汽车机械式变速器总成检测技术详解
机械式变速器作为汽车动力传递的核心部件,其性能直接关系到车辆的传动效率、换挡平顺性及使用寿命。在整车制造、售后维修及质量管控环节中,变速器总成的系统性检测是保障车辆安全运行的关键步骤。根据GB/T 5333-2018《汽车机械式变速器技术条件》及QC/T 568-2021《汽车变速器台架试验方法》等行业标准,规范的检测流程应涵盖静态性能、动态特性、耐久性等20余项关键指标,确保变速器在复杂工况下的可靠性和适配性。
核心检测项目分类
1. 静态性能检测:
包含壳体密封性测试(气压法/荧光示踪法)、输入/输出轴径向跳动量测量(千分表精度需达到0.001mm)、换挡拨叉位移量标定。重点检测各档位齿轮啮合精度,使用齿轮啮合检查仪测量齿侧间隙(标准范围0.08-0.15mm)和啮合印痕覆盖率(≥80%为合格)。
2. 动态特性测试:
在专用试验台架上模拟实车工况,设置输入转速范围(0-6000rpm)和负载扭矩(最大需达标称扭矩的150%)。通过扭矩传感器实时采集传动效率(目标值≥95%),同时利用振动分析仪监测各档位NVH表现,异常振动频率段需控制在200Hz以下。
3. 换挡性能专项检测:
