不含气液体玻璃瓶装生产线检测体系概述
不含气液体(如果汁、乳制品、药品溶液等)的玻璃瓶装生产线检测是保障产品质量、安全性和合规性的核心环节。作为传统包装形式,玻璃瓶凭借其化学稳定性、环保可回收性及高透明度的特点,在食品、药品和化妆品领域广泛应用。然而,其生产流程需面对玻璃材质易碎、密封性要求严格、液体灌装精度高等挑战,因此需通过多维度检测技术构建全流程质量监控体系。现代生产线通常整合机械视觉、传感器技术、自动化控制与数据追溯系统,实现从原料瓶检测到成品包装的闭环管理。
核心检测项目与技术方案
1. 玻璃瓶外观缺陷检测
采用高分辨率工业相机配合多角度光源,通过机器视觉系统检测瓶体裂纹、气泡、杂质及形状畸变。使用AI算法实时比对标准瓶型数据库,缺陷检出率可达99.8%。对瓶颈、瓶底等易损部位实施多光谱扫描,确保无肉眼不可见微裂纹。
2. 密封性及耐压测试
使用负压衰减法或压力浸水法验证瓶盖密封性能,检测系统需模拟运输震动环境,持续监测0.3-0.6MPa压力下的泄漏量。针对药品等高要求产品,配备氦气质谱检漏仪,灵敏度可达1×10⁻⁹ Pa·m³/s。
3. 灌装精度与容量控制
配置动态称重模块和液体流量计,实时监控灌装量偏差。采用质量流量计控制精度达±0.5%,结合自动剔除装置对超差产品进行分选。定期使用标准量筒进行计量校准,符合ISO 9001标准要求。
4. 微生物与异物防控检测
