行列式制瓶机检测的重要性与核心内容
行列式制瓶机作为玻璃容器生产中的核心设备,其性能直接影响瓶罐产品的质量、生产效率及企业成本。随着食品、药品、日化等行业对玻璃包装容器的精度、均匀性和外观要求日益严格,定期对行列式制瓶机进行系统性检测成为保障生产稳定性的关键环节。通过对机械结构、控制系统、成型工艺参数等项目的精确检测,可有效预防模具磨损、温度偏差、气压异常等问题,避免因设备故障导致的废品率上升或生产线停工,同时确保产品符合国家标准(如GB 4544-2020《玻璃容器》)、行业规范和客户定制化需求。
核心检测项目分类与技术要求
1. 机械结构完整性检测
重点检查行列式制瓶机的传动系统、模具夹持机构和分度装置:
• 使用激光对中仪检测导料筒与初型模的同心度(偏差≤0.05mm)
• 通过振动分析仪评估齿轮箱、凸轮机构的磨损状态
• 验证模具开合同步性(时差≤0.1秒)和夹持力均匀性(压差≤5%)
• 检测润滑系统油路压力(0.2-0.4MPa)及分配器工作状态
2. 温度控制系统检测
采用红外热成像仪结合K型热电耦进行多维度监测:
• 料道区域温度均匀性(±2℃)与梯度分布曲线
• 初型模工作温度(650-750℃)闭环控制精度
• 退火炉各温区(预热、保温、缓冷段)的温度稳定性
• 冷却风管风压(800-1200Pa)与流量匹配性测试
3. 成型工艺参数验证
运用高速摄像系统与压力传感器进行动态分析:
• 吹气时序(0.5-1.2秒)与压力曲线(0.3-0.6MPa)匹配度
