涂漆质量检测的重要性与核心内容
在工业制造、建筑装修及汽车生产等领域,涂漆工艺既是产品防护的关键屏障,也是提升外观价值的重要手段。涂漆质量直接影响材料的耐腐蚀性、耐磨性以及客户对产品的第一印象。据统计,因涂层缺陷导致的返工成本约占制造总成本的15%-25%,而通过系统性涂漆质量检测,能够将产品不良率降低60%以上。一套完整的涂漆质量检测体系需要覆盖从基材处理到最终成膜的每个环节,尤其是在环保法规趋严和客户要求升级的背景下,检测项目正朝着更高精度、更智能化的方向发展。
核心检测项目解析
1. 外观与表面质量检测
采用目视检查与仪器分析相结合的方式,重点检测流挂、橘皮、针孔等常见缺陷。使用60倍放大镜观察微观表面,配合光泽度计测量涂层反射率(标准值通常为60-90GU)。新型三维表面轮廓仪可量化分析粗糙度参数Ra值,精度达0.1μm。
2. 涂层附着力测试
执行划格法(ASTM D3359)时需选用0-5级标准图谱比对,高质量涂层应达到4B级以上。拉拔试验(ISO 4624)通过液压装置测量剥离强度,汽车原厂漆要求不低于5MPa。最新研发的激光划痕法可实现非破坏性动态监测。
3. 干膜厚度测定
磁性测厚仪(铁基材)与涡流测厚仪(非铁基材)需按ISO 2808标准校准。乘用车电泳底漆厚度应控制在18-22μm,面漆系统总厚度需达80-120μm。便携式XRF光谱仪可实现多层复合涂层的无损检测。
