结晶罐作为化工、制药、食品等行业中广泛应用的结晶工艺核心设备,其运行状态直接关系到产品质量和生产效率。由于长期处于高温、高压、强腐蚀性介质等极端工况下,结晶罐的金属结构易出现疲劳损伤、应力腐蚀、壁厚减薄等问题。定期开展系统化检测评估,既是保障安全生产的法定要求,也是延长设备使用寿命、优化生产工艺的重要手段。
一、结晶罐检测核心项目
完整的结晶罐检测体系包含四大维度:
1. 结构完整性检测
采用超声波测厚仪对筒体、封头进行100%网格化测厚,绘制壁厚分布云图。重点检测焊缝区域:使用X射线探伤检测未熔合、气孔等缺陷;磁粉探伤排查表面裂纹;对椭圆度超标部位进行圆度矫正。2019年某制药企业案例显示,通过相控阵超声检测发现接管角焊缝处2.8mm深埋裂纹,及时避免了介质泄漏事故。
2. 材料性能检测
取样进行化学成分光谱分析,验证316L不锈钢的Mo含量是否≥2.5%;开展显微金相检验,确认奥氏体晶粒度等级;通过电化学工作站测试点蚀电位,评估材料耐蚀性。某氯碱企业检测发现,使用5年的结晶罐母材Cr含量下降0.6%,及时更换了受Cl-腐蚀严重的下封头。
3. 工艺参数检测
