钢铁及合金材料检测的重要性
钢铁及合金作为工业生产和建筑领域的核心材料,其质量直接关系到工程安全、设备寿命和产品性能。随着材料技术的进步,不锈钢管、角钢、圆盘条、钢筋等衍生品广泛应用于机械制造、建筑工程、交通运输等领域。然而,材料在冶炼、加工、运输过程中可能因成分偏差、工艺缺陷或环境侵蚀导致性能下降。因此,通过科学系统的检测项目对材料进行全方位分析,成为保障材料合规性、安全性和功能性的必要手段。检测不仅需要覆盖成分、力学性能等基础指标,还需结合具体应用场景制定针对性测试方案。
主要检测项目及标准
1. 化学成分分析
通过光谱分析仪(如ICP-OES、XRF)检测材料中碳、硅、锰、铬、镍等关键元素含量,确保符合GB/T 223系列、ASTM E415等标准。尤其对不锈钢管需重点验证铬镍比及抗腐蚀元素含量。
2. 力学性能测试
包括拉伸试验(检测抗拉强度、屈服强度、延伸率)、冲击试验(-40℃低温冲击韧性)、硬度测试(布氏/洛氏/维氏硬度)。角钢需额外关注弯曲强度,钢筋需验证反复弯曲性能(GB/T 28900)。
3. 金相组织检测
利用金相显微镜观察晶粒度、夹杂物等级及分布(GB/T 10561)、奥氏体不锈钢的晶间腐蚀倾向(GB/T 4334),判断材料热处理工艺的合理性。
