工程机械钳盘式制动器检测的重要性
钳盘式制动器作为工程机械(如挖掘机、装载机、起重机等)的核心安全部件,其性能直接关系到设备的操作安全和使用寿命。由于工程机械常处于高负荷、多尘、振动频繁的恶劣环境中,制动器易出现磨损、变形或液压系统故障等问题。定期对钳盘式制动器进行系统性检测,不仅能预防意外事故,还能延长关键零部件的更换周期,降低维护成本。检测过程需涵盖结构完整性、摩擦材料状态、液压响应效率等多个维度,确保制动器在紧急工况下仍能稳定输出制动力。
主要检测项目及方法
1. 制动器尺寸精度检测
使用激光测量仪或三坐标测量设备对制动盘厚度、平行度及钳体安装面平面度进行检测。允许偏差范围需符合ISO 3450或GB/T 18849标准,例如制动盘厚度误差不超过±0.05mm,轴向跳动量应小于0.15mm。
2. 摩擦片磨损状态分析
通过厚度规测量摩擦片剩余厚度,对比原厂设计值(通常磨损极限为原始厚度的1/3)。同时检查摩擦材料表面是否存在不均匀磨损、烧蚀或裂纹,异常磨损需排查钳体回位弹簧或液压活塞卡滞问题。
3. 制动盘热变形检测
采用红外热像仪监测连续制动工况下的温度分布,结合千分表测量制动盘热态变形量。要求工作温度不超过350℃,冷却后盘面端跳误差应恢复至0.1mm以内。若出现永久性翘曲需立即更换。
