航天器组件检测:保障太空探索安全的核心环节
航天器作为人类探索宇宙的核心载体,其可靠性直接关系着数亿元级研发投入的成败以及航天员的生命安全。在极端温度、真空辐射、剧烈振动等严苛的太空环境中,任何微小的组件缺陷都可能导致灾难性后果。航天器组件检测通过系统性、多维度的技术手段,对推进系统、热防护层、电子设备等核心部件进行全方位质量评估,确保每个零件从材料性能到装配精度均符合设计要求。随着商业航天的发展和新材料技术的突破,检测标准已从传统破坏性测试升级为智能化、高精度的无损检测体系,覆盖研发验证、生产质控、发射前复检全流程。
关键检测项目与技术应用
1. 推进系统完整性检测
采用X射线断层扫描(CT)与超声波探伤技术,检测燃料储罐焊缝质量及阀门密封性,通过氦质谱检漏仪定位微米级泄漏点。燃烧室需经受2000℃以上高温模拟测试,同时用高速摄像机捕捉燃料喷射动态。
2. 热防护系统性能验证
通过等离子风洞模拟再入大气层时的气动加热环境,检测隔热瓦的烧蚀速率与结构强度。使用红外热像仪实时监测防护涂层的热传导分布,结合材料微观结构分析预测长期服役性能。
3. 结构组件疲劳强度测试
