内燃机气缸套检测的重要性
内燃机气缸套作为发动机的核心部件,承担着密封燃烧室、引导活塞运动以及传递热量的关键功能。其工作环境极其恶劣,长期承受高温、高压、腐蚀性气体和机械磨损的考验。气缸套的质量和性能直接影响发动机的功率输出、燃油效率、排放水平及使用寿命。因此,针对气缸套的系统化检测是保障发动机可靠运行、预防故障、延长维护周期的重要技术手段。现代工业中,气缸套检测已贯穿于制造、装配、维修全生命周期,涉及几何尺寸、材料性能、表面状态等多维度分析。
核心检测项目及方法
1. 尺寸精度检测
通过三坐标测量仪(CMM)或专用量具对气缸套的内径、外径、长度等关键尺寸进行精密测量,确保其符合设计公差要求。对于磨损后的旧缸套,需重点检测内径椭圆度、锥度变化,判断是否超出允许修复范围。
2. 表面粗糙度与形貌分析
使用表面轮廓仪或原子力显微镜(AFM)对缸套内壁进行微观形貌扫描,评估珩磨网纹的均匀性、沟槽深度及分布密度。表面粗糙度(Ra/Rz值)直接影响润滑油膜形成能力,需控制在0.4-1.6μm范围内。
3. 硬度与耐磨性测试
采用洛氏硬度计或显微硬度计测定缸套基体及表面镀层(如镍基碳化硅涂层)的硬度值,验证热处理工艺效果。通过摩擦磨损试验机模拟实际工况,评价材料的抗磨粒磨损和黏着磨损性能。
