拖拉机用转速工作小时表检测的重要性
在农业机械管理中,拖拉机的工作小时表是衡量设备使用强度、制定维保计划的关键依据。传统机械式小时表通过累计发动机运转时间记录工作量,而现代拖拉机普遍采用基于转速信号的电子式工作小时表,其原理是通过监测发动机转速动态调整计时逻辑(如怠速状态按比例折算工作时间)。这种设计既能准确反映实际作业负荷,又能避免空转造成的虚增计时。然而,由于传感器故障、电路老化或系统设置错误,可能导致小时表数据偏差超过±10%,直接影响设备折旧核算、三包服务期限判断以及关键零部件的预防性更换周期。因此,定期开展转速工作小时表专项检测已成为农机技术服务机构的核心服务项目之一。
核心检测项目与实施方法
1. 转速信号采集系统检测
使用示波器连接转速传感器输出端,在发动机怠速(600-800rpm)、中速(1500rpm)和高速(2200rpm)工况下分别采集波形信号。重点检测信号幅值是否稳定在4.5-5.5V范围,频率波动是否小于±2%。对于霍尔式传感器需验证磁隙间隙(标准值0.8-1.2mm),磁阻式传感器应检查电阻值(常温下120-180Ω)。
2. 计时逻辑算法验证
通过诊断仪读取ECU内存储的计时程序,对比设备铭牌标注的计时标准:当转速≥800rpm时按1:1累计时间;500-800rpm区间按0.7系数折算;<500rpm不计入有效工时。使用发动机测功机模拟不同转速工况,持续运行30分钟后核对小时表增量是否在允许误差(±3分钟)范围内。
3. PTO关联计时功能测试
对于配备动力输出轴(PTO)的机型,需检测PTO启用状态下的计时补偿功能。在PTO转速540/1000rpm模式下,分别进行带载(≥75%额定扭矩)和空载测试,验证小时表是否会根据负载率自动调整计时系数(通常满载按1.2倍速累计)。
