装配质量检测:保障产品性能的关键防线
在现代化制造业中,装配质量检测是确保产品功能、安全性和使用寿命的核心环节。随着工业4.0技术的发展,检测项目已从传统目视检查升级为包含数字化、智能化手段的复合型质量管控体系。通过系统化的检测流程,企业可精准识别装配过程中出现的零部件错位、配合偏差、紧固失效等问题,据行业统计,有效的装配检测可降低30%以上的产品返修率。尤其在汽车、航空航天、精密仪器等领域,装配质量的毫厘之差可能引发严重后果,因此检测项目必须涵盖从微观尺寸到宏观功能的完整维度。
核心检测项目解析
1. 尺寸与形位公差检测
采用三坐标测量机(CMM)或激光扫描仪对装配体的关键尺寸进行微米级测量,验证孔轴配合、平面度、同心度等参数是否符合设计要求。齐全系统可自动比对CAD模型数据,生成三维偏差色谱图。
2. 配合间隙与干涉检测
通过塞尺、间隙规或工业内窥镜检测运动部件间的实际间隙,同时运用有限元分析预测热膨胀带来的潜在干涉风险。汽车发动机装配中该项目的合格率直接决定整机NVH性能。
3. 连接强度测试
使用扭矩扳手校验螺栓预紧力,开展振动台试验评估连接结构耐久性。针对焊接/粘接工艺,需进行拉力剪切测试,航空航天领域要求焊缝强度达到母材的90%以上。
4. 功能性动态检测
在模拟工况下验证装配体整体性能,包括:
