三相异步电动机经济运行检测的意义与背景
三相异步电动机作为工业生产中应用最广泛的动力设备之一,其能效水平直接关系到企业的能源消耗和运营成本。据统计,电动机系统占工业总用电量的60%以上,而低效运行状态可能导致能源浪费高达20%-30%。因此,开展三相异步电动机经济运行检测,既是实现“双碳”目标的关键举措,也是企业降本增效的重要途径。通过科学的检测与评估,可精准识别电动机运行状态偏差,优化负载匹配,延长设备寿命,并为节能改造提供数据支撑。
检测项目与关键参数分析
1. 输入功率与输出功率检测
使用电能质量分析仪或功率计测量电动机的实际输入功率,同时结合扭矩传感器和转速仪计算输出机械功率。重点对比额定工况与实际工况的差异,要求输入功率偏差不超过±5%,输出功率需满足设备工艺需求。
2. 效率检测与能效等级判定
通过公式η=(输出功率/输入功率)×100%计算电动机运行效率,对照GB 18613《电动机能效限定值及能效等级》标准,判断是否符合IE3或IE4等级要求。检测时需记录不同负载率(25%、50%、75%、100%)下的效率曲线变化。
3. 功率因数与无功补偿评估
利用功率因数表测量电动机运行时的功率因数,正常工况下应≥0.85。若检测值偏低,需分析供电电压稳定性及无功补偿装置配置合理性,避免因功率因数不足导致的线路损耗增加和电费惩罚。
4. 负载率匹配性检测
通过电流-负载率关联分析法,验证电动机实际负载是否处于经济区间(60%-80%)。对于长期轻载(<40%)或过载(>100%)的工况,需提出更换容量适配电机或加装变频调速装置的建议。
5. 温升与绝缘性能测试
采用红外热像仪监测定子绕组、轴承等关键部位温升,结合兆欧表测量绝缘电阻值(应≥1MΩ)。若温升超过GB/T 755规定的限值(B级绝缘≤80K),或绝缘电阻异常下降,需立即停机排查故障。
检测流程与优化策略
检测应遵循“数据采集-模型分析-能效诊断-方案制定”的闭环流程。建议每季度开展一次常规检测,并结合SCADA系统实现实时监测。对于检测发现的问题,可采取调整传动系统、优化控制策略、更换高效电机或加装智能节电器等解决方案,使综合节电率达到15%-25%。
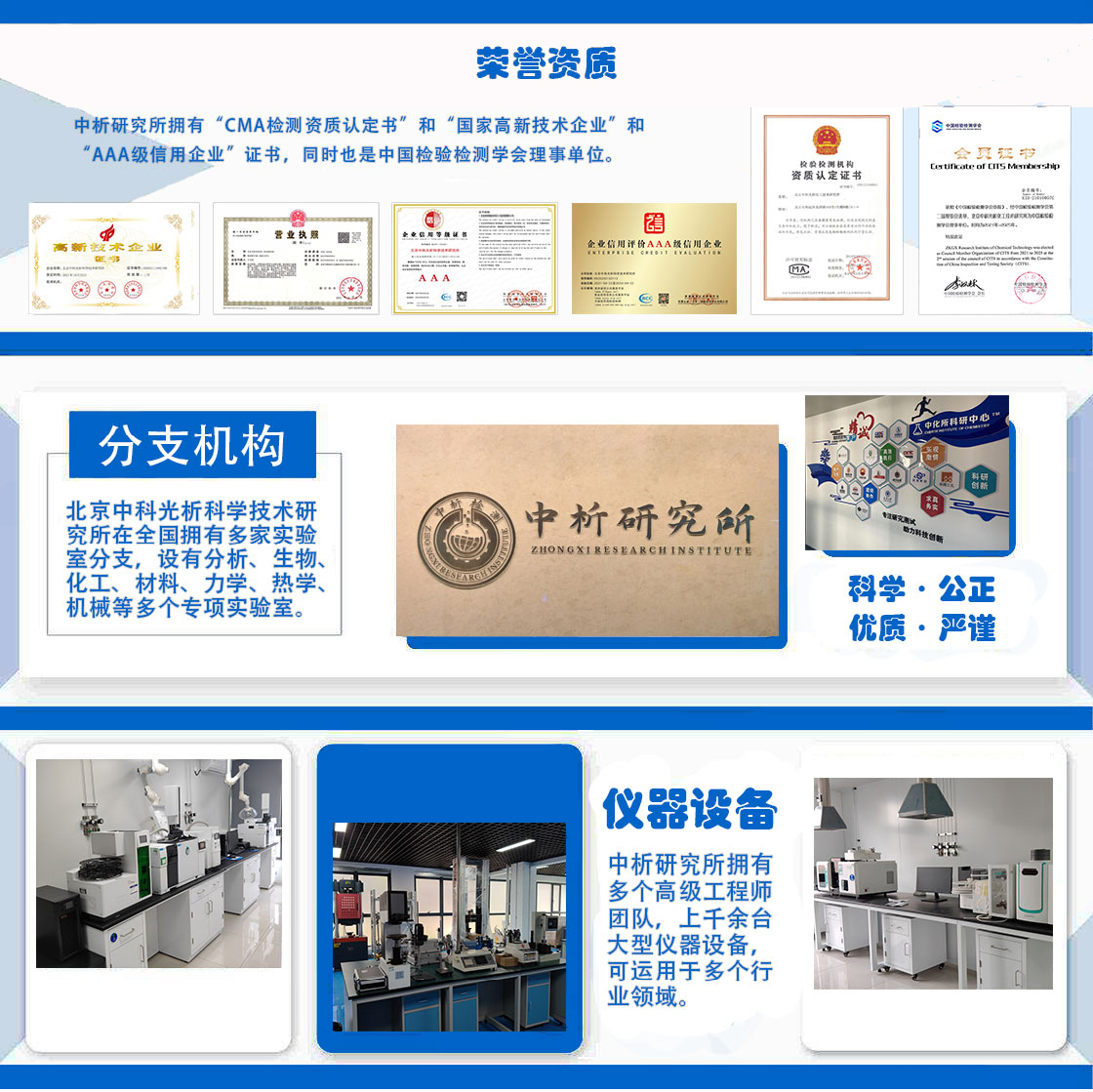
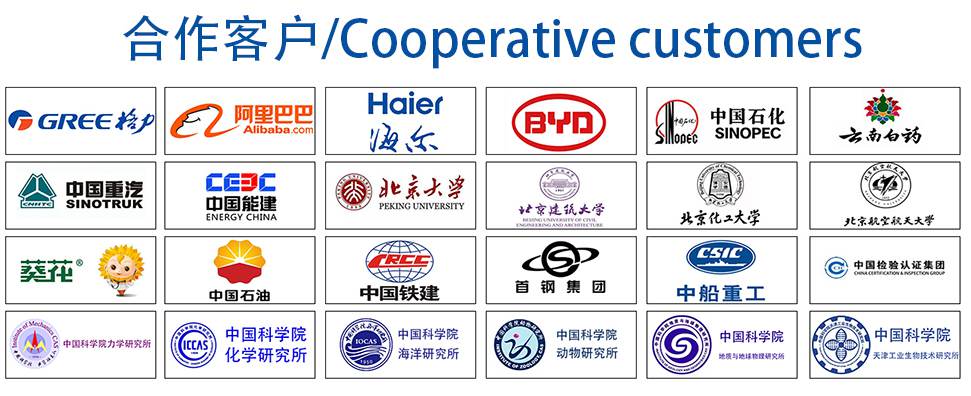