焊接接头和焊接试样检测的重要性
焊接是工业生产中广泛应用的基础工艺,其质量直接影响设备、结构的强度、密封性和使用寿命。焊接接头作为焊接结构的核心区域,易因工艺参数偏差、材料缺陷或操作不当产生裂纹、气孔、未熔合等问题。焊接试样检测则是通过模拟实际焊接条件,对材料性能、工艺参数及焊接质量进行验证的重要手段。通过科学的检测项目,能够全面评估焊接接头和试样的可靠性,确保其满足设计标准和安全需求。
焊接接头的主要检测项目
焊接接头的检测通常分为无损检测和破坏性检测两类:
1. 无损检测(NDT)
• 射线检测(RT):利用X射线或γ射线穿透焊缝,通过底片或数字成像发现内部气孔、夹渣、裂纹等缺陷(如ISO 17636标准);
• 超声波检测(UT):通过高频声波反射信号定位缺陷位置和深度(符合GB/T 11345要求);
• 磁粉检测(MT):适用于铁磁性材料表面及近表面裂纹检测(按JB/T 6061执行);
• 渗透检测(PT):通过显像剂显示开口缺陷,用于非多孔材料表面检查(依据ISO 3452)。
2. 破坏性检测
• 拉伸试验:测定焊接接头的抗拉强度、屈服强度和延伸率(按GB/T 2651标准);
• 弯曲试验:评估焊缝韧性及结合面质量,包括面弯、背弯和侧弯(参考GB/T 2653);
