电工异形铜排及铜合金排凹行排检测的重要性
在电力设备制造及输配电系统中,异形铜排及铜合金排因其优异的导电性、机械强度和耐腐蚀性,被广泛应用于变压器、开关柜、母线槽等关键部件中。其中,凹行排(即具有特定凹陷结构的铜排)的几何精度、表面质量和材料性能直接影响设备的导电效率、散热能力及长期运行稳定性。然而,由于加工工艺复杂、使用环境严苛,此类铜排易出现尺寸偏差、表面缺陷或材料性能退化等问题,可能引发局部过热、接触电阻增大甚至设备故障。因此,针对异形铜排及铜合金排凹行排的专项检测成为保障电力系统安全运行的重要环节。
核心检测项目及方法
1. 几何尺寸与形状精度检测
使用三坐标测量仪(CMM)或激光扫描仪对凹行排的截面尺寸、凹陷深度、角度公差及整体弯曲度进行高精度测量,确保其符合GB/T 5585.1-2018《电工用铜、铝及其合金母线》标准要求。重点检测关键部位的配合尺寸,避免因安装偏差导致接触不良。
2. 表面质量与缺陷分析
通过目视检查结合金相显微镜、工业内窥镜对表面裂纹、气孔、氧化层等缺陷进行定性定量分析。采用涡流探伤或超声波探伤技术检测内部夹杂、分层等隐蔽性缺陷,确保材料内部结构的完整性。
3. 导电性能测试
依据IEC 60468标准,使用四探针电阻率测试仪或微欧计测量铜排的电阻率,评估其导电效率。对于铜合金排需额外分析合金元素对导电性的影响,确保导电率不低于国标规定值(如纯铜排≥98% IACS)。
4. 力学性能评估