4. 尺寸与表面质量检测
不锈钢管需测量壁厚均匀度(超声波测厚仪)、椭圆度;角钢检测边宽、边厚偏差(GB/T 706);圆盘条检验直径公差(GB/T 14981);钢筋表面需排查裂纹、结疤等缺陷(GB 1499.2)。
5. 特殊性能测试
不锈钢管需进行盐雾试验(ASTM B117)评估耐蚀性;高温合金需测试蠕变强度;海洋工程用材料需做应力腐蚀开裂(SCC)试验;钢筋需验证焊接接头性能(JGJ 18)。
检测流程与质量控制
检测过程遵循“抽样-预处理-实验分析-数据比对-报告签发”标准化流程,采用CMA/ 认证设备,每批次留存实物样品及检测记录。对争议结果需启动复核机制,通过第三方实验室交叉验证确保数据权威性。
结语
针对钢铁及合金材料的系统性检测,不仅能够有效预防因材料缺陷引发的工程事故,更为企业优化生产工艺、降低质量成本提供数据支撑。随着智能检测技术的发展,无损检测(如TOFD超声成像)、大数据质量追溯等新方法将进一步推动行业标准化进程。
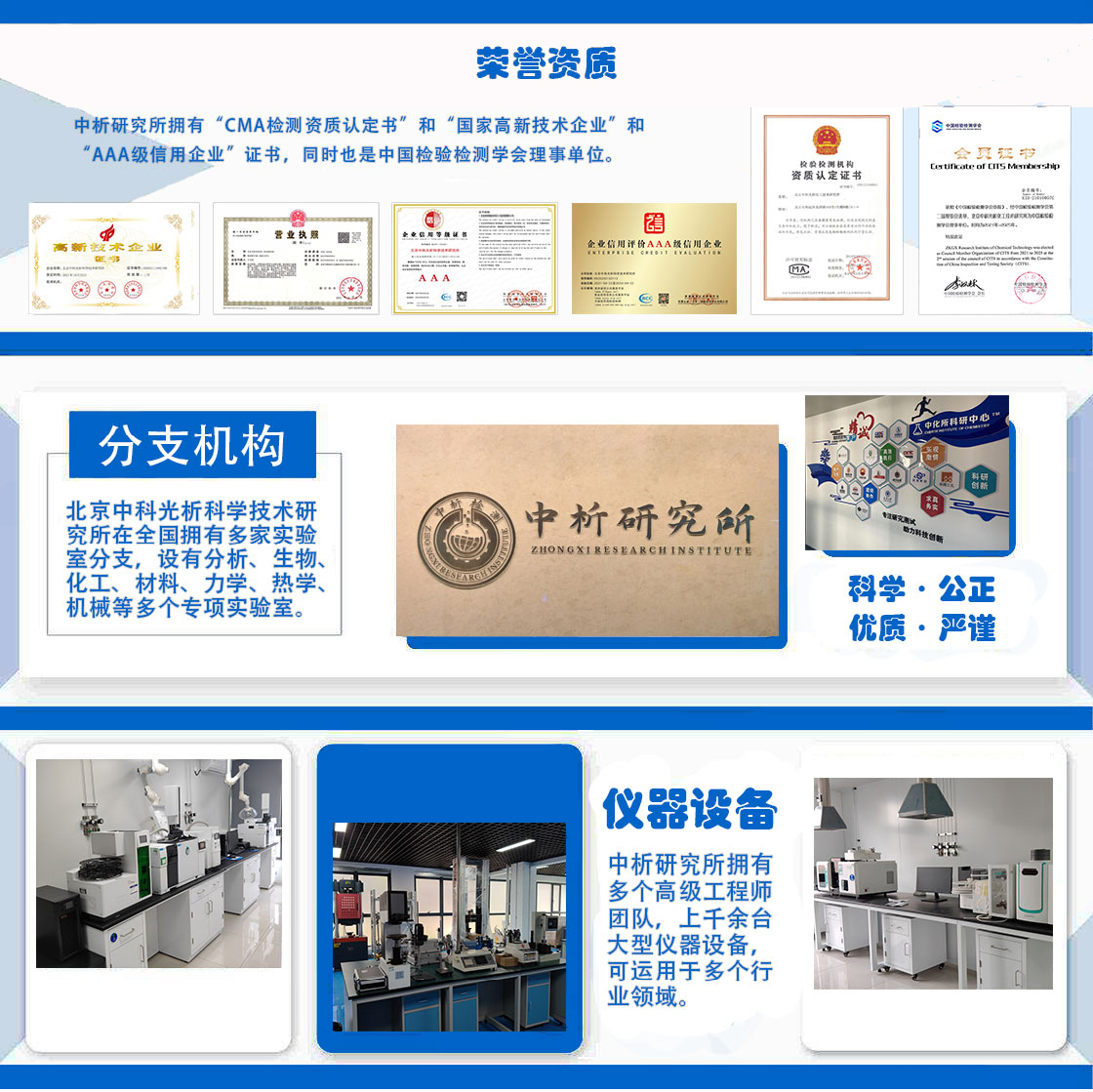
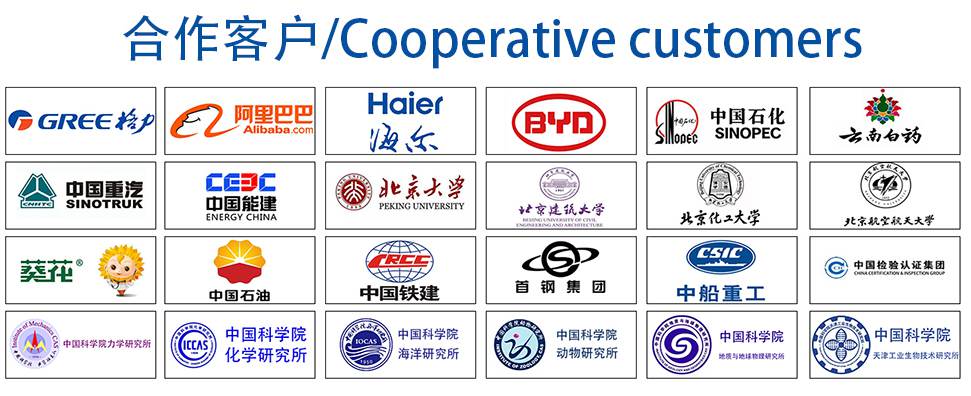