• 冲击试验:测试焊接接头在低温或动态载荷下的抗冲击性能(依据GB/T 2650);
• 硬度测试:检测热影响区与母材的硬度分布,分析组织变化(使用维氏或布氏硬度计)。
焊接试样的专项检测内容
焊接试样需针对特定用途设计检测方案:
1. 宏观组织分析
通过金相显微镜观察焊缝横截面的熔深、熔宽及热影响区宽度,检查未焊透、夹渣等宏观缺陷(按GB/T 3375进行)。
2. 微观金相分析
分析焊缝金属的晶粒度、相组成及显微缺陷(如微裂纹),评估焊接工艺对材料组织的影响(遵循ISO 9015标准)。
3. 化学成分检测
通过光谱分析仪或化学滴定法测定焊缝金属的元素含量,确保其符合母材匹配要求(参考AWS A5.01规范)。
4. 腐蚀性能试验
针对特殊环境应用(如化工设备),需进行盐雾试验、晶间腐蚀试验等以验证耐蚀性(按ASTM G48执行)。
检测结果的应用与改进
检测数据需与设计规范(如ASME BPVC、EN 287)对比,对于不合格项应分析原因并优化焊接工艺参数,包括电流电压调整、焊材选择或预热温度控制。通过系统化的检测流程,可显著提升焊接结构的安全性和经济性。
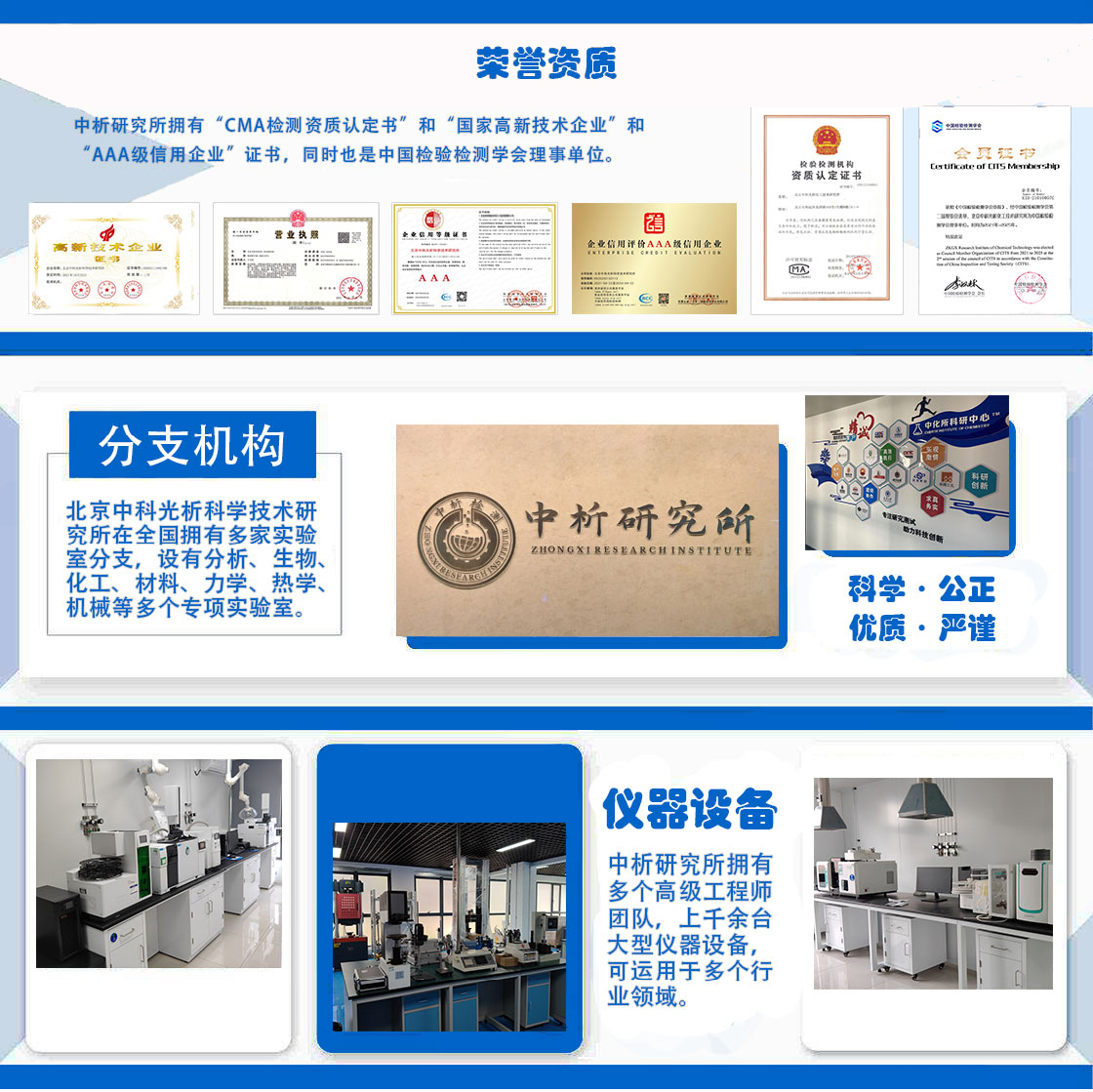
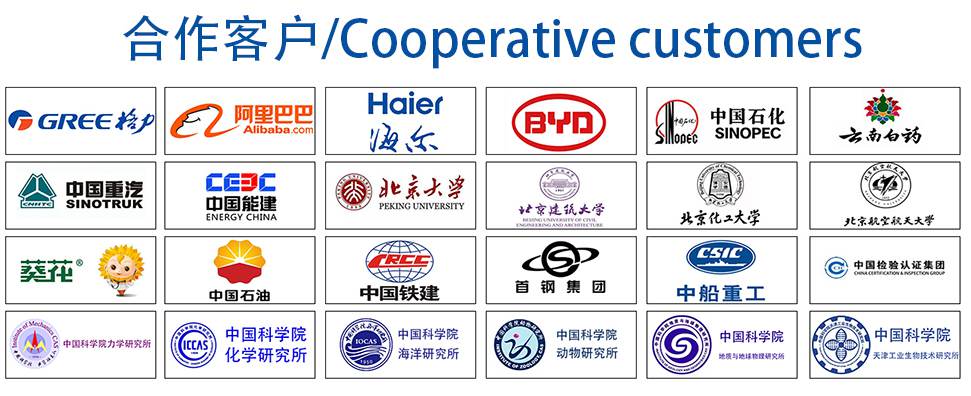