数字化胶印机检测的重要性与技术要求
随着印刷行业向智能化、数字化方向快速转型,数字化胶印机已成为现代印刷生产的核心设备。这类设备集成了精密机械、电子控制、色彩管理及数字化流程技术,其性能直接影响印刷品的质量、生产效率及成本控制。为确保设备稳定运行并达到最佳输出效果,定期开展科学化、标准化的数字化胶印机检测成为企业技术管理的核心环节。通过系统性检测,可精准识别设备老化、参数偏移、软件适配性等问题,同时为预防性维护和工艺优化提供数据支撑。
核心检测项目及实施方法
1. 机械与电气系统基础检测
重点检查设备传动机构、滚筒同心度、压力调节装置等机械部件的磨损情况,使用激光测距仪和振动分析仪评估运行精度。电气系统需测试伺服电机响应速度、电路板信号稳定性及电源波动容错能力,确保控制指令的精准执行。
2. 数字化色彩管理系统校准
通过分光光度计和色彩管理软件,验证设备是否符合ISO 12647印刷标准。检测内容包括油墨预置准确性、网点扩大率、灰平衡稳定性等参数,并生成ICC特性文件以实现跨设备的色彩一致性。
3. 网络化控制模块功能性验证
针对数字化胶印机的JDF/JMF数据传输、远程监控及MES系统对接功能,模拟生产订单下发、状态反馈和数据追溯流程,检测网络延迟、协议兼容性及数据加密可靠性,保障工业4.0环境下的协同生产能力。
4. 印刷压力与温度闭环控制测试