4. 液压系统密封性测试
在1.5倍额定工作压力下进行保压试验,5分钟内压降不得超过10%。使用荧光检漏剂检查液压管路、活塞密封圈等部位是否存在渗漏,特别注意高温环境对密封材料的影响。
5. 动态制动力矩标定
通过转矩传感器和动态测试台模拟实际载荷,验证制动力矩是否达到设计值的90%-110%。测试需覆盖冷态(常温)和热态(连续制动10次后)两种工况,确保力矩衰减率不超过15%。
6. 紧急制动响应时间检测
采用高速数据采集系统记录踏板力施加到完全制动的延迟时间,标准要求不超过0.3秒。异常延迟需检查液压管路排气是否充分或主泵内部阀件是否失效。
检测周期与数据管理
建议每500工作小时或季度进行常规检测,高强度工况下需缩短至300小时。检测数据应通过数字化平台记录分析,建立历史趋势图谱,对摩擦片磨损速率、液压效率等关键参数实现预测性维护。
结语
钳盘式制动器的系统性检测是保障工程机械安全运行的重要防线。通过标准化检测流程与智能化数据分析,企业可显著降低突发性故障风险,同时优化备件管理策略,为设备的高效作业提供坚实保障。
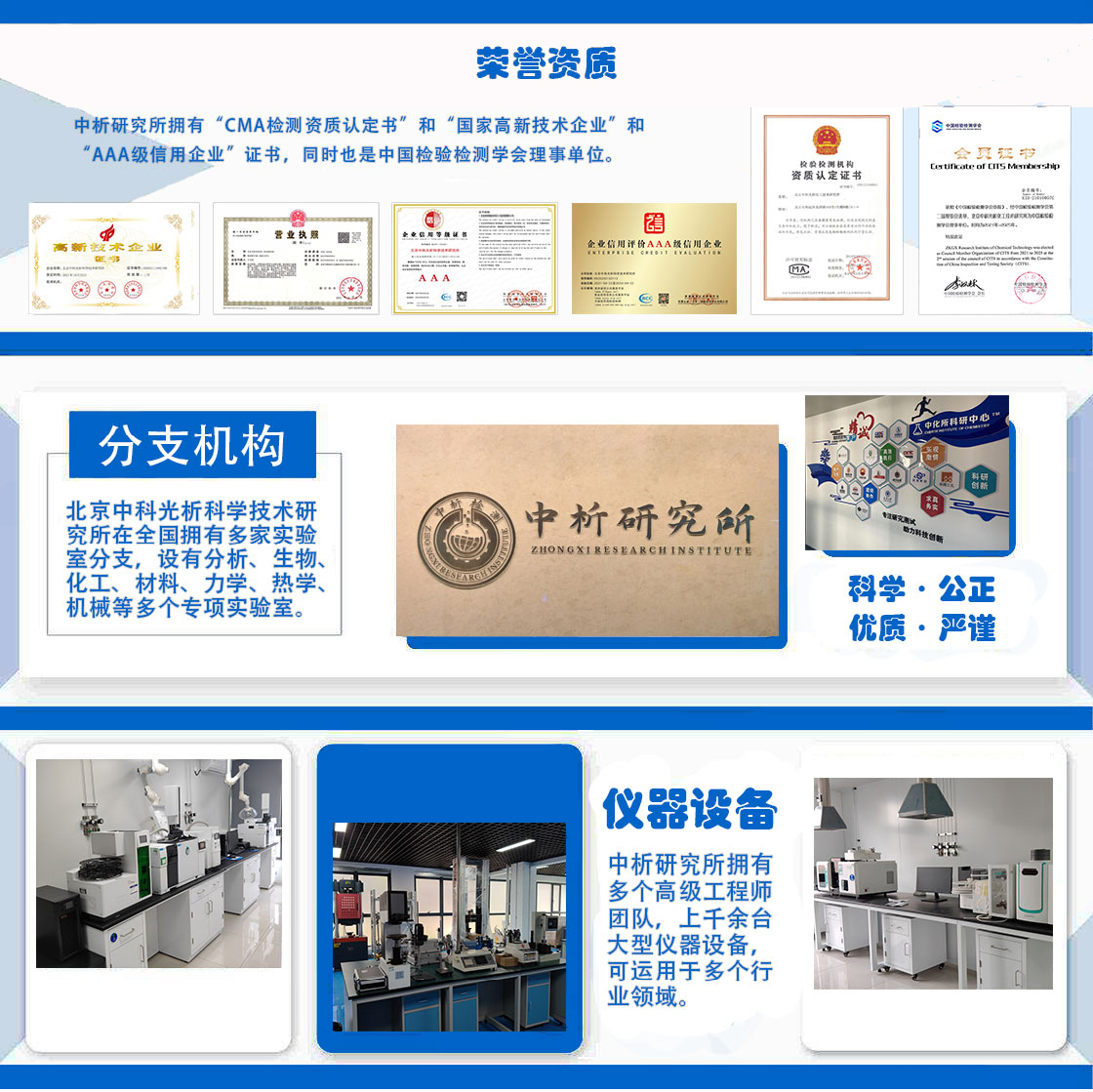
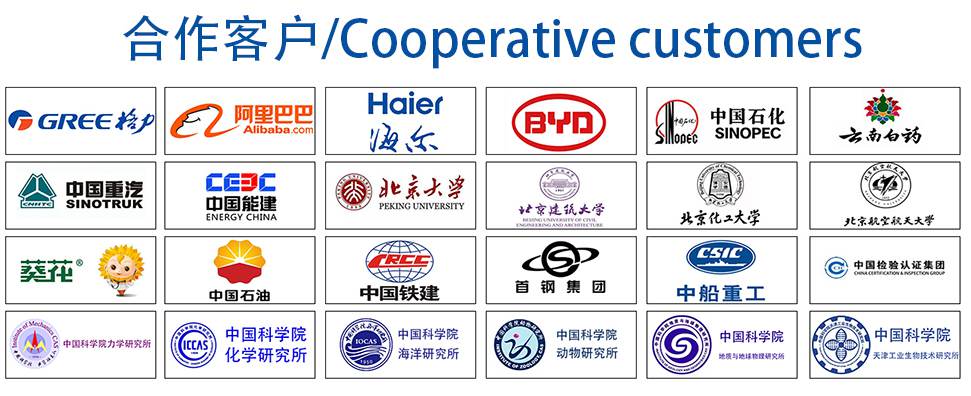