辊式颗粒破碎机检测的必要性与核心内容
辊式颗粒破碎机作为矿山、建材、化工等行业的核心破碎设备,其运行状态直接影响生产效率和产品质量。由于长期承受高负荷冲击及物料摩擦,设备关键部件易出现磨损、变形、裂纹等问题。定期开展系统性检测不仅能预防突发故障、延长设备寿命,还可通过数据积累优化生产工艺。检测过程需结合设备结构特点,针对传动系统、辊轮组件、密封装置等核心部位进行多维度技术评估,同时关注能耗与安全防护性能的匹配度。
辊式颗粒破碎机核心检测项目
1. 辊轮组件状态检测
作为直接参与破碎作业的核心部件,需重点检测辊面磨损量(使用激光测厚仪)、辊齿完整度(目视+探伤检测)及同轴度偏差(千分表测量)。当单侧磨损超过3mm或齿形缺损率达15%时需及时修复,同轴度偏差应控制在0.05mm/m范围内。
2. 传动系统运行检测
包含减速机振动值(测振仪检测,需≤4.5mm/s)、联轴器对中精度(激光对中仪测量,偏差≤0.1mm)、齿轮啮合间隙(塞尺测量,标准0.2-0.3mm)及轴承温升(红外测温,温升≤35℃)四大指标。需特别注意齿轮箱油液金属颗粒含量(光谱分析,Fe含量≤100ppm)。
3. 液压调隙系统检测
