纵向分切机检测的重要性与核心内容
纵向分切机作为卷材加工领域的关键设备,广泛应用于纸张、薄膜、金属箔、无纺布等材料的精密分切。其性能直接影响产品分切精度、生产效率及设备使用寿命。为确保设备稳定运行并满足高标准生产要求,定期开展纵向分切机检测成为企业质量控制和设备维护的核心环节。检测内容需覆盖机械结构、电气系统、安全防护及裁切质量等多个维度,通过科学的检测手段及时发现潜在隐患,避免因设备故障导致的材料浪费或安全事故。
纵向分切机核心检测项目
1. 机械结构精度检测
重点检测刀轴与放卷/收卷轴的平行度、垂直度,使用激光对中仪或千分表测量偏差值。导轨直线度误差需控制在0.02mm/m以内,刀片安装座的重复定位精度应通过标准试块验证,确保分切过程中刀片轨迹的稳定性。同时需检查压辊压力平衡性,避免材料偏移或起皱。
2. 动力系统性能检测
包含主电机扭矩输出稳定性测试、传动系统齿轮/皮带磨损度评估以及变频器参数校准。通过振动频谱分析判断轴承状态,使用转速表验证各轴转速同步精度(通常要求误差≤±0.5%)。张力控制系统的响应时间和波动范围需使用专业仪器进行动态测试。
3. 裁切质量专项检测
采用千分尺测量分切带宽的一致性(精度需达±0.1mm),使用高倍放大镜检查切口毛刺率。通过设定不同速度档位进行连续分切试验,统计废品率并分析边料收卷的整齐度。材料张力波动需通过张力传感器记录曲线,确保控制在工艺要求范围内。
