内燃机金属冷却风扇检测的重要性
内燃机金属冷却风扇是发动机热管理系统的核心组件之一,其性能直接影响发动机的散热效率、能耗水平和使用寿命。在高温、高转速和复杂工况下,金属冷却风扇需承受反复的机械应力与热冲击,任何结构缺陷或材料劣化都可能导致叶片变形、断裂甚至引发连锁故障。因此,通过系统化检测项目对风扇的材质特性、几何精度、动平衡性能及耐久性进行全面评估,成为保障内燃机可靠运行和预防突发性故障的关键环节。
核心检测项目清单
1. 材料成分与金相分析
采用光谱分析仪检测铝合金/不锈钢材料中的元素配比,验证是否符合GB/T 1173或ASTM标准要求。通过金相显微镜观察材料晶粒度、夹杂物分布及热处理效果,确保基体材料具备良好的抗疲劳特性。
2. 几何尺寸精度检测
使用三坐标测量机(CMM)对叶片安装孔径、轮毂端面跳动量、叶片扭角等关键尺寸进行三维扫描,公差范围需控制在±0.05mm以内。同步检查叶片径向/轴向轮廓度,确保气流动力学特性符合设计规范。
3. 动平衡性能测试
在动平衡机上以1500-6000rpm模拟实际工况,测量残余不平衡量。根据ISO 1940标准要求,平衡等级应达到G6.3级,振动幅值不超过2.5mm/s。对超标产品需进行配重修正或判定报废。