• 滴料重量波动范围(±0.5g)与剪切时序精度(±0.01秒)
• 模具表面粗糙度(Ra≤0.8μm)与涂层完整性检测
• 行列式分度精度(角度偏差≤0.05°)验证
4. 电气与控制系统检测
通过PLC程序诊断与信号追踪确保控制精度:
• 伺服电机定位重复精度(±0.02mm)测试
• 气动电磁阀响应时间(≤10ms)与泄漏率检测
• 人机界面参数设置与设备实际执行值比对
• 安全联锁装置(急停、防护门)功能验证
5. 成品质量关联性检测
建立设备参数与最终产品的量化关系模型:
• 瓶口尺寸(高度公差±0.15mm)与模具磨损相关性分析
• 壁厚分布(CV值≤3%)与吹制压力的函数关系
• 耐内压强度(≥1.2MPa)与退火工艺参数的优化匹配
• 外观缺陷(气泡、条纹)与熔融玻璃温度的关联诊断
检测周期与数据化管理
建议按照生产批次实施动态检测机制:
• 连续生产8小时后进行关键参数快速校验
• 每季度执行全面预防性检测(含精度校准)
• 建立设备健康状态数据库,运用AI算法预测维护周期
• 通过MES系统实现检测数据与生产订单的智能关联
通过系统的检测体系实施,行列式制瓶机的设备综合效率(OEE)可提升15%-20%,产品合格率稳定在98.5%以上。现代检测技术(如机器视觉、数字孪生)的融合应用,正在推动玻璃制瓶行业向智能化、可追溯化方向发展。
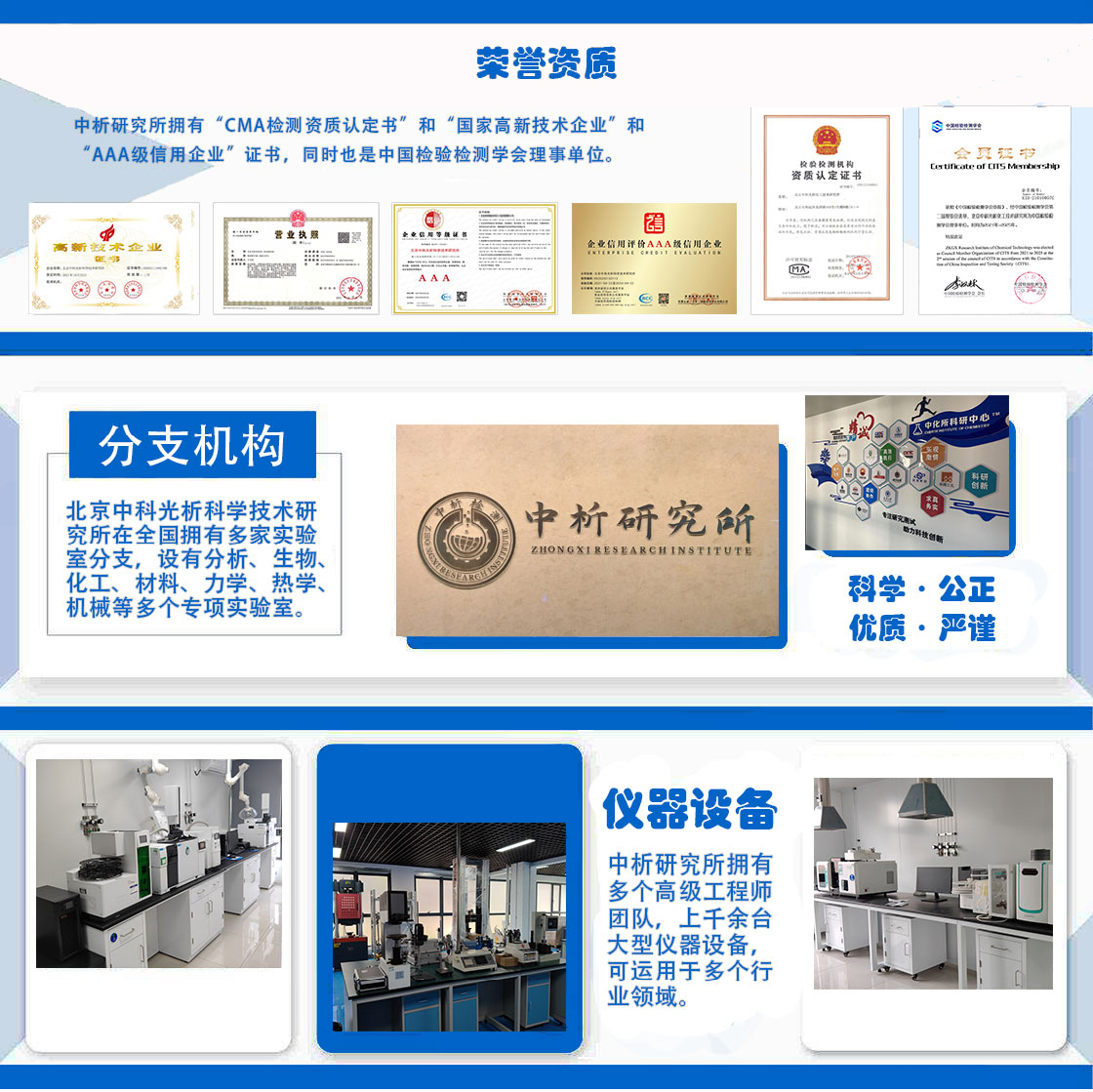
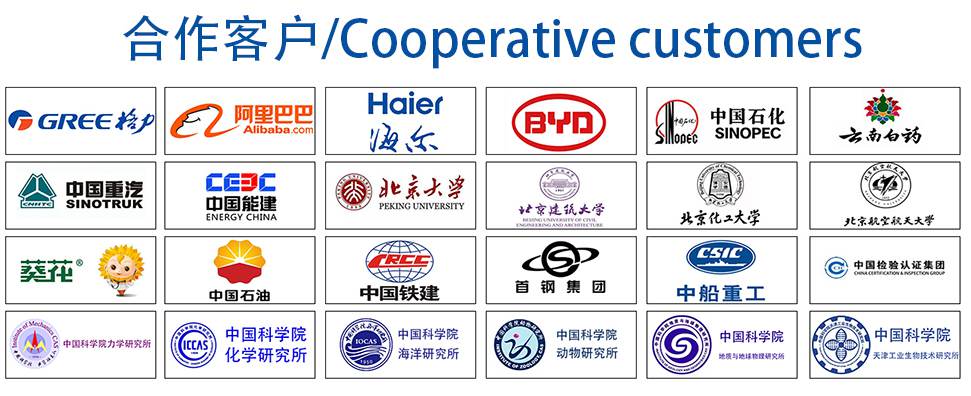