(防爆)超压排气活门检测的重要性与应用场景
防爆超压排气活门作为工业安全防护系统中的核心组件,广泛应用于化工、石油、电力、核设施及粉尘爆炸危险场所。其功能是在系统内部压力超出安全阈值时快速开启排气,防止设备或管道因超压引发爆炸事故。由于工作环境的特殊性和安全需求的严苛性,定期开展防爆超压排气活门的检测成为保障安全生产的必要措施。通过系统化的检测,可确保活门启闭灵敏度、密封性能及防爆等级符合设计要求,从而有效降低爆炸风险,延长设备使用寿命。
防爆超压排气活门检测项目清单
1. 密封性能检测
采用气密性试验装置对活门在关闭状态下的密封性进行测试,通过加压至额定工作压力的1.1倍并保压30分钟,观察压力表数值变化。泄漏率需≤3%方为合格,同时检查密封面磨损、腐蚀或变形情况,确保无介质渗漏风险。
2. 动作压力校准
使用专用压力校准设备验证活门的开启压力与复位压力值。根据GB/T 12241-2021标准,在模拟超压工况下,活门应在设计压力±5%范围内准确动作,复位后需完全闭合且无卡滞现象。需反复测试3次以上以确认稳定性。
3. 结构完整性检测
通过目视检查、超声波探伤及磁粉检测技术,评估阀体、弹簧、阀瓣等关键部件的机械性能。重点关注焊接部位裂纹、弹簧疲劳断裂及腐蚀减薄情况,阀体壁厚损失不得超过原厚度的10%。