4. 高频疲劳强度试验
通过电磁振动台施加10^7次循环载荷,模拟发动机全生命周期内的交变应力。检测叶片根部应力集中区是否出现裂纹萌生,验证结构设计的安全系数是否达到3倍以上行业标准。
5. 盐雾腐蚀耐受性验证
依据GB/T 10125标准进行96小时中性盐雾试验,评估阳极氧化层或电镀层的耐腐蚀性能。试验后表面不应出现基体腐蚀,涂层脱落面积需小于总表面积的0.5%。
6. 热变形温度特性测试
将试样置于温度循环箱中,在-40℃至200℃范围内进行50次冷热冲击试验,检测叶片尖端变形量。允许的最大形变量应小于0.1mm,且不得出现永久性塑性变形。
智能检测技术应用
随着工业4.0技术的普及,基于机器视觉的自动光学检测(AOI)系统已实现叶片表面缺陷的毫秒级识别,X射线断层扫描可非破坏性检测内部孔隙率。数字孪生技术通过建立风扇三维模型,能预测不同工况下的应力分布,显著提升检测效率和准确性。
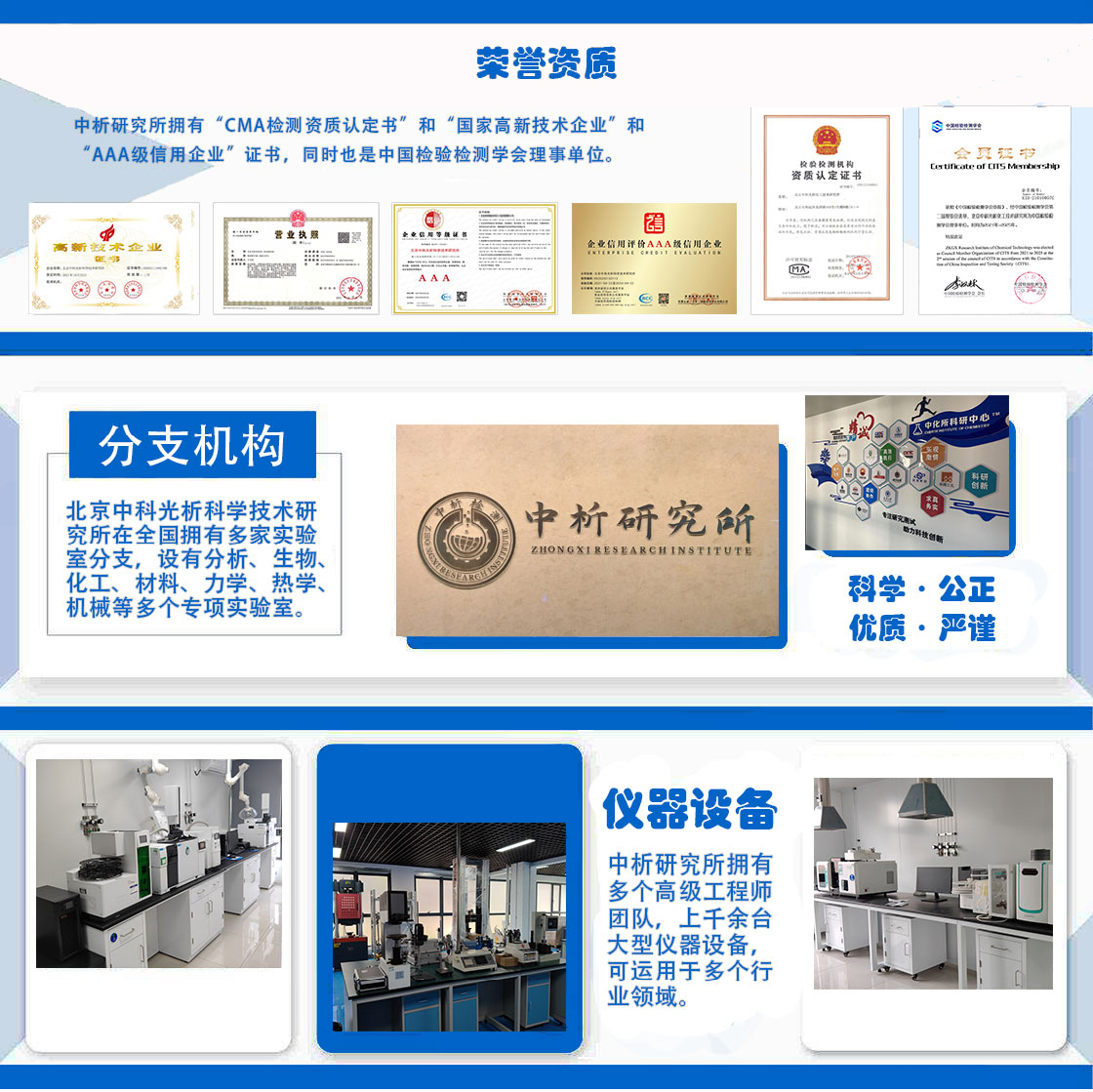
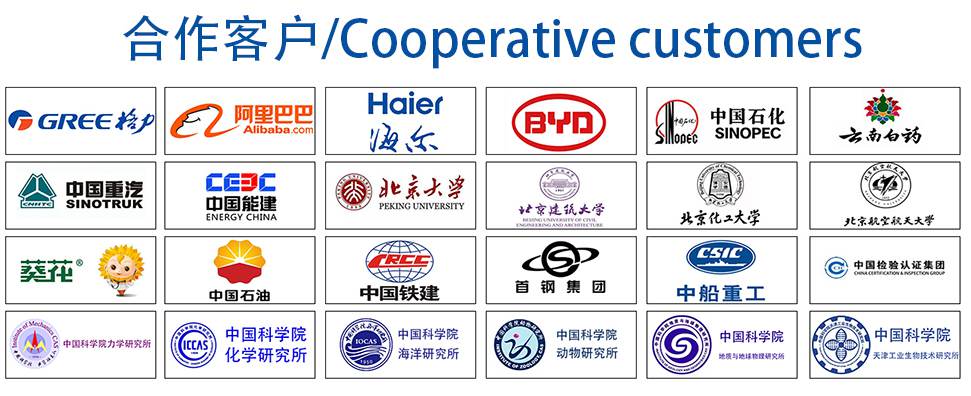