角度位置指示器检测的重要性与技术要求
角度位置指示器作为机械系统、航空航天设备及工业自动化领域中的核心传感器,其精度与可靠性直接关系到设备运行的安全性与效率。该装置通过实时反馈旋转部件或执行机构的角度信息,为闭环控制系统提供关键数据支持。在航空发动机、数控机床、机器人关节等高精度场景中,角度位置指示器的检测误差超过0.1°就可能引发连锁故障。因此,建立完善的检测体系,覆盖从静态校准到动态响应等全方位测试项目,已成为保障设备性能的必要手段。
核心检测项目体系
1. 静态精度校准测试
使用高精度分度头配合激光干涉仪,在恒温条件下进行360°全量程多点校准。检测时需控制环境温度波动≤±1℃,重点验证线性度误差、零点漂移及回程差等指标。最新ISO 230-2标准要求工业级设备的角度重复性误差≤±0.05°。
2. 动态响应特性测试
通过伺服电机驱动平台模拟不同转速工况(0-5000rpm),使用高速数据采集系统记录信号延迟与波形畸变情况。关键参数包括:阶跃响应时间(应<2ms)、频率带宽(需>200Hz)以及振动环境下的信号稳定性。
3. 环境适应性验证
在温湿度试验箱中执行-40℃至+85℃的温度循环测试,同时进行湿热(95%RH)、盐雾(5%NaCl溶液)等严苛环境试验。军用标准MIL-STD-810G规定,经72小时环境试验后,绝缘电阻需保持>100MΩ,输出信号波动<±0.1%FS。
4. 电磁兼容性(EMC)测试
依据IEC 61000-4系列标准,进行辐射抗扰度(80MHz-1GHz场强10V/m)、静电放电(±8kV接触放电)及电源线浪涌(±2kV)等测试。合格产品应在电磁干扰下保持输出噪声<0.5%量程,且不出现数据跳变现象。
5. 机械耐久性考核
搭建模拟工况测试台,执行连续100万次全行程往复运动。检测内容包括轴承磨损量(应<5μm)、接触电阻变化(ΔR<10%)及信号连续性。航空级产品还需通过GJB 150.16A规定的三轴随机振动试验(20-2000Hz,20g RMS)。
智能化检测技术发展
随着工业4.0技术的普及,基于数字孪生的虚拟标定系统正在兴起。通过建立精确的传感器数学模型,可在完成30%实体测试后预测全量程性能,使检测周期缩短40%。同时,机器学习算法可自动识别温度补偿曲线中的非线性特征,将校准精度提升至0.01°级别。
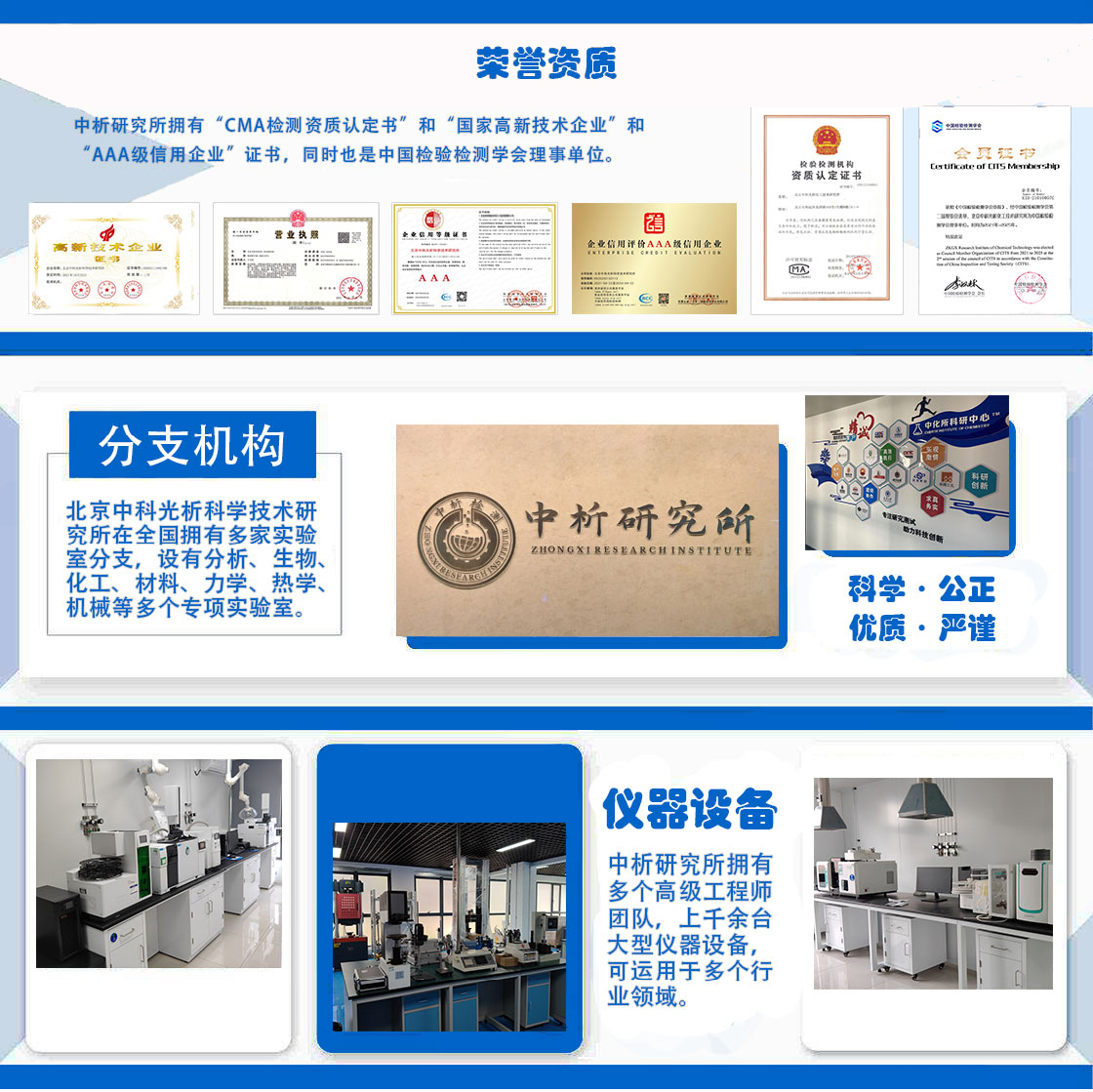
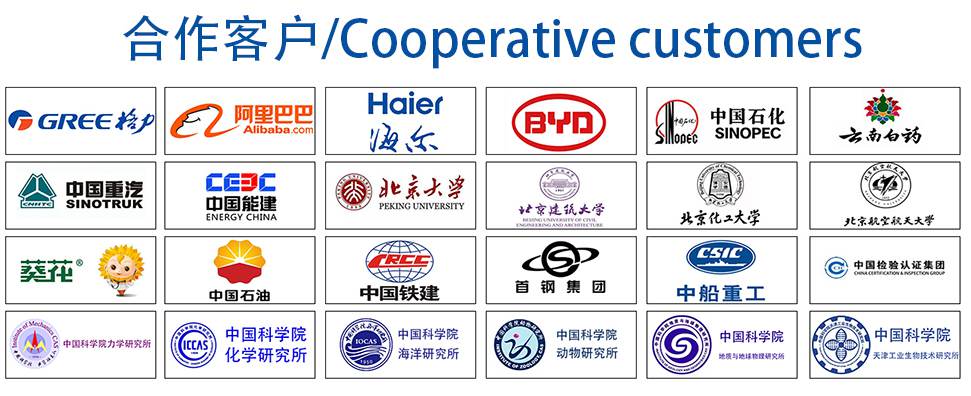