搭建电子换挡力测试系统,测量换挡手柄操作力(1-5档标准值:30-50N)、换挡行程偏差(允许±1.5mm)。借助高速摄像机记录同步器接合过程,分析同步时间(≤0.3s)和换挡冲击度(加速度峰值<3g)。
关键质量控制点
针对常见故障模式建立预警机制:
- 齿轮点蚀检测:使用工业内窥镜观察齿面,配合油液金属颗粒分析
- 轴承温升监控:红外热像仪实时记录运转温度(温升≤45℃)
- 密封件老化测试:85℃耐油试验持续72小时验证膨胀率
智能化检测技术应用
当前行业正加速推进AI检测系统部署,通过多传感器数据融合(振动+噪声+温度+压力),结合深度神经网络算法,可实现故障模式识别准确率提升至98%。某头部企业实施的数字孪生检测平台,使台架试验周期缩短40%,同时生成三维磨损预测模型。
随着新能源汽车对变速器紧凑化、轻量化的要求,检测技术正向着高精度(微米级形变检测)、高集成(多参数同步采集)、高仿真(虚拟现实工况模拟)方向持续演进。定期规范的检测不仅能预防突发故障,更能通过数据积累优化产品设计,推动传动系统技术迭代。
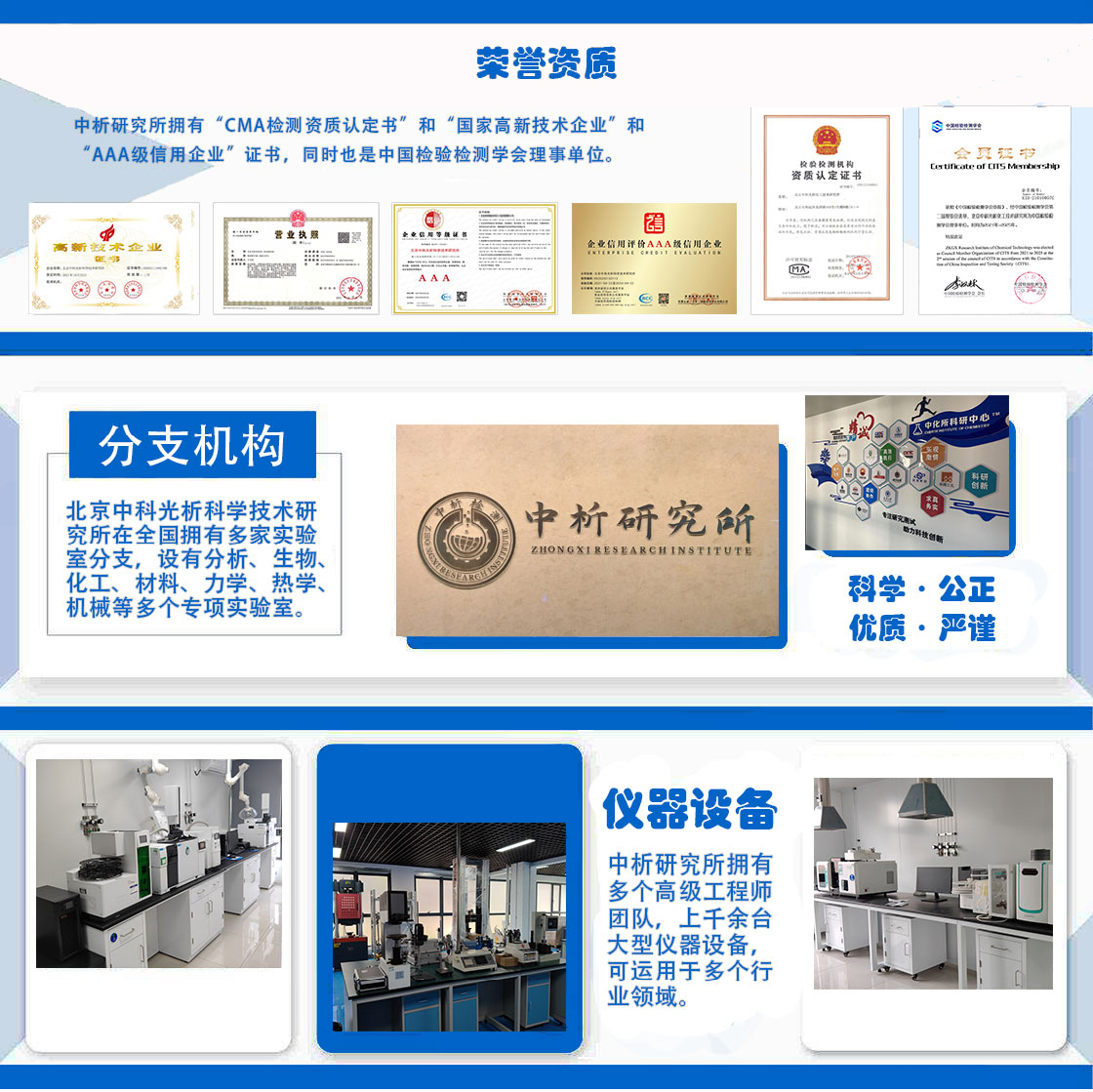
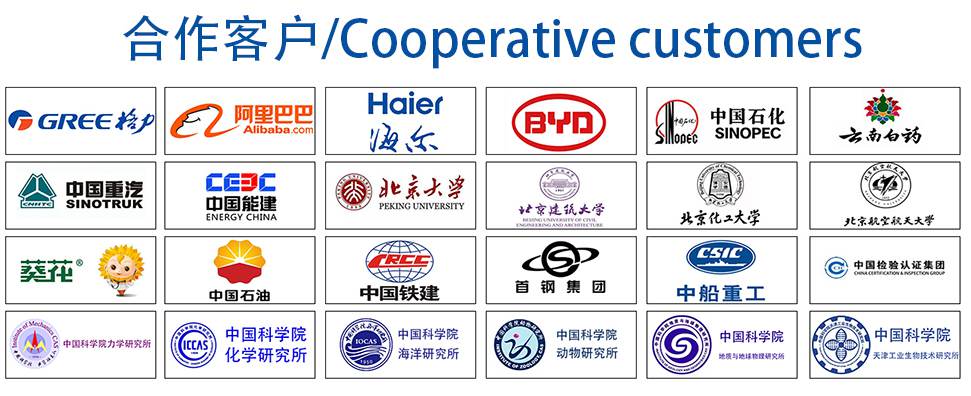