含气饮料灌装封盖机检测的重要性
随着饮料行业的快速发展,含气饮料(如碳酸饮料、气泡水等)的市场需求持续增长。作为生产链中的核心设备,灌装封盖机的性能直接关系到产品质量、生产效率及企业经济效益。由于含气饮料对灌装精度、密封性和气体保持能力的要求极高,定期对灌装封盖机进行系统性检测成为保障生产安全、避免产品缺陷的关键环节。通过科学的检测手段,企业不仅能优化设备运行状态,还能降低因设备故障引发的产品报废率,同时确保符合国家食品安全与卫生标准。
核心检测项目及技术要点
1. 密封性检测
密封性是含气饮料灌装封盖机的核心指标。检测时需模拟实际生产条件,通过负压测试或真空室检测仪验证瓶盖与瓶口的密封效果。重点检查封盖部位是否存在微小泄漏,确保二氧化碳等气体不会在储存或运输过程中逸散。常见检测方法包括压力衰减法和气泡法,要求泄漏率低于0.05%才符合标准。
2. 灌装精度检测
灌装量的精确控制直接影响产品计量合规性与成本控制。检测时需使用高精度称重传感器或流量计,验证设备在连续灌装过程中每瓶液位的一致性。标准误差范围通常控制在±1%以内,并需关注设备在不同速度下的稳定性。对于含气饮料,还需确保灌装过程中气泡分布均匀,避免因液位波动导致包装缺陷。
3. 气体压力控制检测
含气饮料需在特定压力下完成灌装以维持气体溶解性。检测中需通过压力传感器实时监控灌装腔内的气体压力,确保其稳定在设定值(如碳酸饮料通常要求3~5bar)。重点验证设备在高速运行时的压力补偿能力,以及突发停机后的恢复性能,防止因压力波动引发液沫喷溅或气体逸出。
4. 微生物污染风险检测