在振动台上开展三轴随机振动试验,模拟发射阶段的力学冲击。应用光纤光栅传感器网络,持续监测桁架结构在载荷作用下的应变分布,建立全生命周期健康预测模型。
4. 电子系统电磁兼容性检测
于屏蔽暗室中测试导航计算机、通信模块的抗电磁干扰能力,采用故障注入技术验证冗余系统切换逻辑。高精度时域反射仪(TDR)可定位电路板微短路缺陷至0.1mm精度。
智能化检测技术的突破
基于机器视觉的自动光学检测(AOI)系统可识别太阳能帆板0.02mm级别的装配偏差,AI算法处理效率较人工提升40倍。量子传感技术的引入使磁场检测灵敏度达到pT级,有效预警推进剂管路腐蚀隐患。数字孪生平台通过实时数据融合,实现组件性能退化趋势的可视化预测。
国际标准与未来趋势
当前检测流程严格遵循NASA-STD-5009与ECSS-Q-ST-70-08C标准体系,商业航天企业正推动模块化自检技术的发展。随着在轨维护需求增长,具备自诊断功能的智能组件与微型化检测机器人将成为行业新焦点,为实现深空探测任务提供技术保障。
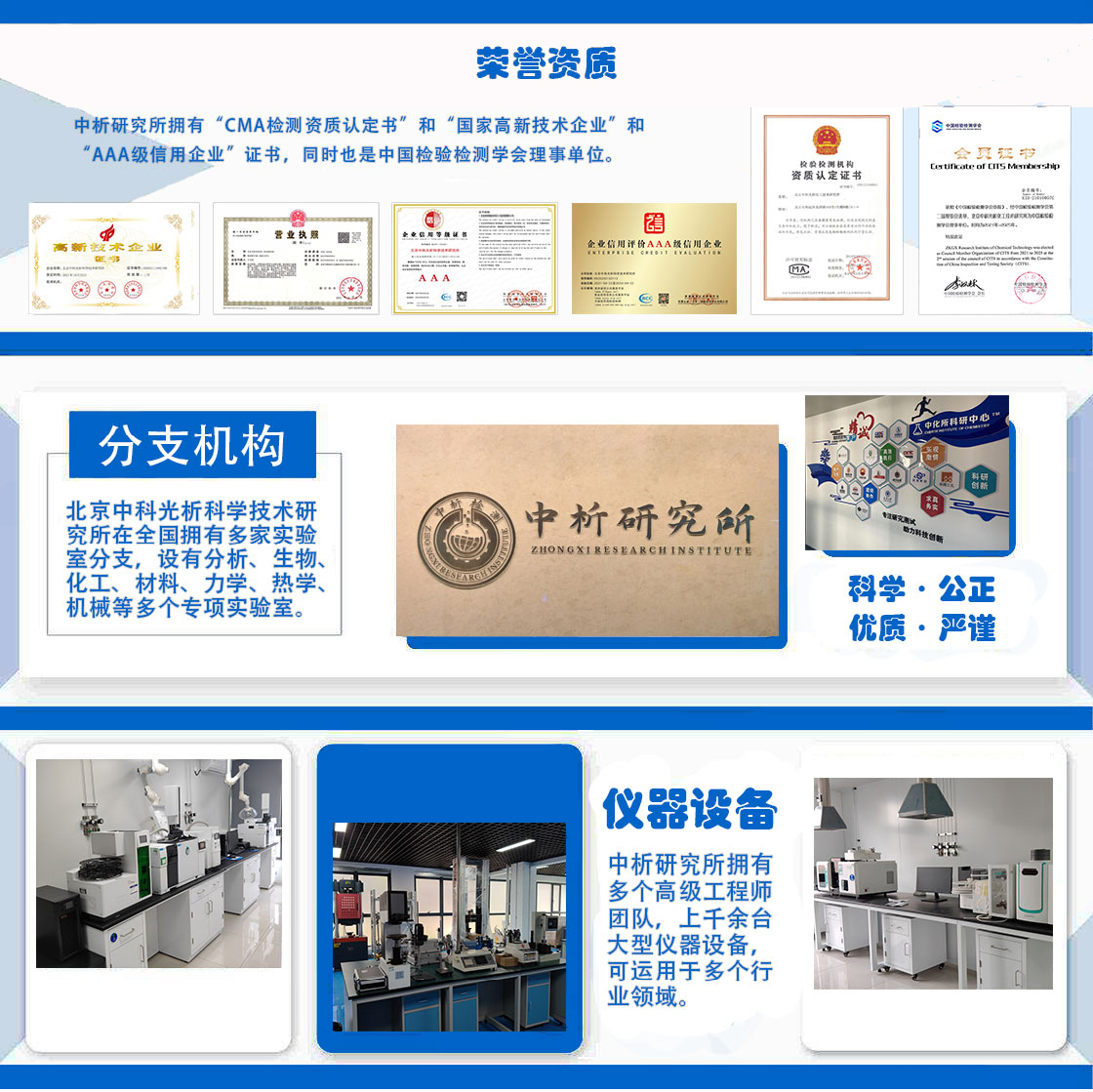
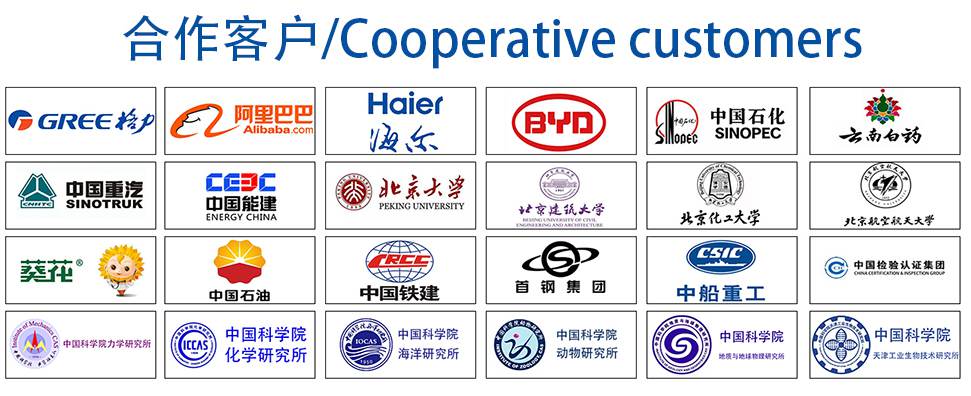