纸箱印刷成型生产线检测的关键项目与实施要点
随着包装行业对生产效率与产品质量要求的不断提升,纸箱印刷成型生产线的自动化检测已成为保障生产稳定性和市场竞争力的核心环节。该生产线涵盖印刷、模切、粘箱、堆码等多个工序,需要通过系统性检测手段确保设备性能、工艺参数及成品质量的全面达标。专业的检测体系能够最大限度减少次品率、降低损耗成本,同时满足食品、电子、医药等行业对包装箱强度、印刷精度及环保性能的严苛要求。
一、印刷质量检测
印刷环节重点检测色差控制、套印精度和图案完整性。采用在线印刷质量自动检测系统(如CCD相机+图像处理软件)实时监控颜色偏差,检测标准需符合Pantone色卡或客户指定色域范围。套印误差应控制在±0.15mm以内,对于二维码、条形码等特殊标识需通过专用读取设备验证可识别性。
二、模切精度检测
模切刀模的定位精度直接影响纸箱成型质量,需通过激光位移传感器测量刀口位置偏差,X/Y轴向误差应≤0.1mm。定期使用标准测试版进行全尺寸验证,重点检查边角切割完整度与压痕深度一致性,确保折叠线位置符合设计图纸±0.3mm公差要求。
三、成型稳定性检测
在粘箱成型段需监测胶水涂布量、粘合强度及箱体方正度。使用红外测厚仪检测胶层厚度(通常要求80-120μm),通过剥离试验机测试粘接部位抗拉强度(≥3.5N/cm²)。三维激光扫描仪可快速检测箱体对角线误差,确保成型尺寸符合GB/T 6543标准。