在洁净灌装区设置在线粒子计数器,监测空气悬浮粒子浓度(符合GMP A级标准)。采用X射线异物检测机识别玻璃碎片、金属杂质,灵敏度达0.3mm。对终产品进行ATP生物荧光检测,30秒内获取微生物污染指标。
5. 标签与喷码完整性验证
通过OCR字符识别系统核对生产日期、批次号信息,检测标签错贴、褶皱及缺失情况。使用激光打码质量分析仪验证二维码可读性,确保追溯码DPM值≥1.5。对UV油墨固化度进行光谱分析,防止运输途中的标识磨损。
6. 液位一致性视觉检测
在高速传输线上部署线阵CCD相机,通过液面反光特征分析灌装高度。系统可自动补偿不同瓶型的透视畸变,检测速度达800瓶/分钟,液位控制精度±1mm,有效避免因泡沫或挂壁造成的误判。
7. 产线环境监控系统
集成温湿度传感器、压差监测模块,确保灌装区保持正压(10-15Pa)及20-25℃恒温状态。紫外线强度检测仪实时监控消毒灯效能,数据接入中央控制系统实现预警联动。
智能化质量控制发展趋势
当前行业正加速推进数字孪生技术的应用,通过3D建模同步模拟物理产线与检测系统。引入深度学习算法优化缺陷分类模型,结合MES系统实现检测数据与生产参数的闭环优化。未来,区块链技术有望为每瓶产品建立全生命周期质量档案,进一步提升质量追溯效率与可信度。
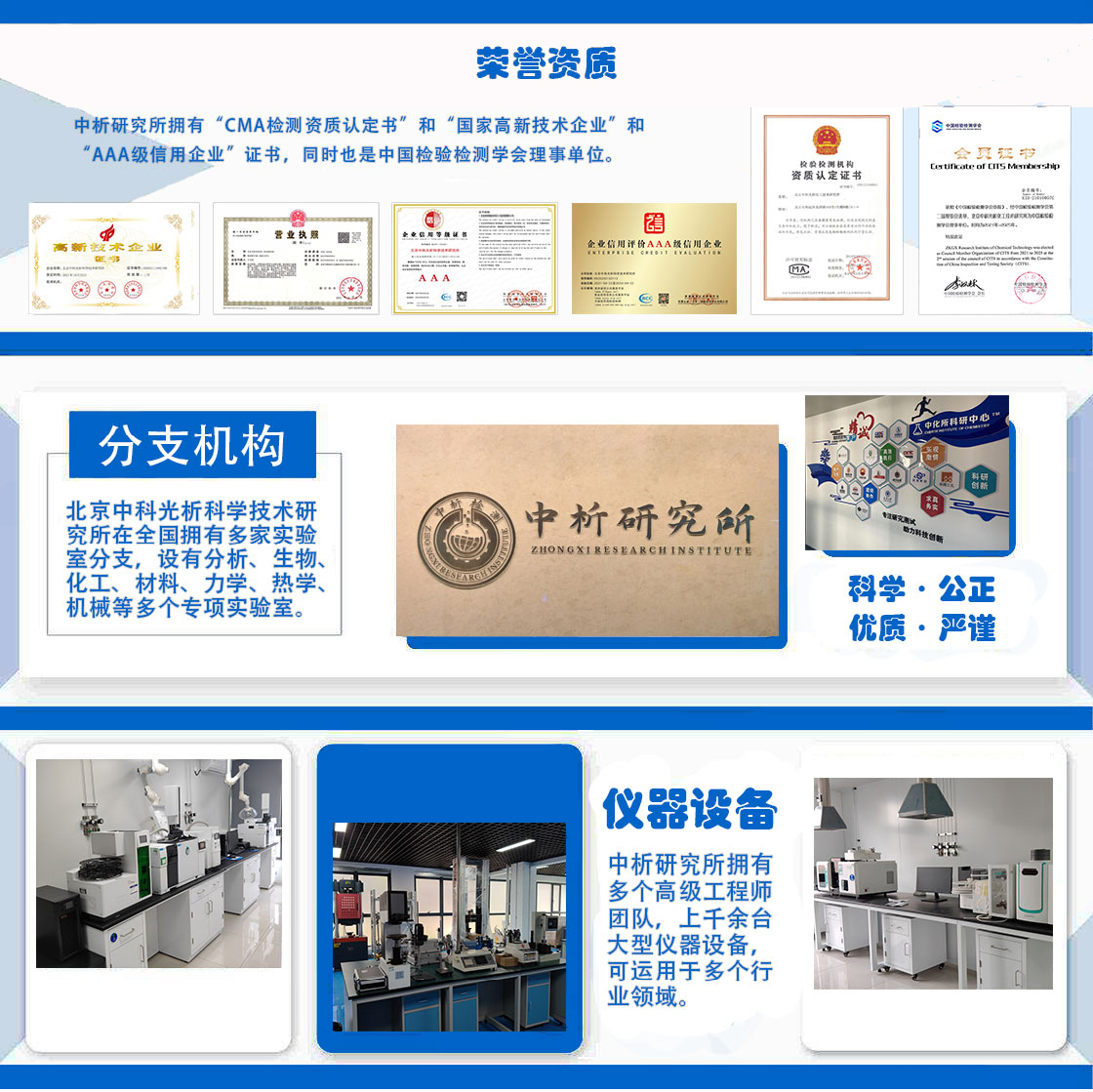
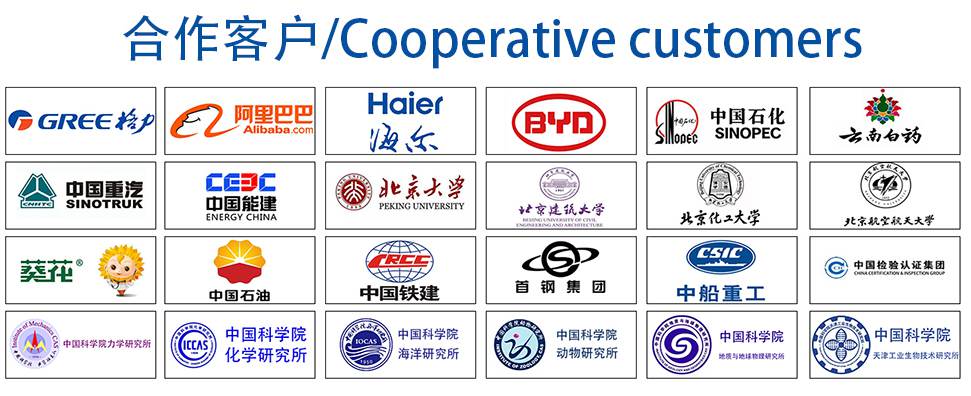