采用热电偶矩阵监测结晶过程温度场分布,优化降温梯度控制;使用光纤压力传感器实时监控工作压力波动;通过PH在线监测系统追踪介质酸碱度变化。某葡萄糖生产线的检测数据显示,将结晶区温差控制在±0.5℃后,晶体粒径均匀度提升37%。
4. 辅助系统检测
对搅拌系统进行动平衡测试,确保轴系振动值<4.5mm/s;使用激光对中仪校正机械密封的同轴度;采用氦质谱检漏法验证真空系统密封性。某钛白粉生产企业通过优化搅拌桨型,使结晶速率提高22%,能耗降低15%。
二、检测标准与周期
执行NB/T47013-2015承压设备无损检测标准,参照TSG21-2016固定式压力容器安全技术监察规程。常规检测周期为:年度外部检查、3年停机检验、6年全面检验,腐蚀速率>0.3mm/年的设备需缩短至2年全面检测。2023年新实施的GB/T40327-2022首次明确了结晶罐专用检测规范。
通过构建涵盖机械性能、化学特性、工艺参数的多维度检测体系,结合大数据分析建立设备健康档案,可有效预防结晶罐的突发性故障,实现从被动维修向预测性维护的转变,为流程工业的安全生产提供可靠保障。
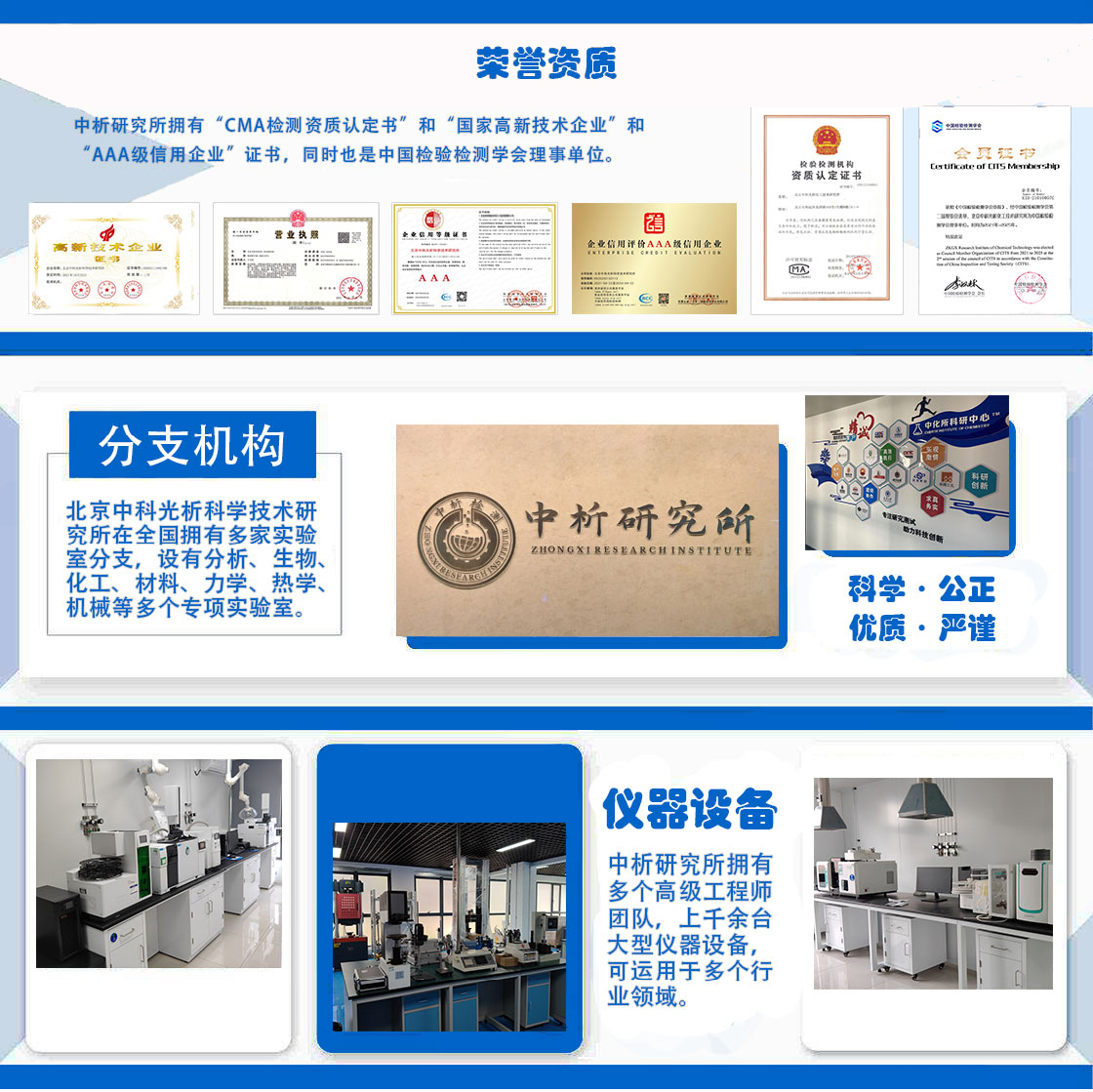
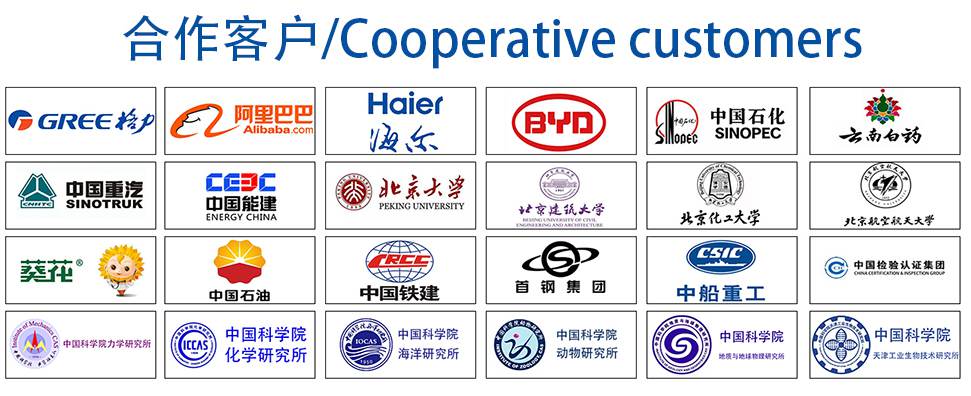