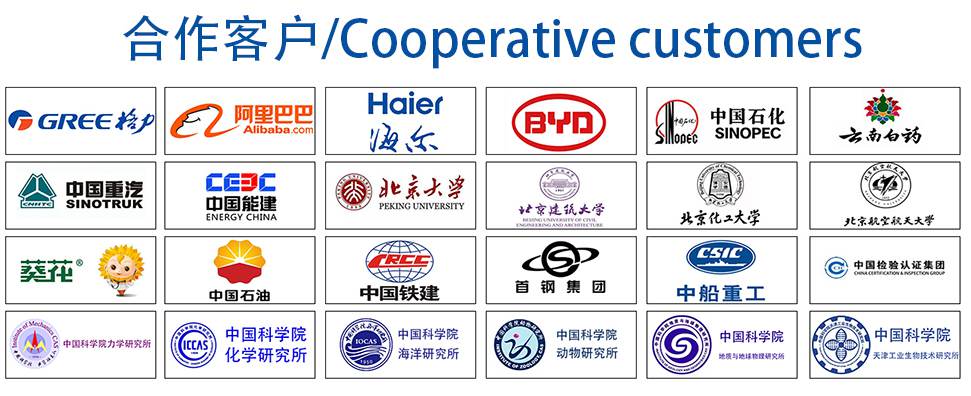