4. 防爆性能验证
依据GB 3836.1-2021防爆电气设备标准,对活门的隔爆接合面间隙、表面粗糙度及耐压强度进行检测。通过爆炸压力测试验证其抗爆能力,要求活门在1.5倍最大爆炸压力下保持结构完整,且爆炸火焰不得外泄。
5. 耐腐蚀性评估
在化工等高腐蚀环境中,需对活门材料进行盐雾试验(按GB/T 10125标准)和介质浸泡试验。重点检测不锈钢部件晶间腐蚀倾向,非金属密封件的溶胀老化情况,确保材料耐受性满足工况要求。
检测流程与技术要求
专业检测应遵循"外观检查→解体清洗→尺寸测量→功能测试→防爆验证"的标准化流程,检测周期建议每12个月或设备大修时实施。检测机构需具备CMA认证资质,检测人员应持有特种设备检验员证书,检测数据需实时记录并生成可视化报告,为设备维护决策提供科学依据。
结语
防爆超压排气活门检测是工业安全体系的重要环节,通过系统化的检测项目组合,可全面评估设备的安全性能。企业应建立完善的检测档案管理制度,结合智能传感器技术实现预测性维护,从而最大限度避免因活门失效引发的安全生产事故。
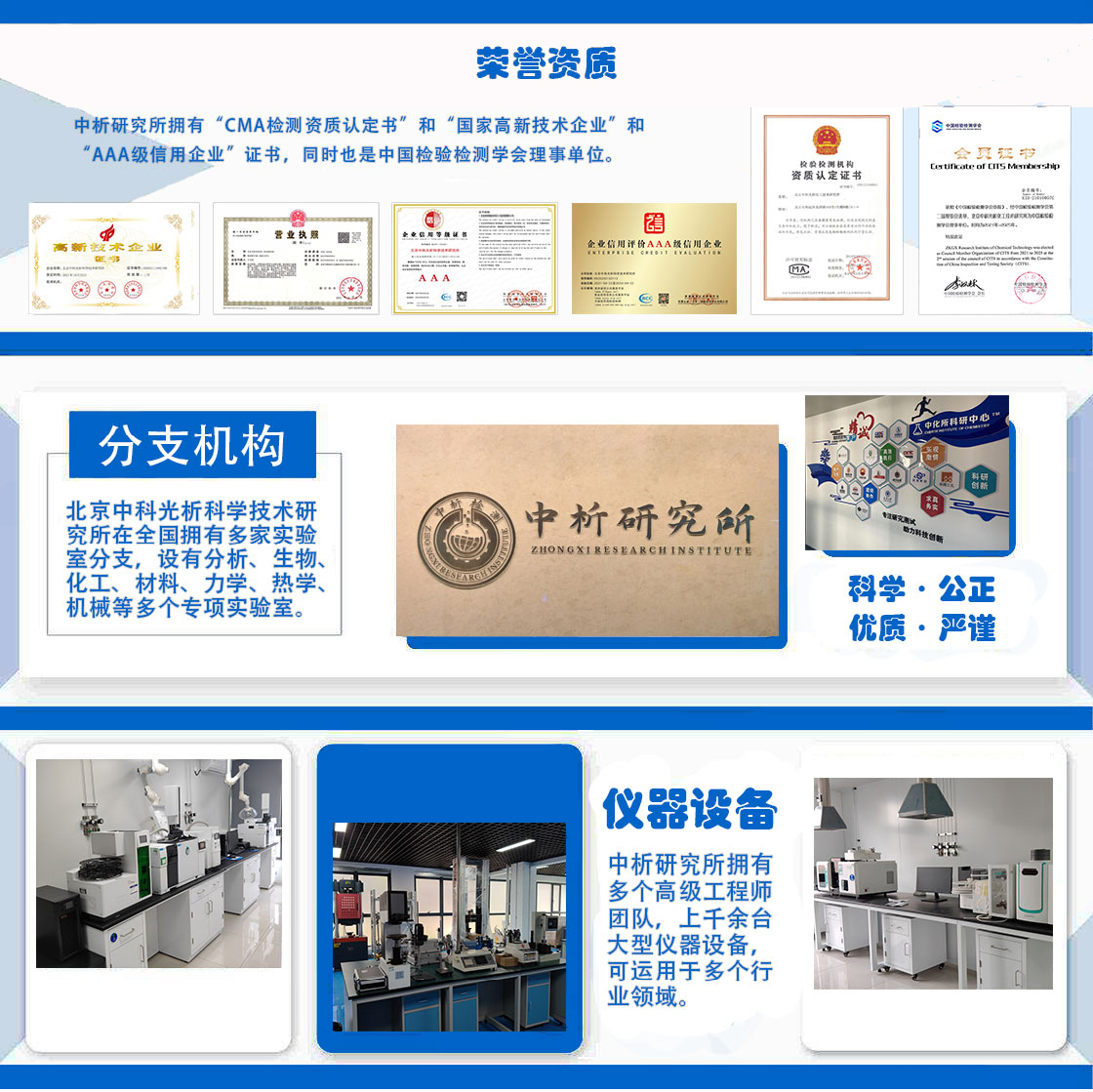
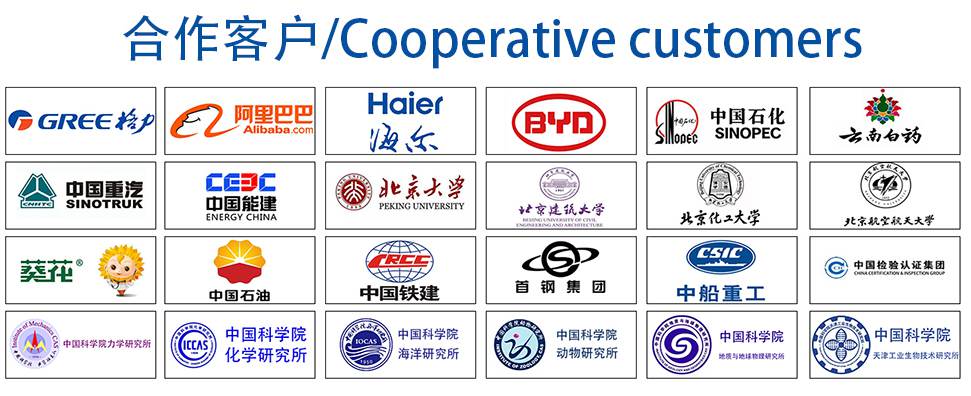