泵类及液体输送系统节能监测检测的重要性
泵类及液体输送系统是工业生产中能耗占比最高的设备之一,广泛应用于化工、电力、市政供水和石油开采等领域。据统计,泵类设备的电力消耗占工业用电量的20%-25%,其中约30%的能源因系统设计不合理、运行效率低下或维护不当而被浪费。因此,针对泵类及液体输送系统开展节能监测检测,不仅是降低企业运营成本的关键举措,更是实现“双碳”目标的重要技术支撑。通过系统化的检测手段,能够精准识别能耗异常点,优化设备运行参数,并为节能改造提供科学依据。
核心检测项目及方法
1. 运行效率测试
采用GB/T 13469-2021《离心泵系统经济运行要求》标准,通过超声波流量计、压力传感器和功率分析仪,实时测量泵的流量、扬程、输入功率及效率。重点对比实际效率与额定效率的差异,若偏差超过10%则判定为低效运行,需进行叶轮磨损检查或电机匹配性分析。
2. 流量-扬程匹配度评估
结合工艺需求曲线与泵性能曲线,分析系统是否存在“大马拉小车”现象。若检测发现泵长期运行在额定流量的60%以下,需评估安装变频调速装置或更换多级泵的可行性,同时检查阀门开度是否合理以减少节流损失。
3. 变频调速系统效能验证
对已安装变频器的系统,需检测其控制逻辑是否与负载变化同步,并利用电能质量分析仪测量谐波含量及功率因数。要求变频器在40%-80%负载率区间运行时,综合节电率不低于15%,否则需重新设定PID参数或优化控制策略。