通过压力测试验证液压缸保压能力(30分钟压降≤5%),检查位移传感器精度(误差≤±0.2mm)。同步检测液压油清洁度(NAS 7级标准)和电磁阀响应时间(≤0.5s),确保辊间距动态调节的可靠性。
4. 防护装置与安全联锁
验证急停按钮响应时间(≤0.5s)、防护罩机械联锁有效性(断开后1s内停机),检测过载保护装置的电流阈值设定(应≤额定电流110%)。需模拟堵料工况测试自动反转功能(触发后3s内执行反转)。
5. 能耗与破碎效率评估
通过电能质量分析仪记录单位产量电耗(kW·h/t),比对设计指标偏差。同步进行粒度分析(筛分法+激光粒度仪),统计合格率(目标≥95%)。破碎比(进/出料粒径比)应维持在3.5-5.0区间。
检测周期与数据应用
建议每600运行小时进行常规检测,大修周期不超过8000小时。所有检测数据应纳入设备健康管理系统,建立趋势分析模型。通过比对历史数据可预判轴承寿命(振动值增幅>20%时预警)、预测辊面堆焊周期(磨损率>0.1mm/100h需计划维护),实现从被动维修向预测性维护的转型。
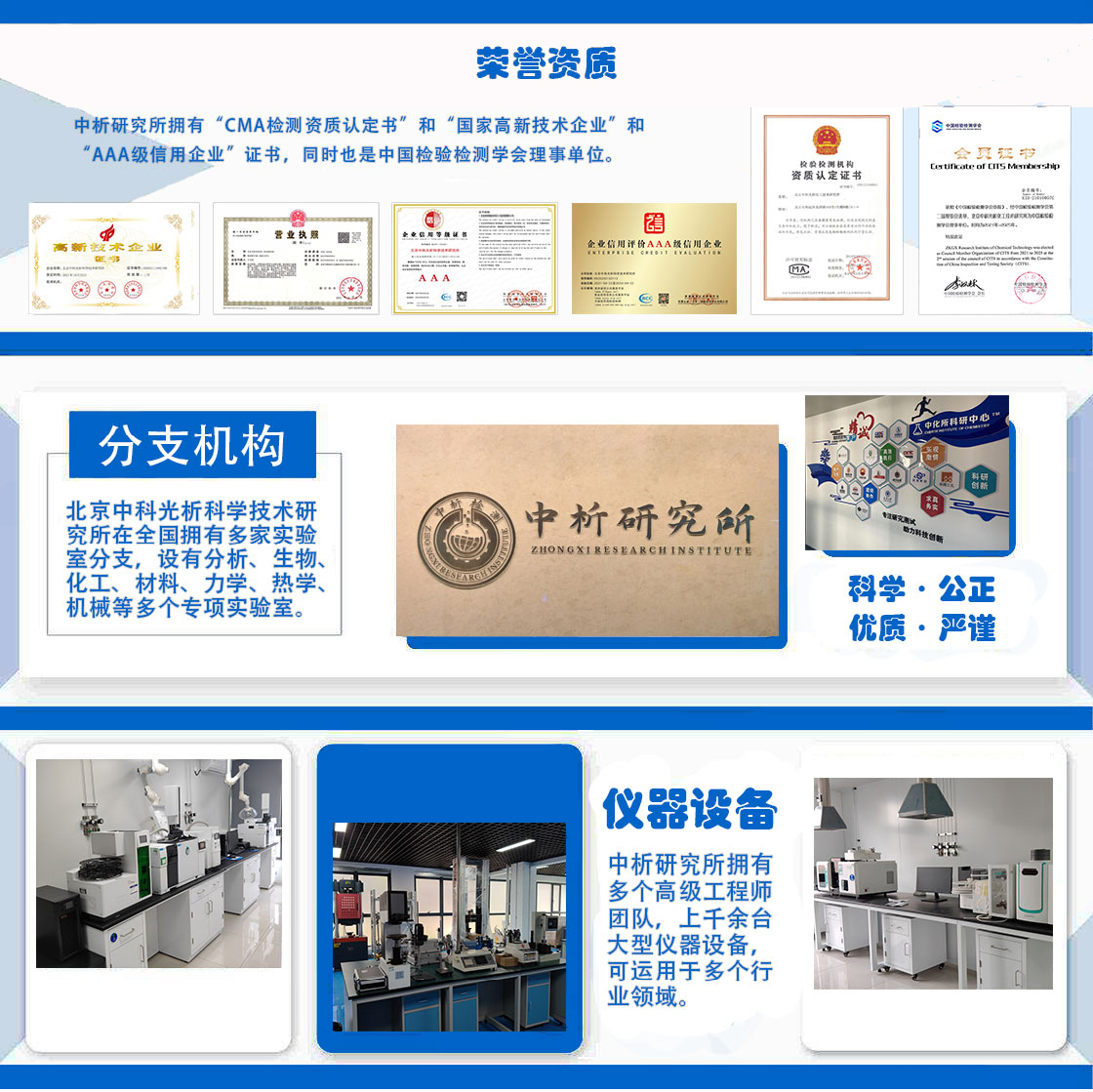
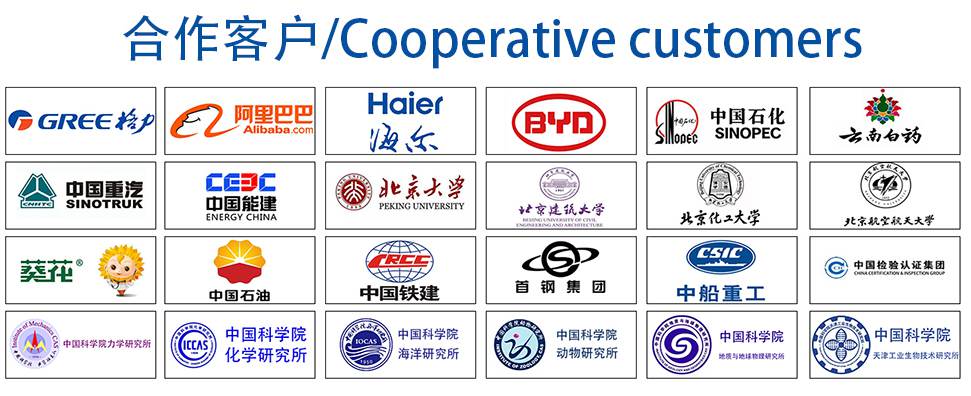