四、材料性能检测
原纸板环压强度(RCT)、边压强度(ECT)和耐破强度需定期抽样检测,瓦楞纸板含水率应控制在8-12%区间。印刷面纸的吸墨性、耐磨性测试同样关键,可采用摩擦试验机模拟运输环境进行500次循环测试。
五、设备运行状态监测
建立PLC数据采集系统,对伺服电机扭矩、齿轮箱温度、传送带张力等关键参数进行实时监控。振动分析仪可提前发现轴承磨损异常,设备综合效率(OEE)需持续优化,建议维持>85%的基准值。
六、环保与安全检测
油墨VOC排放需符合GB 38507-2020强制标准,定期进行车间空气质量检测。电气系统绝缘电阻应>10MΩ,紧急停机装置响应时间须<0.5秒,机械防护装置需通过EN ISO 13849安全认证。
通过构建覆盖全流程的检测体系,企业不仅能提升纸箱生产的良品率,还可实现设备预测性维护与工艺参数优化。建议采用机器视觉+工业物联网的智能检测方案,结合AI算法建立质量缺陷数据库,推动纸箱生产线向数字化、智能化方向升级。
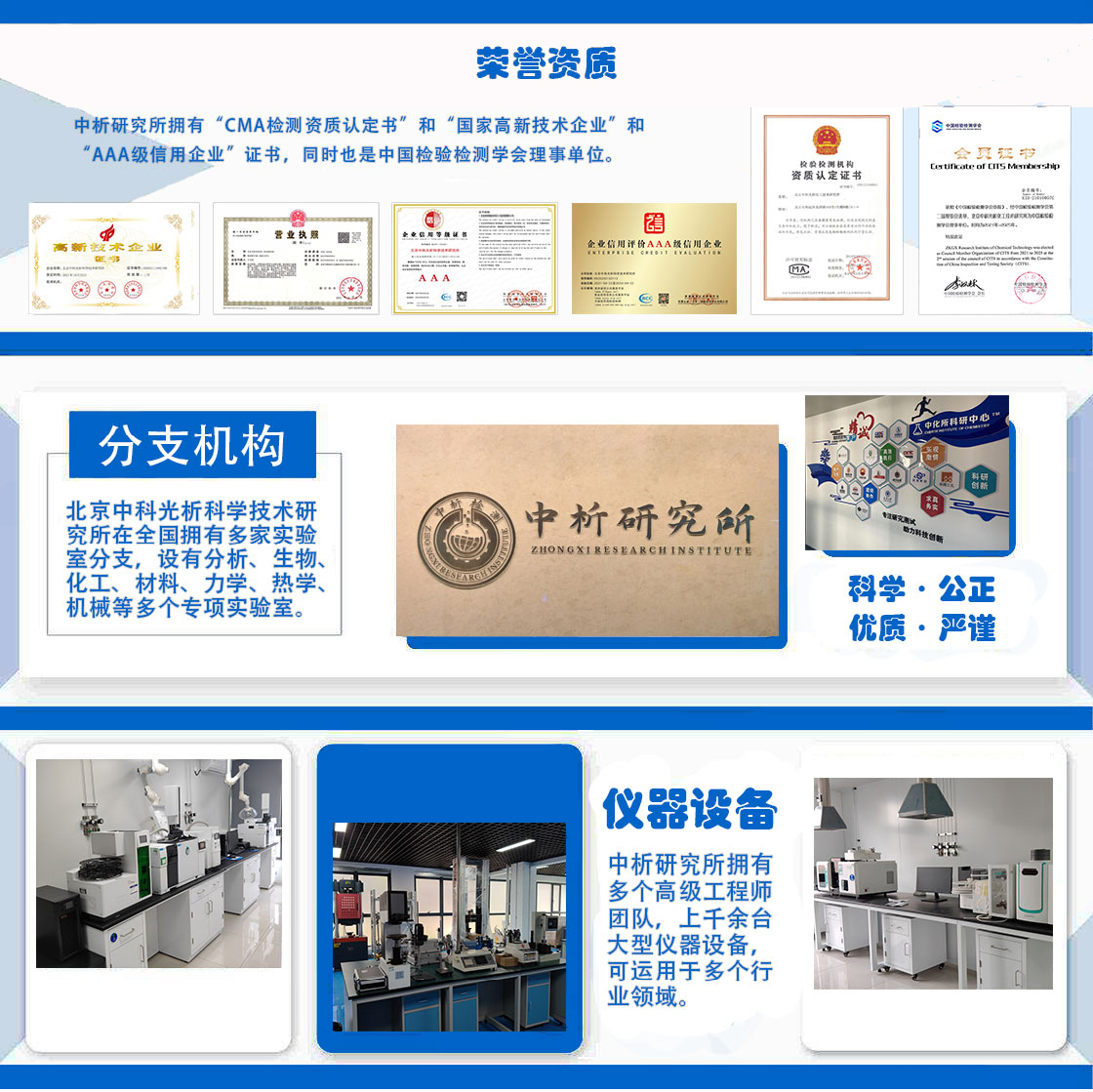
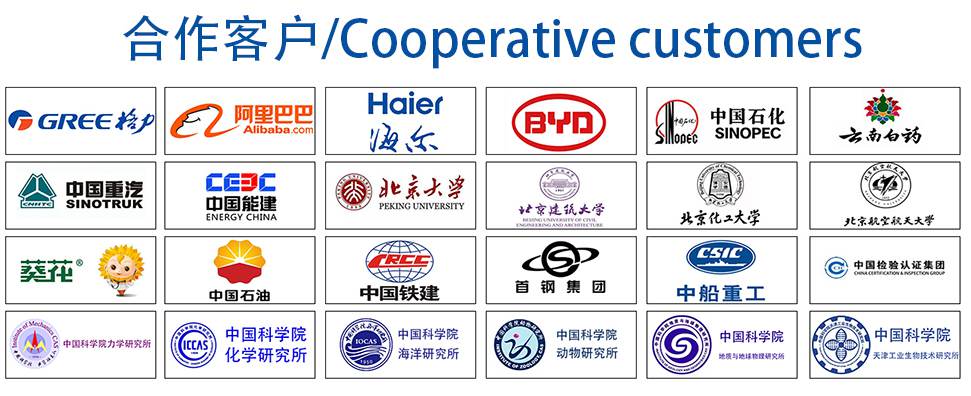