4. 耐腐蚀性能验证
盐雾试验(ASTM B117)要求中性盐雾环境下500小时无红锈,循环腐蚀测试(CCT)模拟真实环境更严苛。电化学阻抗谱(EIS)可量化评估涂层防护性能,阻抗值>1×10^8Ω·cm²为优质标准。
5. 颜色与光泽一致性控制
采用分光测色仪测量ΔE色差值,汽车修补漆要求ΔE≤0.5。多角度光泽度检测(20°、60°、85°)配合大数据分析,可追溯批次间差异。智能比色系统已实现与Pantone色卡的自动匹配。
6. 环境耐受性测试
紫外老化试验(QUV)需满足2000小时光照后保光率>80%,耐化学品测试包含汽油浸泡(72h)、制动液接触(24h)等项目。新能源汽车电池箱体涂层要求通过IP67防水测试。
智能化检测技术发展
当前工业4.0体系下,机器视觉检测系统可达到每分钟300件的高速检测,AI算法对气泡缺陷的识别准确率超过98%。在线式红外热像仪能实时监控烘烤固化温度曲线,物联网平台实现检测数据的云端管理和质量追溯。随着纳米压痕技术、太赫兹成像等新方法的引入,涂漆质量检测正向微观尺度和数字化方向深度演进。
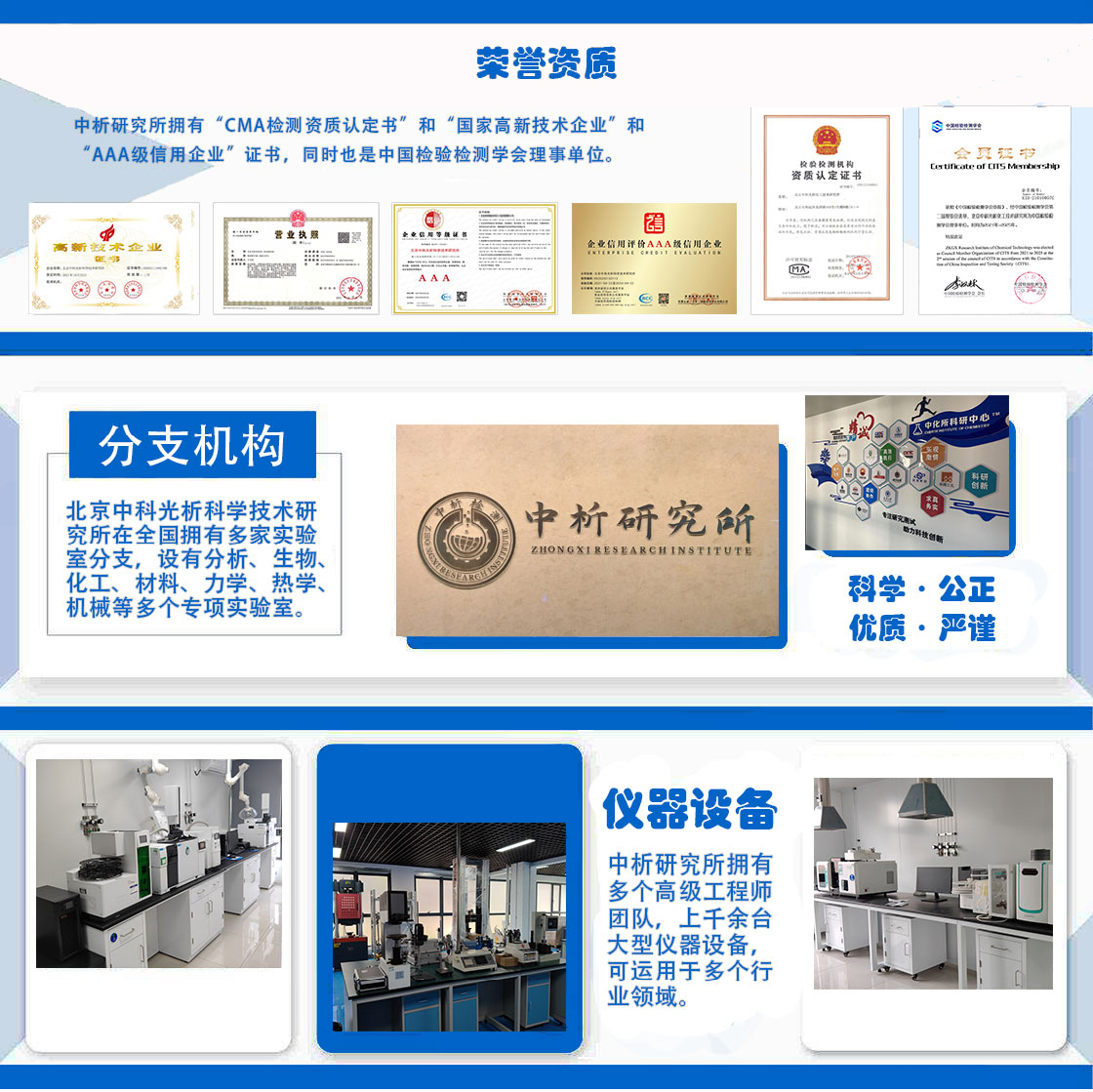
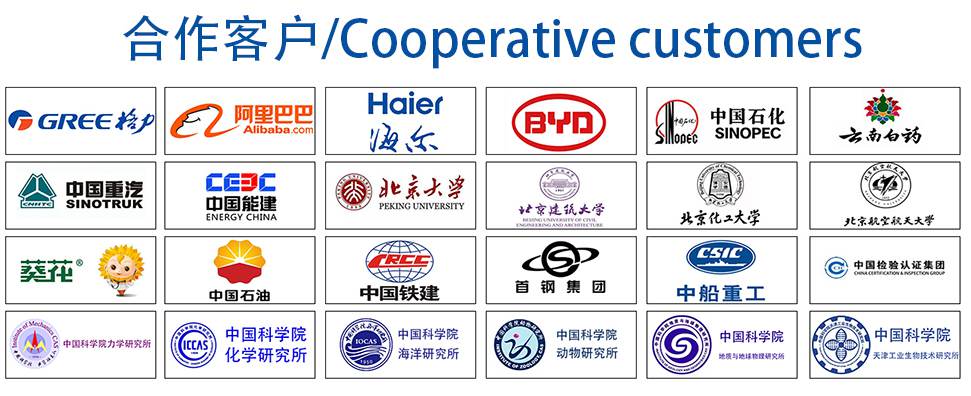