塑瓶液态乳制品灌装生产线检测体系解析
在液态乳制品工业化生产中,塑瓶灌装生产线作为核心环节,其运行精度与质量控制直接决定了产品安全性、保质期及市场合规性。随着GB 5413系列食品安全国家标准的实施和消费者对乳制品品质要求的提升,灌装生产线检测已从传统的机械参数监控发展为涵盖物理指标、微生物控制、包装完整性的多维度检测体系。该体系需满足每小时数千瓶高速灌装下的实时监测需求,同时符合HACCP关键控制点管理规范,确保从原料乳到成品包装的全链路可追溯性。
核心检测项目分类与实施标准
1. 密封性检测系统
采用负压测试与视觉检测双模式,通过压力衰减法检测瓶盖扭矩值(标准范围0.8-1.2N·m),配合高分辨率工业相机(最小分辨率0.02mm)识别瓶口密封圈完整性,泄漏率需控制在≤0.01%的行业基准。周期性校准需依据JJF 1070定量包装商品净含量计量检验规则执行。
2. 容量精度控制模块
配置在线质量流量计(精度±0.5%)与动态称重系统(分辨率0.1g),实时校核200ml/500ml等规格产品的灌装净含量。根据GB 5009.5要求,批次产品平均净含量不得低于标称值,单瓶负偏差≤3%。系统需具备每15分钟自动取样复检功能,异常数据触发声光报警并记录追溯编码。
3. 异物检测与微生物防控