通过万能材料试验机进行抗拉强度、屈服强度和延伸率测试,验证材料在弯曲、冲压加工后的机械性能。对于凹行排的应力集中区域,需结合有限元分析(FEA)模拟验证其抗疲劳强度。
5. 耐腐蚀性检测
采用盐雾试验箱模拟湿热、盐雾等恶劣环境,参照GB/T 10125标准进行加速腐蚀试验。通过电化学工作站测定材料的极化曲线,评估其耐电化学腐蚀能力,特别关注铜合金排的钝化膜稳定性。
6. 焊接质量与金相组织分析
针对焊接连接的凹行排,利用X射线探伤检测焊缝内部缺陷,并通过金相显微镜观察焊缝及热影响区的晶粒形态,分析是否出现晶界腐蚀或粗化现象,确保焊接接头的力学与电气性能一致性。
7. 成分与杂质含量检测
采用直读光谱仪(OES)或X射线荧光光谱仪(XRF)分析铜及合金元素的含量,检测铅、硫等杂质元素是否超标。对于高导电要求的铜排,需确保氧含量≤0.001%(无氧铜标准)。
检测结果的意义与改进方向
通过系统化检测,可精准识别凹行排在加工、运输或使用中的潜在风险点。例如,若发现局部电阻率异常升高,可能需优化退火工艺以消除残余应力;若表面缺陷频发,则应改进冲压模具的润滑方案。检测数据还可反馈至设计端,推动铜排结构优化与材料选型升级,最终实现电力设备的高效化与长寿命化。
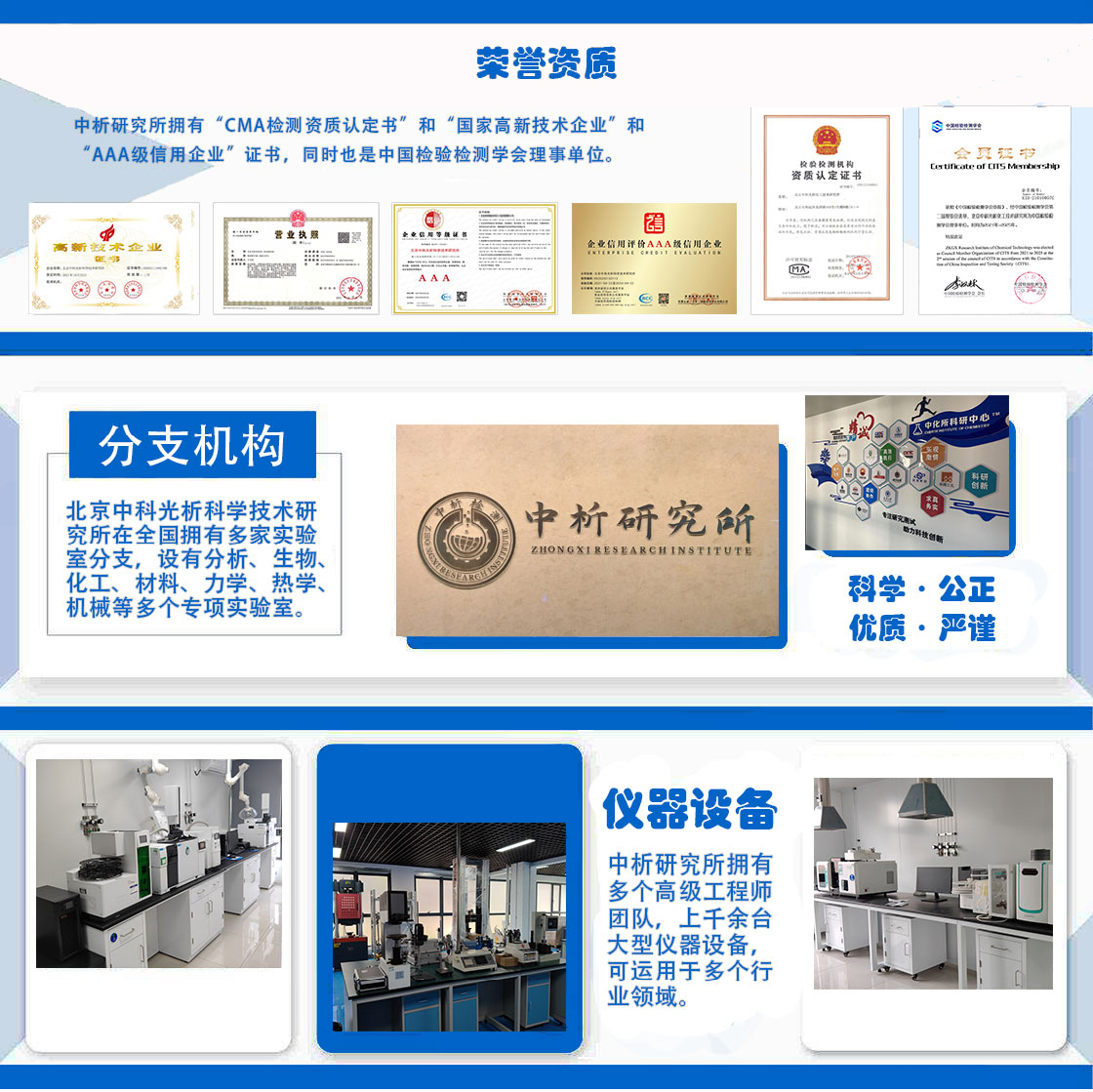
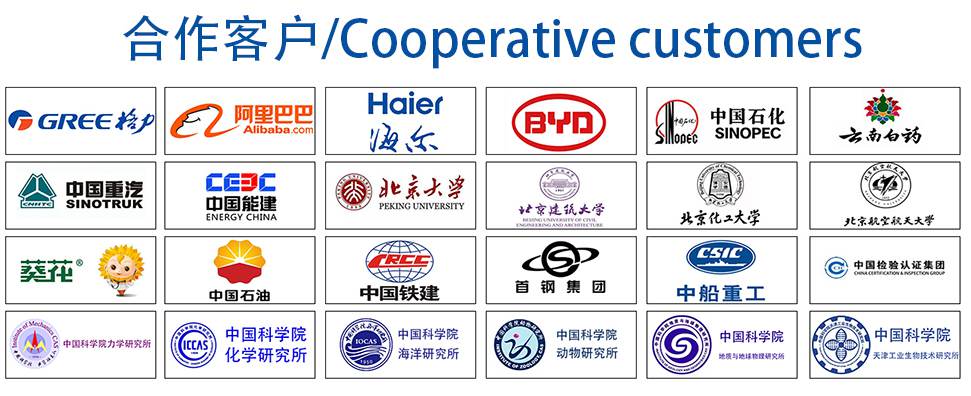