设备清洁度对食品安全至关重要。需对灌装阀、输料管道等关键部位进行微生物采样,检测是否存在细菌或霉菌污染。同时验证CIP(原位清洗系统)的有效性,确保清洗后残留物符合GB 14881等食品安全标准。对于无菌灌装设备,还需检测紫外灭菌或高温灭菌装置的杀菌效率。
5. 设备材质与兼容性检测
灌装封盖机的材质需耐腐蚀、抗磨损,且符合食品级要求。检测时需验证不锈钢部件的耐酸性(如接触柠檬酸饮料后的腐蚀情况),以及密封圈等橡胶件的抗老化性能。此外,针对不同瓶型(如PET瓶、玻璃瓶)需检测夹瓶机构的适配性,避免因机械应力导致瓶体破损。
6. 自动化系统与故障诊断检测
现代灌装封盖机普遍搭载PLC控制系统和传感器网络。检测需覆盖人机界面操作响应、故障报警触发机制及数据追溯功能。通过模拟断瓶、缺盖等异常工况,验证设备能否快速停机并准确定位故障源,最大限度减少停机时间。
7. 长期运行稳定性测试
通过连续72小时以上的满载运行测试,评估设备在高温、高湿环境下的耐久性。记录关键部件(如伺服电机、传动齿轮)的温升、振动等参数变化,预测设备寿命并制定预防性维护计划。
检测结果的应用与优化建议
检测完成后需形成综合报告,量化设备性能指标并提出改进方案。例如,对灌装精度不达标的设备,可能需校准流量计或优化阀门响应速度;密封性不足时,则需调整封盖扭矩或更换磨损的O型圈。定期检测数据还可为设备升级提供依据,助力企业实现智能化、绿色化生产转型。
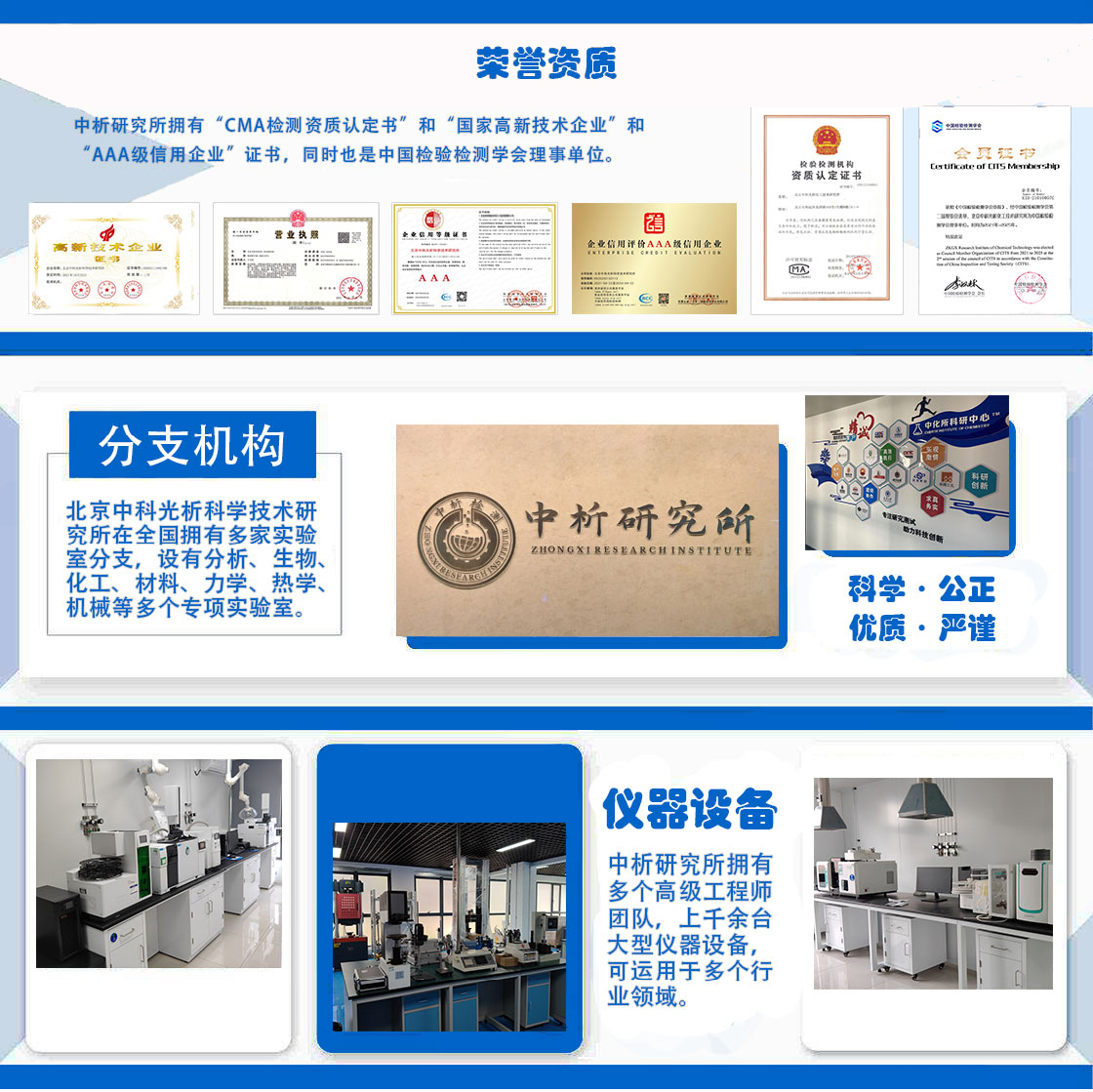
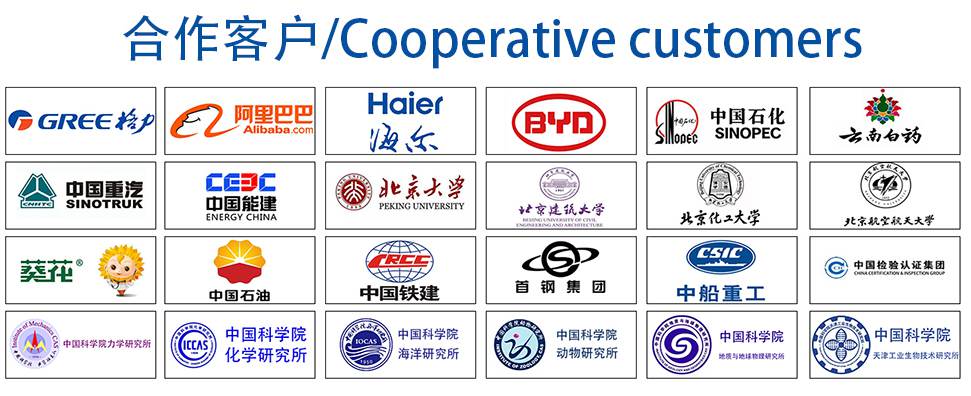