• 液压系统保压测试(泄漏量<0.1ml/min)
• 旋转机构动平衡检测(G2.5级标准)
• 电气接插件的导通阻抗测量(≤5mΩ)
5. 表面质量与缺陷识别
借助工业相机配合AI算法检测划痕、毛刺、污染等表面缺陷,使用超声波探伤仪探测内部气孔、裂纹。高端产线已实现每分钟2000帧的高速瑕疵捕捉能力。
6. 材料匹配性验证
通过光谱分析确保装配件材质符合BOM清单,重点防范异种金属接触引发的电化学腐蚀。新能源汽车电池包装配需额外检测绝缘材料的耐高温性能。
7. 智能化过程监控
基于IoT的装配线实时采集拧紧曲线、压装压力等300+过程参数,MES系统自动触发质量追溯。某变速箱工厂通过该技术将错装率从0.8%降至0.02%。
检测技术发展趋势
当前装配检测正朝着多传感融合方向发展,机器视觉、量子测量等新技术使检测精度突破纳米级。值得关注的是,数字孪生技术可实现虚拟装配与实物检测的闭环验证,某航天企业通过该方案将装配调试周期缩短了40%。随着AI深度学习的应用,未来检测系统将具备自主决策能力,真正实现零缺陷制造目标。
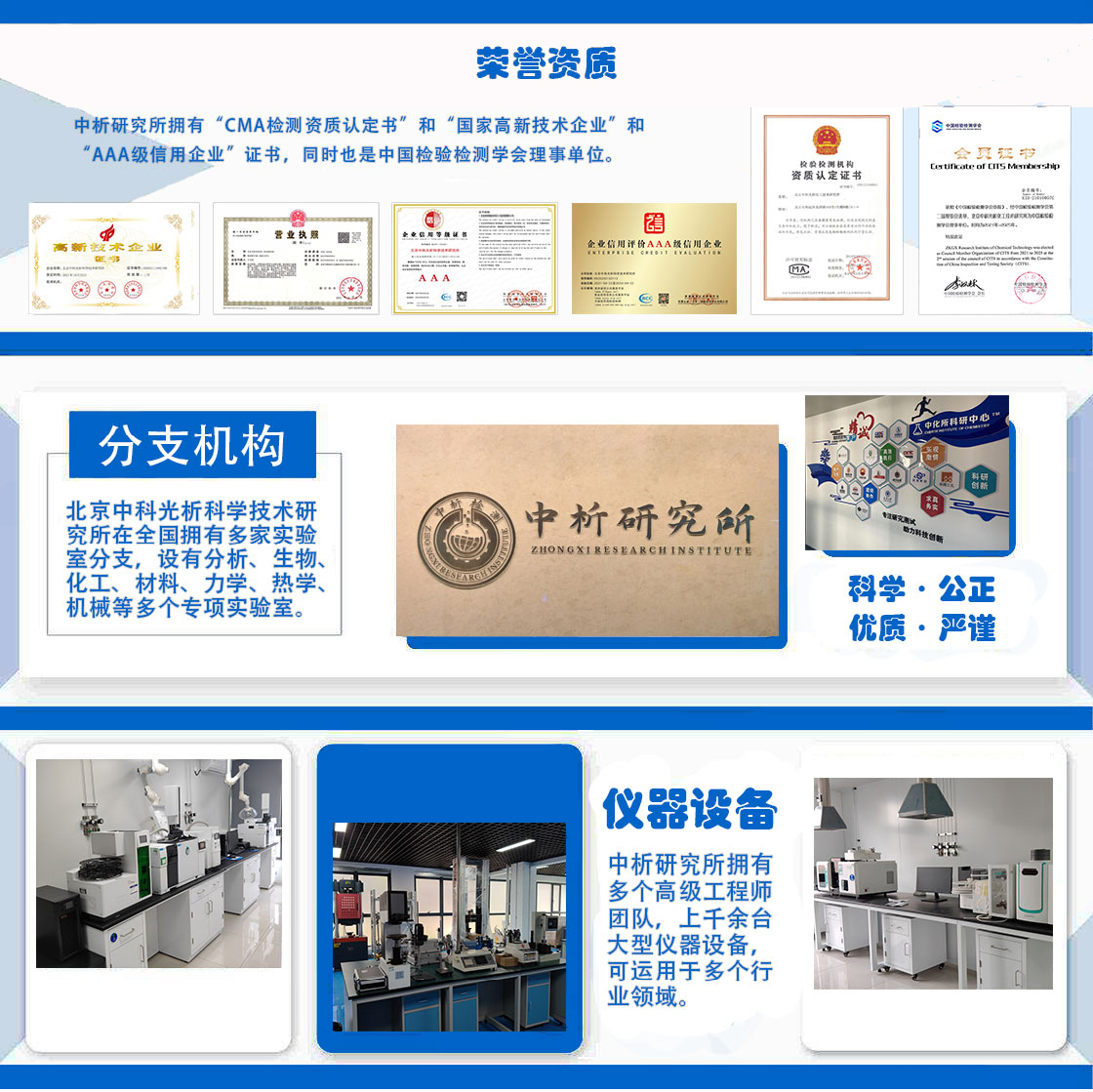
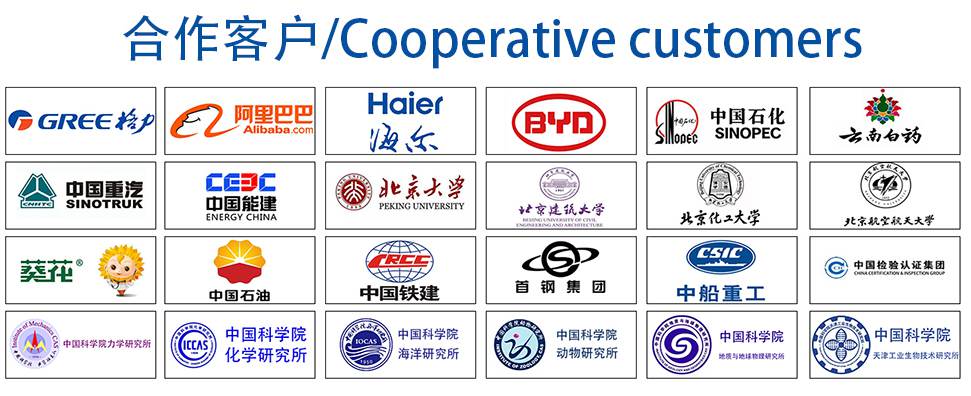