压力试验检测的重要性及应用领域
压力试验检测是评估设备和容器在高压环境下安全性与可靠性的核心手段,广泛应用于工业制造、能源化工、航空航天、建筑工程等领域。通过模拟实际工况下的压力条件,检测设备或材料的强度、密封性及抗变形能力,能够有效预防因压力异常导致的泄漏、爆炸等安全事故。尤其在压力容器、管道系统、锅炉、燃气设备等关键设施的验收及定期检验中,压力试验检测是确保其合规性和使用寿命的必要环节。此外,该检测还能为产品设计优化、材料选型提供数据支持,降低后期维护成本。
压力试验检测的主要项目
压力试验检测通常包含以下几类核心项目:
1. 静压试验
通过向被测对象施加恒定压力(通常为设计压力的1.25-1.5倍),在规定时间内观察其是否发生泄漏、变形或破裂。此项目主要用于验证设备的极限承载能力和结构完整性。
2. 耐压强度试验
通过逐步增加压力至规定值,检测材料在高压下的抗拉强度、屈服强度等力学性能,确保其在极端工况下的稳定性。
3. 气密性试验
采用气体(如氮气或压缩空气)作为介质,通过压力变化检测设备是否存在微小泄漏。常用方法包括气泡法、压力降法和氦质谱检漏法,适用于对密封性要求较高的设备。
4. 爆破试验
持续加压直至被测对象失效,记录爆破压力值以评估产品的安全裕度和设计合理性,常见于管材、阀门等部件的质量控制。
5. 疲劳压力试验
模拟设备在交变压力下的长期使用状态,检测其抗疲劳性能,适用于航空液压系统、核电站管道等需高频压力循环的场合。