集成X射线检测仪(检测灵敏度Φ0.3mm金属/Φ0.8mm玻璃)与高速CCD视觉系统(200fps拍摄速率),双通道剔除含异物产品。洁净灌装区需维持ISO 14644-1规定的5级洁净度,在线粒子计数器(0.5μm粒径)每2小时自动采样,菌落总数需≤10CFU/m³(GB 4789.2标准)。
4. 包装完整性验证体系
包含瓶体强度测试(爆破压力≥0.35MPa)、跌落测试(1.2m自由跌落无破损)及透氧率检测(≤0.5cm³/m²·24h·atm)。采用红外光谱法检测瓶坯PET材质结晶度(标准值32-38%),防止因材料缺陷导致的保质期内变质风险。
智能化数据追溯平台
基于MES系统构建生产批次数据库,记录灌装温度(85±2℃)、时间参数(4-6秒)、设备状态等300+维度数据。通过OPC UA协议实现与实验室信息管理系统(LIMS)的实时交互,异常批次可在15分钟内完成质量溯源,符合FDA 21 CFR Part 11电子记录规范要求。
该检测体系通过动态优化控制算法,可使生产线OEE(设备综合效率)提升至85%以上,产品一次合格率稳定在99.97%以上,为液态乳制品生产企业构建起从过程控制到终端保障的全方位质量防线。
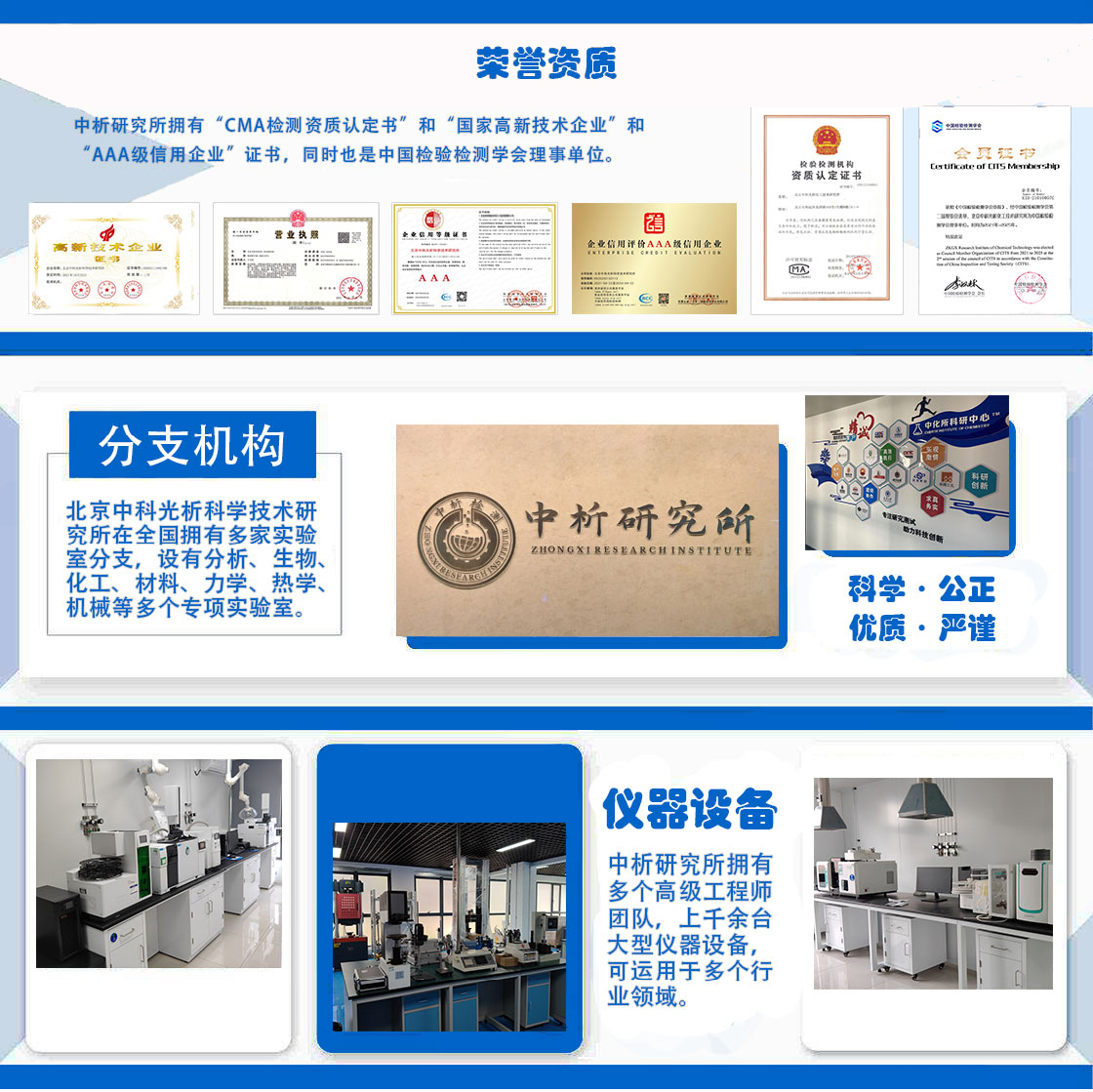
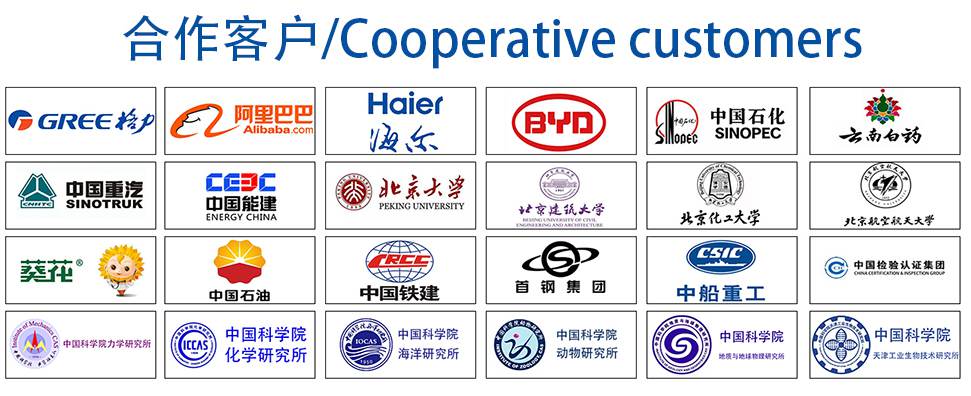