4. 安全防护功能验证
紧急制动系统需在0.5秒内完成停机响应,防护罩联锁装置应进行200次以上开闭测试。安全光栅灵敏度需用标准测试棒校验,确保有效探测距离偏差不超过±5mm。过载保护、漏电保护等电气安全功能需通过模拟故障场景进行触发验证。
5. 环境适应性检测
在温湿度变化环境下(如15-35℃、30-80%RH)进行48小时连续运行测试,观察设备精度漂移量。使用声级计测量设备噪音(行业标准通常要求≤75dB),通过振动测试仪检测异常频率,预防共振导致的机械损伤。
6. 周期性维护检测项目
包括润滑油污染度分析、气动元件密封性测试、电气线路绝缘电阻测量(应≥5MΩ)。每季度进行齿轮箱磨损金属颗粒检测,每年开展整机几何精度复检。建议建立数字化检测档案,通过数据趋势分析预判部件更换周期。
通过上述系统化检测可有效延长纵向分切机使用寿命,据统计,规范执行检测程序可使设备故障率降低60%以上,同时提升分切良品率3-5个百分点。企业应根据设备使用强度制定分级检测计划,并配备专业检测工具与标准化作业流程。
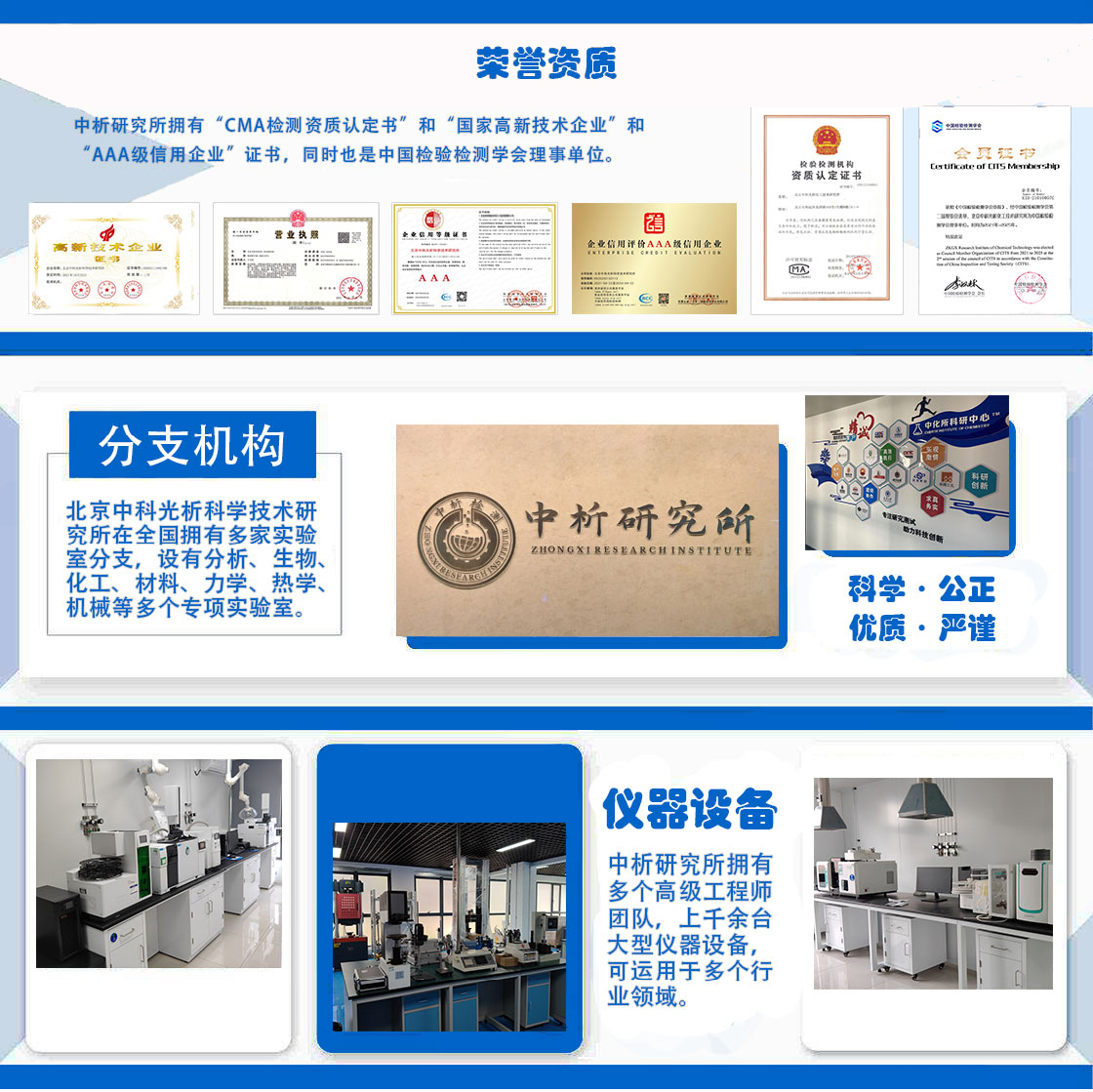
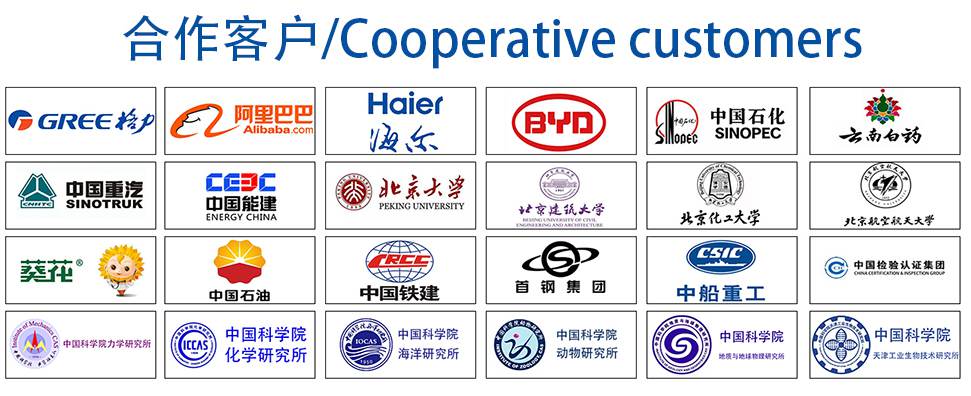