4. 数据存储与显示一致性校验
使用专用检测设备同时读取ECU原始数据、仪表盘显示值及远程监控平台记录。在连续8小时模拟作业中,每小时记录三组数据比对差异。要求各通道间最大偏差不超过0.1小时,历史数据存储完整率需达到100%。
5. 环境适应性检测
将设备置于高低温试验箱,在-20℃至65℃温度范围内进行冷热冲击测试。重点观察液晶屏在低温下的响应速度(应<2秒),以及高温环境下信号传输延迟(CAN总线报文间隔需保持100-200ms)。同时模拟85%湿度环境,检测接插件端子是否出现氧化导致的接触电阻升高(>0.5Ω即为异常)。
6. 故障自诊断功能验证
人为制造传感器断路、信号干扰等故障,检测系统能否在3秒内触发故障码(如P0500系列代码),并通过仪表盘警示图标提示。对于配备智能终端机型,还需测试无线报警信息能否在10秒内上传至云平台。
检测结果分析与处置建议
完成上述检测后,需编制包含原始数据记录、波形图谱和误差分析表的检测报告。当发现转速信号失真度>15%时,建议更换传感器并重新标定;若计时算法偏差超过5%,需通过厂家专用软件刷新控制程序;对于存在数据不同步现象的机型,应检查CAN总线终端电阻(标准值120Ω)和网关模块固件版本。经校正后的工作小时表,其综合误差应控制在±2%以内,确保为农机全生命周期管理提供可靠数据支撑。
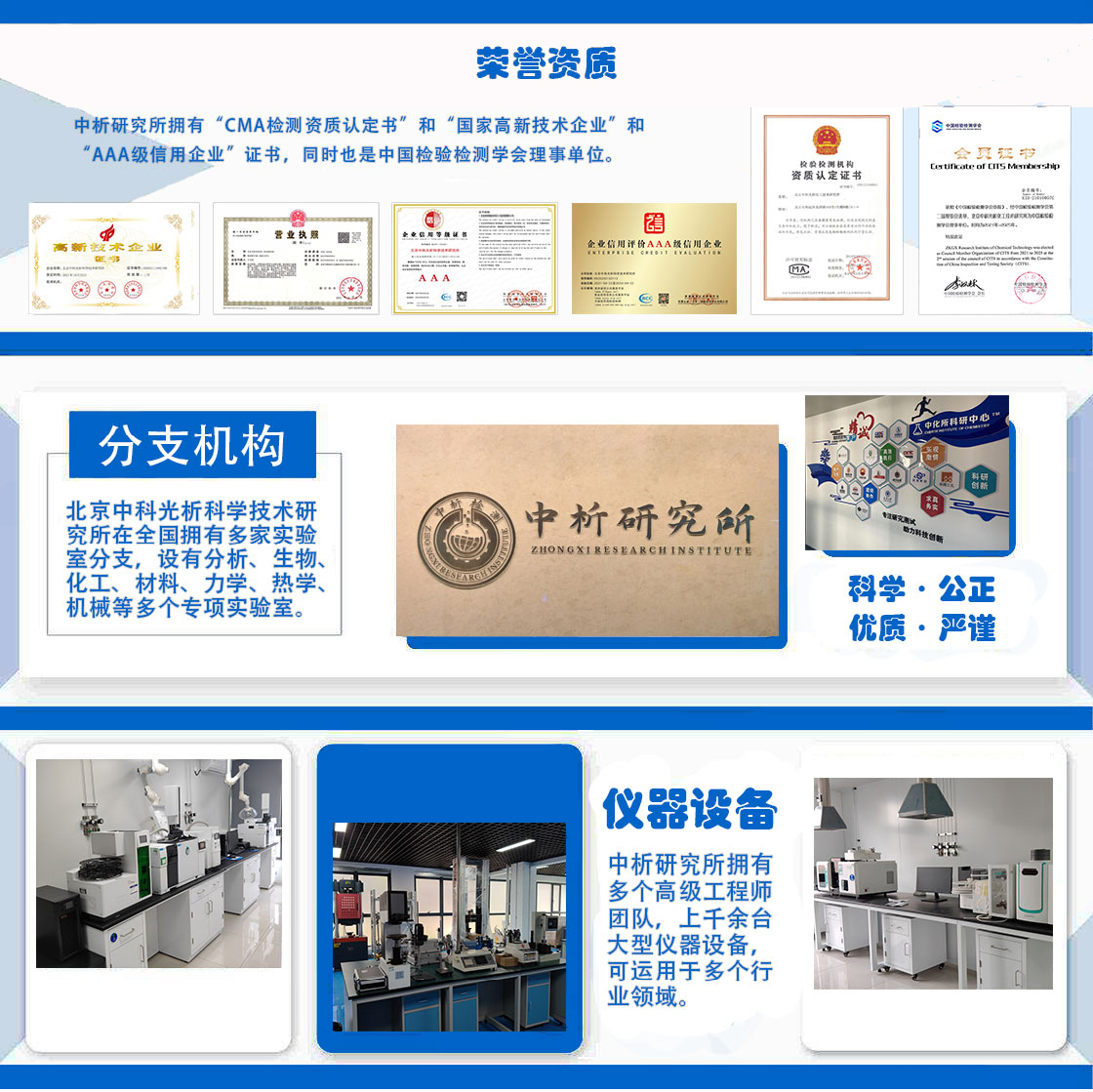
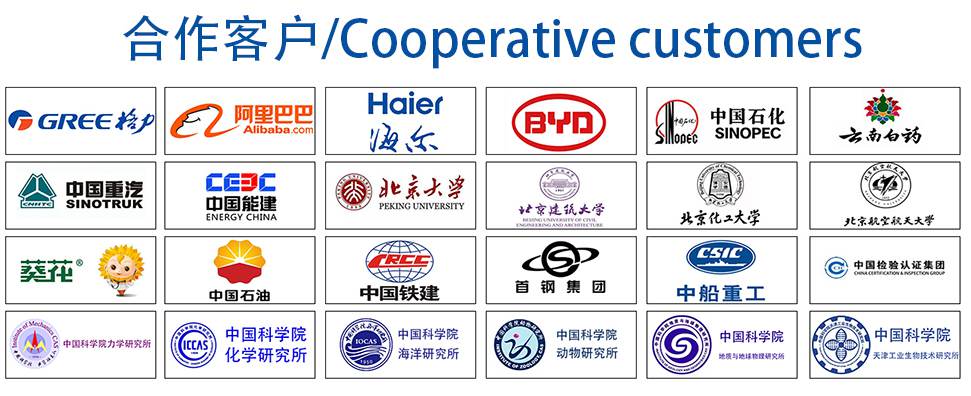