内燃机水散热器检测的重要性
内燃机水散热器作为发动机冷却系统的核心组件,承担着将高温冷却液热量快速散发到空气中的关键任务。其性能直接影响发动机的工作温度、燃油效率和整体寿命。据行业统计,约35%的发动机故障与冷却系统异常相关,其中散热器问题占比超过60%。通过系统性检测可及时发现散热器堵塞、泄漏、结构变形等问题,避免发动机过热导致的拉缸、烧瓦等严重故障,同时确保冷却液循环效率,维持发动机最佳工作温度区间(通常为80-95℃)。
核心检测项目及方法
1. 密封性检测
使用专用压力测试仪向散热器施加1.2-1.5倍工作压力(通常0.15-0.3MPa),保压时间不少于5分钟。重点检查散热器芯体、进出水管接头、放水阀等部位是否存在渗漏。电子检漏仪可精准定位0.1mm级微泄漏点,氦气质谱检测法适用于高精度密封要求场景。
2. 散热效率测试
在模拟工况条件下,测量进水口与出水口温差应保持8-12℃区间。采用红外热像仪扫描散热片温度分布,合格产品温差梯度不超过15℃/㎡。新风流速检测需达到2.5-4m/s,散热面积折损率不得超过原始设计的5%。
3. 内部清洁度检测
通过内窥镜检查水道沉积物厚度,使用水质电导率仪测量冷却液污染度。标准规定水道内壁沉积物不得超过0.5mm,电导率应小于2000μS/cm。超声波清洗配合磁力除垢可恢复90%以上流通截面积。
4. 结构强度试验
振动台模拟车辆行驶工况,进行X/Y/Z三轴向各20万次振动测试。爆破压力需达到工作压力的3倍以上,翅片焊点脱落率不得超过0.5%。采用数字图像相关技术(DIC)分析应力分布状态。
智能检测技术应用
最新检测体系集成AI视觉识别系统,可自动判断散热片变形程度;搭载粒子图像测速仪(PIV)精确分析流体动力学特性;基于大数据建立的散热器健康度评估模型,能预测剩余使用寿命并生成维修建议报告。
检测周期建议
常规车辆每2万公里或12个月需进行基本检测,工程机械等高负荷设备应缩短至500工作小时。检测后需建立包含散热性能曲线、密封参数、材质损耗率等数据的电子档案,为预防性维护提供依据。
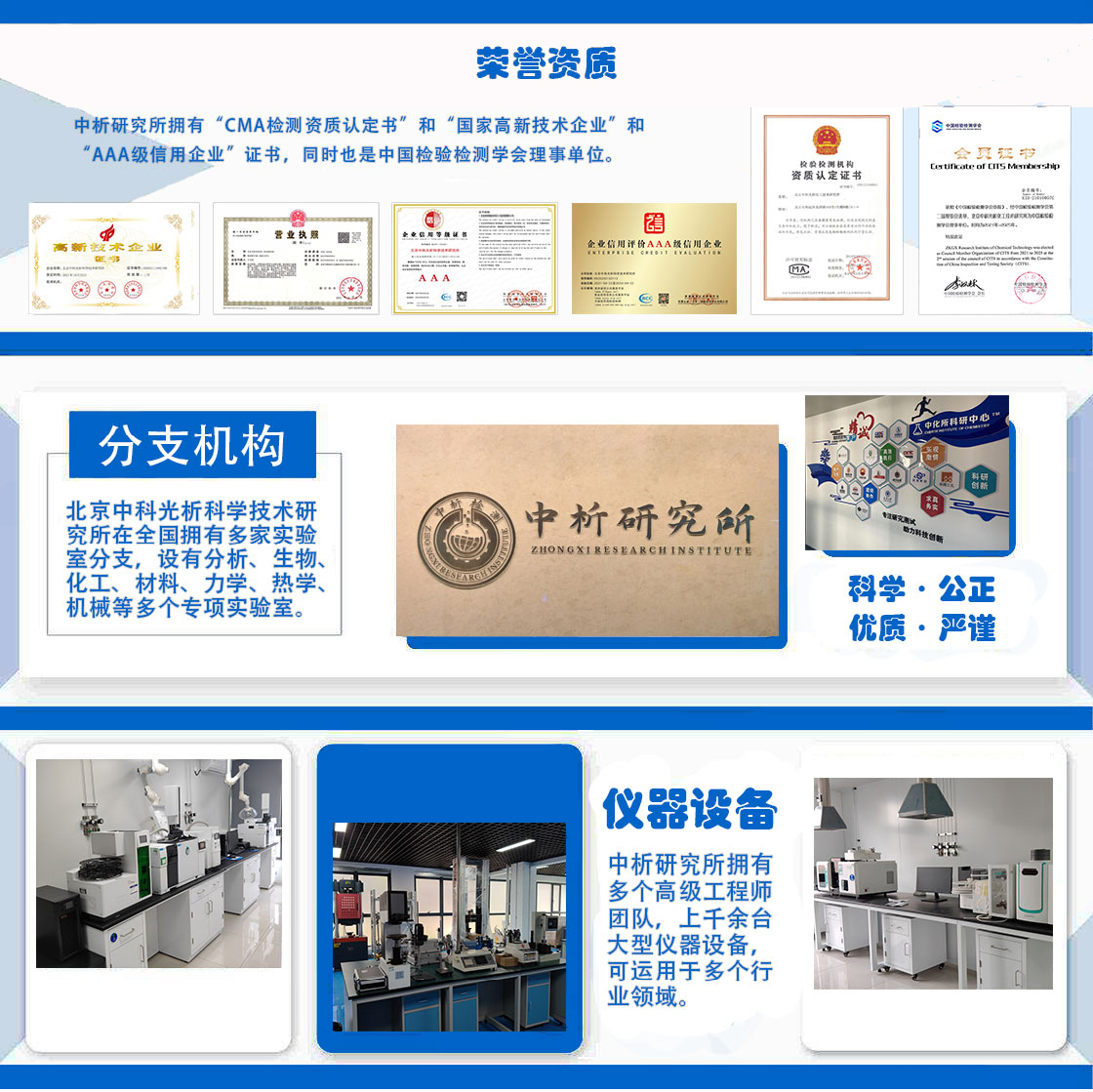
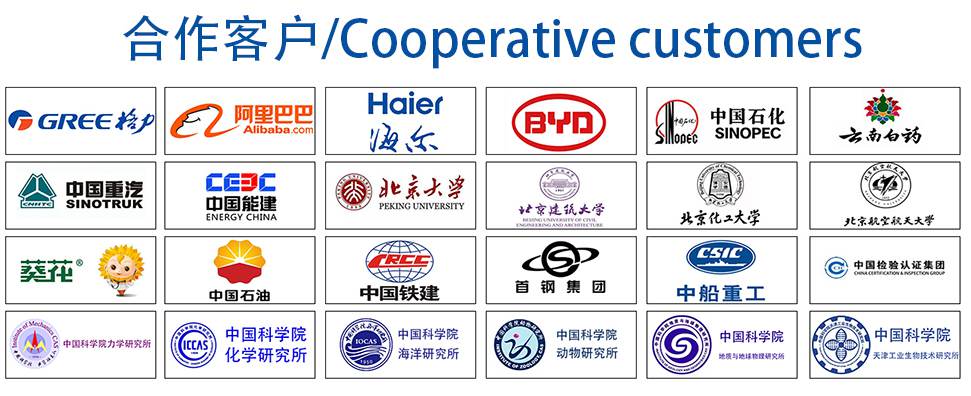