压力试验检测的技术要点
为确保检测结果的准确性,需遵循以下技术规范:
- 介质选择:根据设备类型选择液体(水、油)或气体作为试验介质,液体介质需考虑粘度与挥发性,气体介质需严格防爆。
- 压力控制:采用高精度压力传感器和自动控制系统,确保加压速率和保压时间符合标准(如GB/T 150、ASME BPVC)。
- 安全防护:设置安全阀、防爆墙及远程监控系统,防范试验过程中可能发生的突发风险。
- 数据分析:结合应变仪、超声波测厚仪等设备,实时记录变形量、泄漏率等参数,生成检测报告并评估设备状态。
压力试验检测的行业标准与认证
国内外针对压力试验检测制定了多项强制性标准,例如中国的《固定式压力容器安全技术监察规程》(TSG 21)、欧盟的PED指令(2014/68/EU)以及美国的ASME Section VIII。检测机构需通过ISO/IEC 17025认证,确保检测流程与数据的权威性。企业需根据产品用途和出口目标市场,选择符合要求的检测标准与认证体系。
结语
压力试验检测不仅是保障设备安全运行的“生命线”,更是推动工业技术升级的重要支撑。通过科学规划检测项目、严格遵循技术规范,能够显著提升产品质量,降低安全事故发生率,为企业的可持续发展奠定基础。
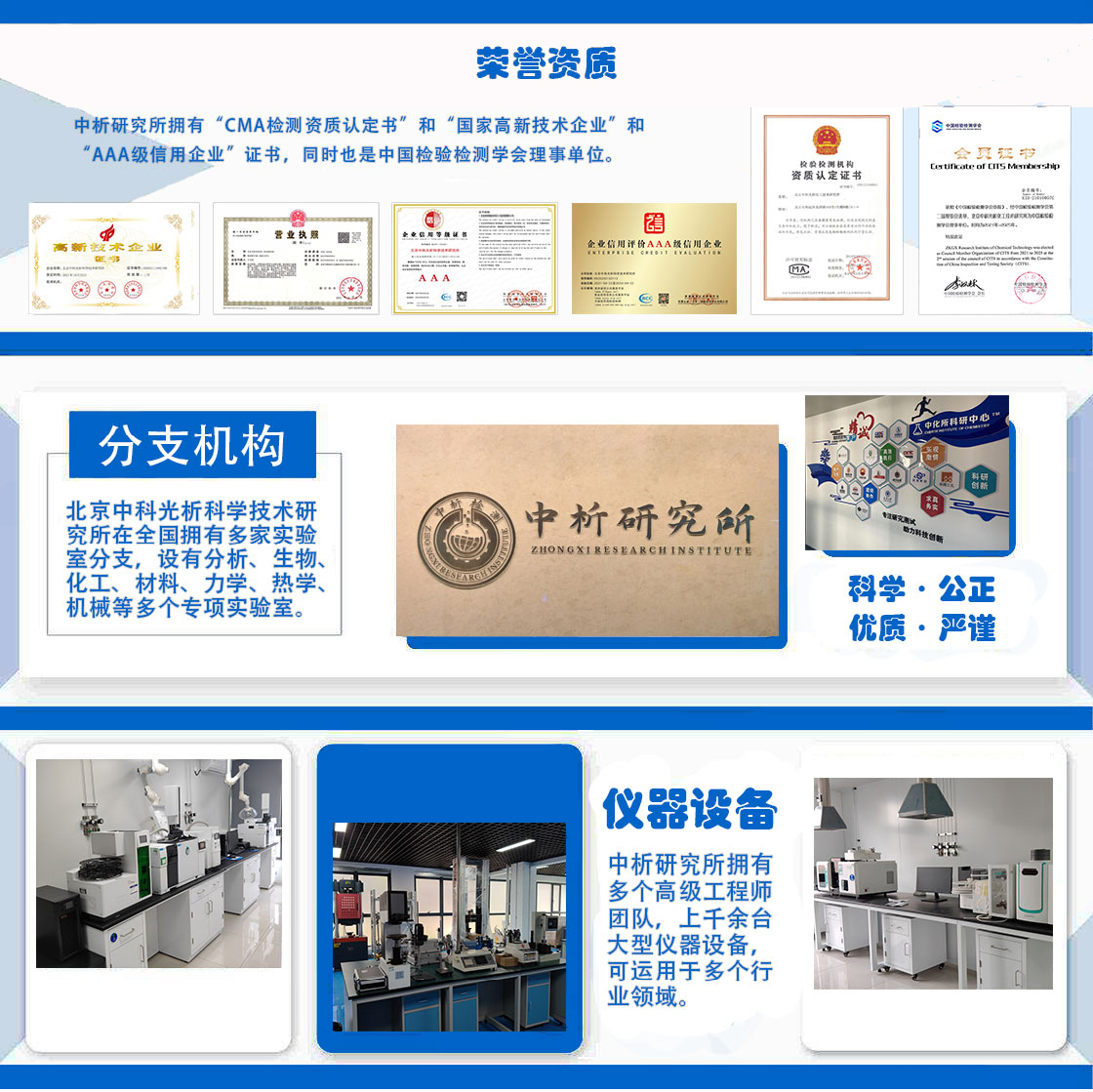
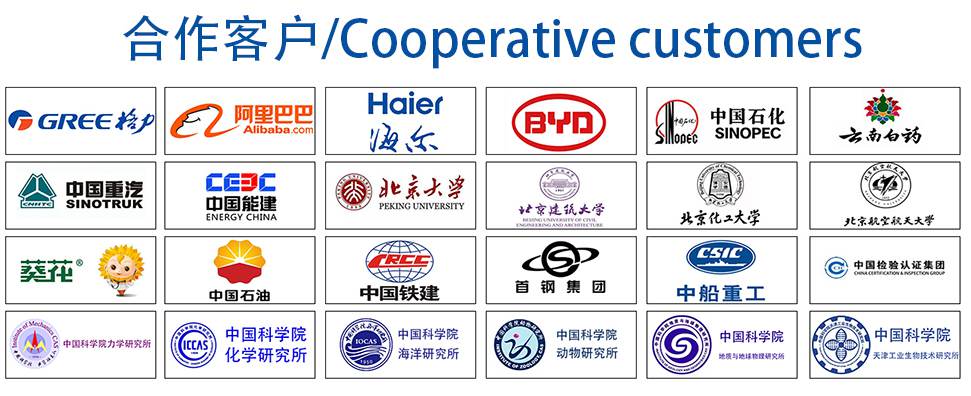