4. 金相组织检验
对缸套材料进行剖切、研磨、腐蚀后,利用金相显微镜观察石墨形态(铸铁缸套)、晶粒度、碳化物分布等微观结构,排查铸造缺陷(缩孔、夹渣)或热处理异常导致的组织不均匀问题。
5. 耐腐蚀与密封性检测
通过盐雾试验、电化学腐蚀测试评估缸套在酸性燃烧产物环境中的耐蚀能力。使用气压/水压试验装置检查缸套与缸体装配后的密封性能,确保冷却水腔无渗漏风险。
6. 裂纹与缺陷探伤
综合运用磁粉探伤(MT)、超声波探伤(UT)或工业CT扫描技术,检测缸套表面及内部的微裂纹、气孔、夹杂物等缺陷,尤其关注应力集中区域(如法兰过渡处)。
智能化检测技术发展趋势
随着工业4.0技术的普及,激光扫描三维重建、AI图像识别算法、在线监测传感器等新技术逐步应用于气缸套检测领域。例如,基于机器视觉的自动缺陷分类系统能实现毫秒级裂纹识别,而嵌入式温度/振动传感器可实时监控缸套工况。这些创新手段显著提升了检测效率和数据可靠性,为发动机健康管理提供精准决策支持。
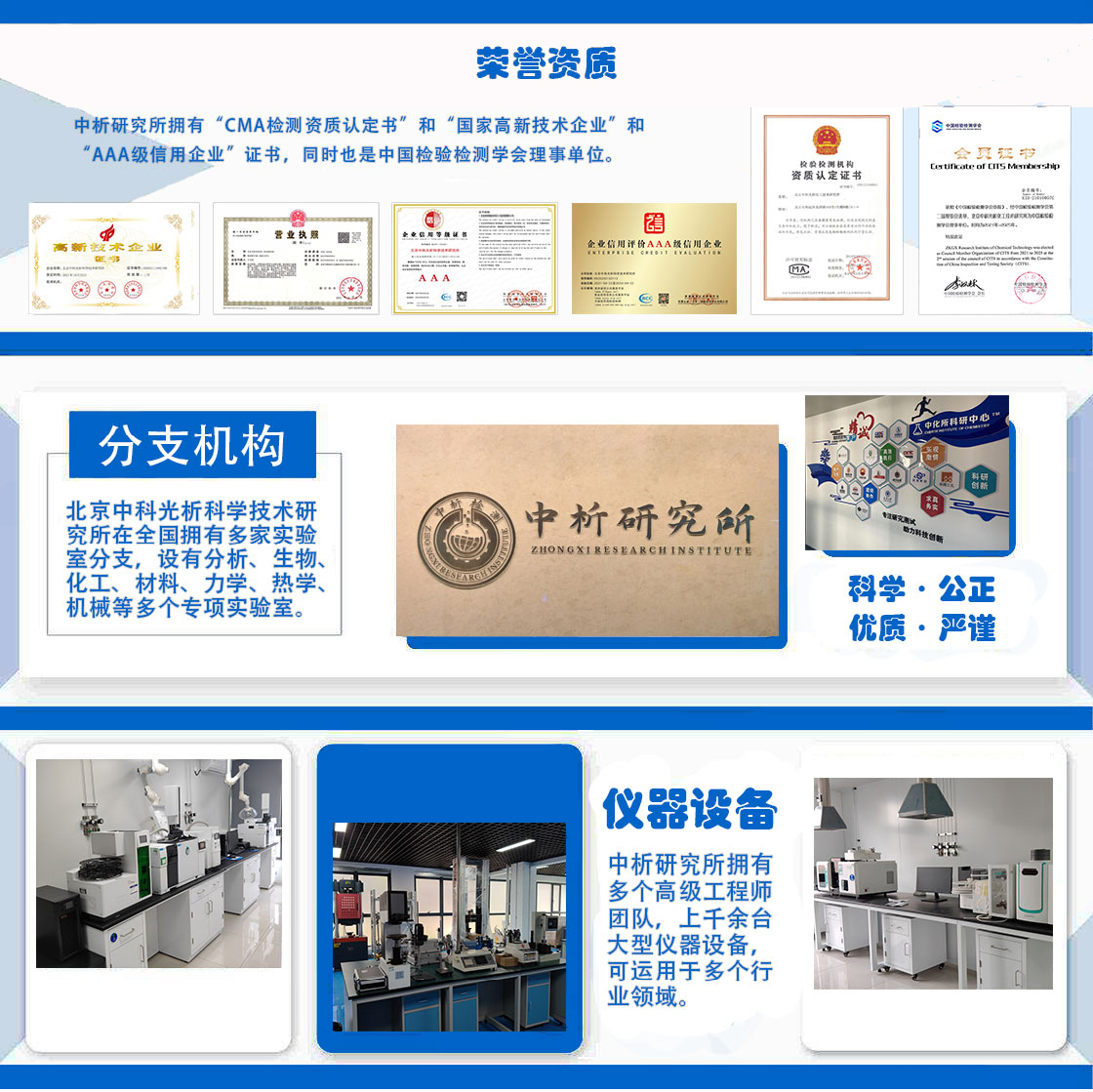
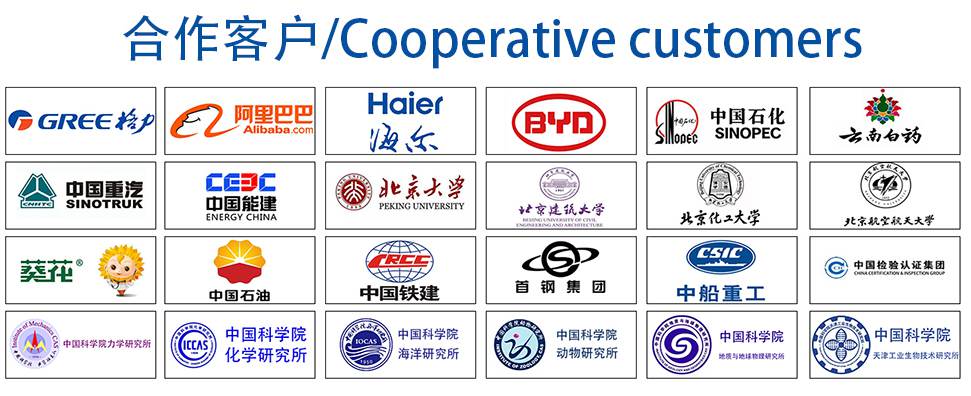