全自动吹瓶机检测的重要性与核心内容
全自动吹瓶机作为食品、医药、日化等行业包装生产的核心设备,其运行稳定性和安全性直接影响产品质量与生产效率。随着生产工艺要求的提升和智能化技术的应用,设备检测已成为保障吹瓶工艺达标、降低故障率的关键环节。通过系统性检测,可精准定位设备磨损、参数偏差、控制系统异常等问题,避免因设备隐患导致的原料浪费或生产线停滞,同时满足ISO 9001、GMP等行业质量认证的硬性要求。
全自动吹瓶机核心检测项目
1. 机械性能检测
包括传动系统稳定性测试(主轴转速偏差≤±1%)、模具开合精度检测(重复定位精度≤0.02mm)、气动/液压系统压力波动监测(波动范围需控制在额定值的±5%内)。需使用激光测振仪、压力传感器等设备对机械振动、气缸动作响应时间进行量化分析。
2. 温度控制检测
重点验证加热模块温控精度(红外测温仪测量偏差应≤±2℃)、冷却系统效率(瓶胚降温速度需达到工艺曲线要求)以及热电偶校准状态。对于PET原料吹瓶机,模温均衡性需确保各区域温差<3℃。
3. 气密性与压力测试
通过保压试验检测高压气路密封性(30秒内压降不得超过0.05MPa),验证吹气压力稳定性(波动值≤±0.2bar)。需特别关注减压阀、换向阀等关键部件的耐久性表现。
4. 电气控制系统检测