4. 管道系统阻力检测
使用压差变送器分段测量管道沿程阻力和局部阻力,重点关注弯头、变径管件及过滤器的压降。若总阻力超过设计值的20%,需排查结垢、堵塞问题,或重新计算管径匹配性。建议结合CFD模拟优化管道布局,降低湍流损失。
5. 密封与润滑状态监测
通过红外热像仪检测机械密封部位温度分布,配合振动分析仪识别轴承异常磨损。要求填料密封泄漏量≤50mL/min,机械密封泄漏量≤5mL/min。同时定期取样检测润滑油黏度、水分及颗粒污染物,确保摩擦功耗在允许范围内。
6. 能源管理系统集成度评价
核查系统是否配备能耗数据采集模块,并具备趋势分析、能效对标和报警功能。重点验证数据采样频率(不低于1次/分钟)及历史数据存储周期(≥3年),确保满足ISO 50001能源管理体系要求。
检测结果应用与优化建议
基于检测数据生成能效诊断报告,明确节能潜力点并提出分级改造方案:优先实施零成本措施(如调整运行工况),其次推进变频改造或高效泵替换(投资回收期<3年),最后规划系统级优化(如管网拓扑重构)。通过周期性复测验证节能效果,建立动态能效管理机制。
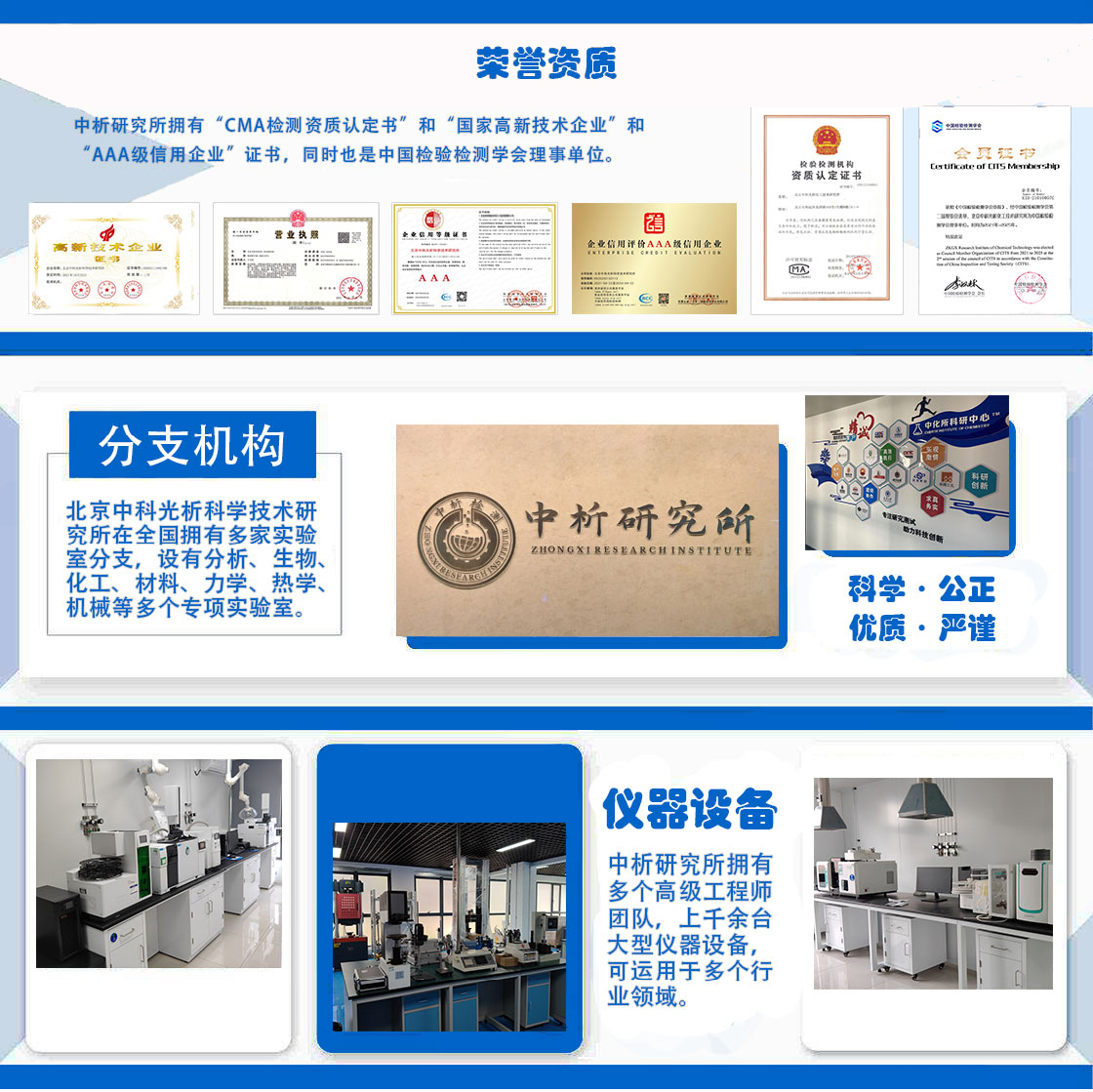
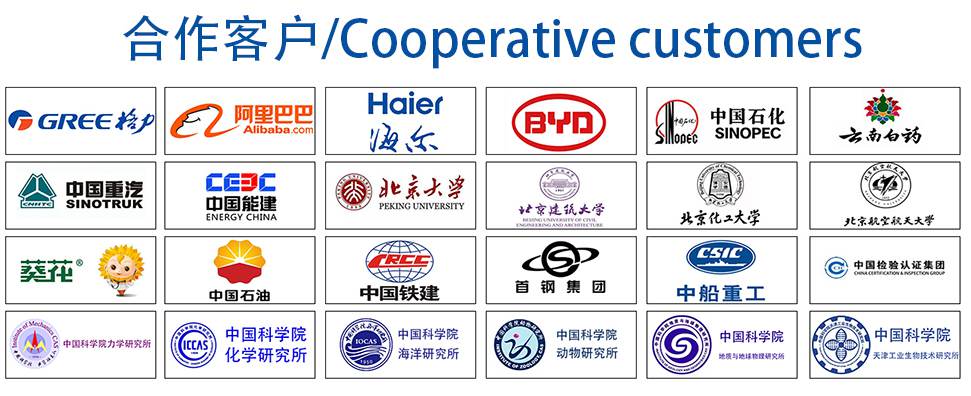