采用压力传感薄膜和红外热成像技术,实时监测滚筒间压力分布和干燥系统温度场,结合PLC控制逻辑分析动态调节性能,防止因局部压力不均导致的网点变形或纸张褶皱问题。
5. 软件系统兼容性及版本迭代检测
验证RIP软件、工作流程系统与设备固件的版本匹配度,通过压力测试评估多任务并发处理能力。同时检测新版本驱动程序的稳定性,避免因升级造成的功能冲突或数据丢失风险。
6. 安全防护与故障自诊断能力评估
模拟急停按钮触发、安全光栅遮挡等异常场景,记录设备响应时间和故障代码生成准确性。利用内置传感器数据分析模块,验证设备对滚筒卡纸、油墨泄漏等常见故障的预测准确率。
7. 耗材适配性综合测试
对不同品牌油墨、润版液及版材进行适配实验,检测网点还原度、水墨平衡调节效率及印版耐印力。通过量化数据建立耗材性能数据库,为采购决策提供技术依据。
检测结果分析与优化策略
完成检测后需生成多维度的评估报告,包括设备健康度评分、关键参数偏离阈值列表及改进建议。对于高频次出现的异常项,建议采用机器学习算法建立预测模型,逐步实现从被动维修向主动维护的转型。通过持续迭代检测方案,可显著降低设备宕机时间,延长核心部件寿命,最终推动印刷企业实现降本增效的数字化转型目标。
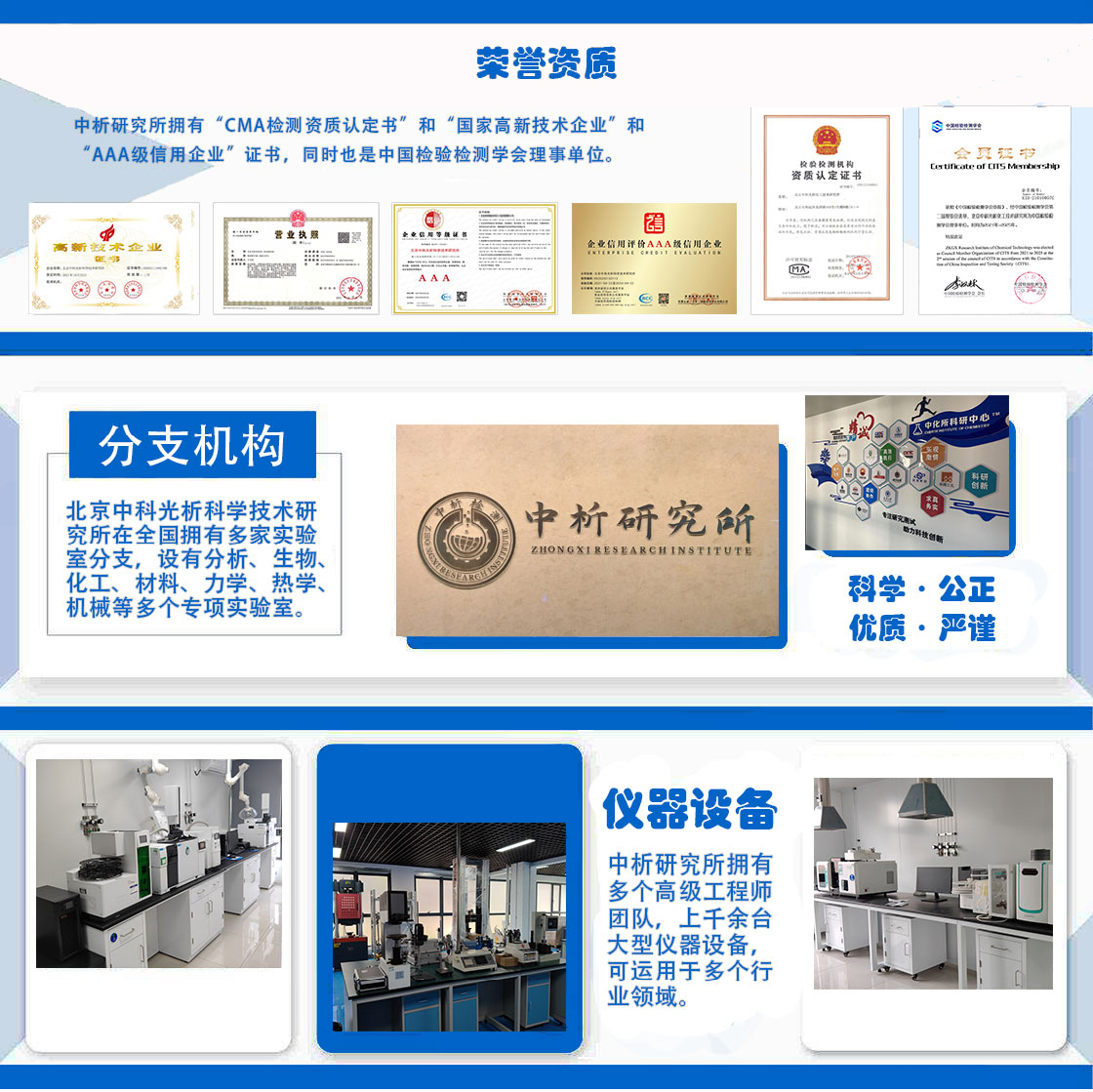
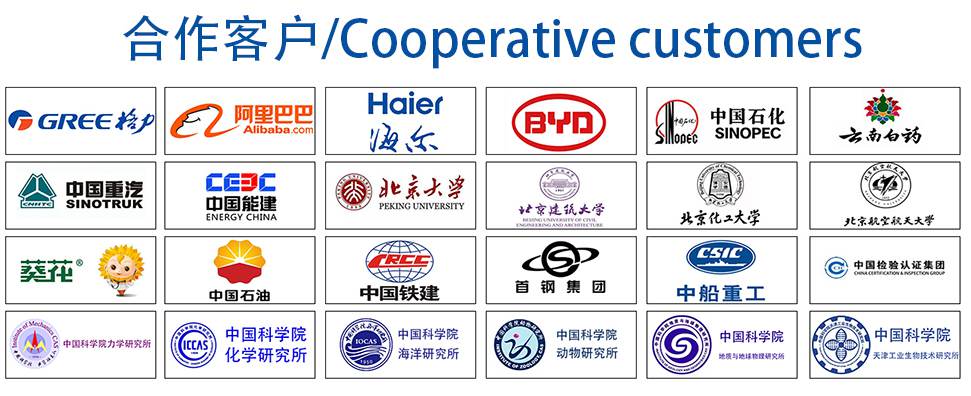