涵盖PLC程序逻辑验证(动作时序误差<50ms)、伺服电机扭矩输出测试(与设定值偏差≤3%)、HMI人机界面响应测试。需使用示波器记录I/O信号延迟,并模拟突发断电检验数据保存功能。
5. 成品质量关联检测
采用瓶壁测厚仪(厚度均匀性误差≤5%)、爆破压力测试机(符合ASTM D2659标准)、透光率检测仪等设备,量化分析吹制瓶体的物理性能指标,反向追溯设备参数设置合理性。
6. 安全防护装置检测
包括紧急停止按钮响应测试(动作时间≤0.5秒)、防护门互锁功能验证、过载保护触发阈值校准。需符合机械安全标准EN ISO 13849-1的PL等级要求。
检测周期与方法建议
建议实施三级检测体系:日常点检(每班次进行气路压力、温度示值检查)、月度维护(传动部件润滑度检测、控制系统固件升级)、年度大检(全面性能评估与关键部件寿命预测)。对于高速机型(产能≥8000瓶/小时),应增加轴承磨损的振动频谱分析频次。
通过建立完善的检测档案和数字化运维系统,企业可显著提升设备综合效率(OEE),将非计划停机时间降低40%以上,同时确保吹制容器100%符合食品级接触材料的安全规范。
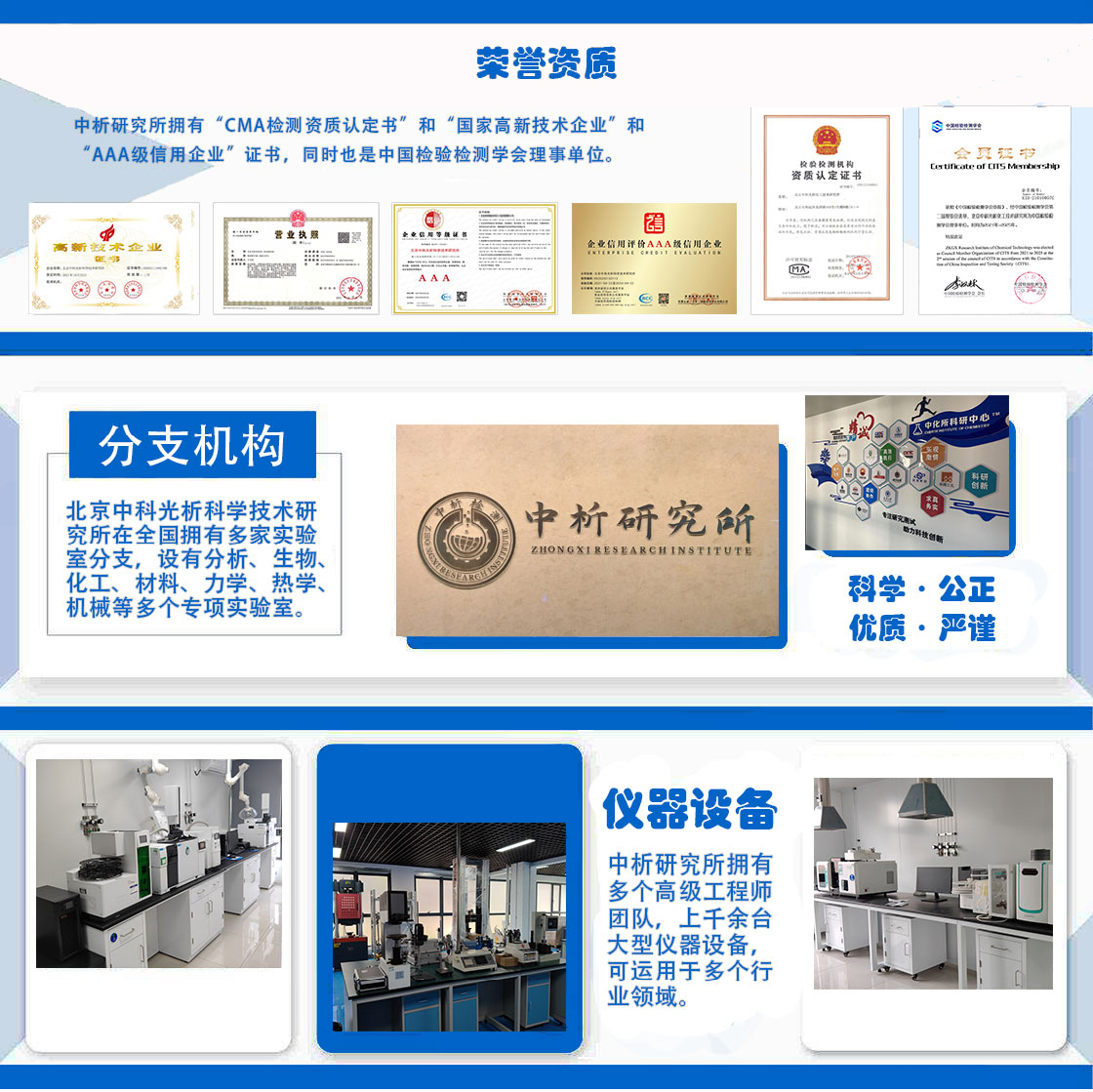
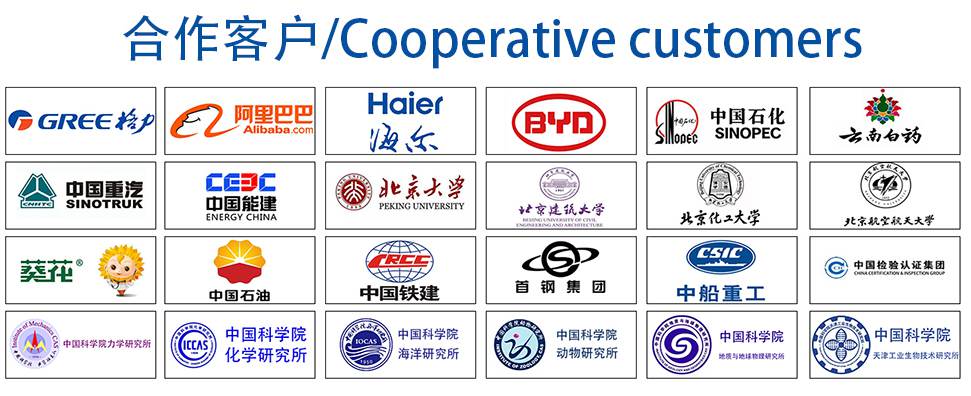