工程机械驱动桥检测的重要性
作为工程机械传动系统的核心部件,驱动桥承担着动力传递、载荷支撑及转向控制等关键功能,其性能直接影响到设备的工作效率与安全性。在矿山、建筑、港口等恶劣工况下长期运行的工程机械,驱动桥会因振动冲击、金属疲劳、润滑失效等原因产生磨损、变形甚至断裂风险。定期开展驱动桥检测不仅能预防突发故障,还能延长部件使用寿命,降低维修成本。根据行业统计,规范的检测可使驱动桥故障率降低40%以上。
驱动桥检测核心项目
1. 外观与结构完整性检测
采用目视检查与超声波探伤相结合的方式,重点检测桥壳是否存在裂纹、变形或腐蚀现象。使用三维坐标测量仪对桥体几何尺寸进行验证,确保主减速器安装面的平面度误差不超过0.05mm,轮毂轴承座同轴度偏差控制在0.1mm以内。
2. 齿轮传动系统检测
通过磁粉探伤检查主减速齿轮表面疲劳裂纹,利用齿轮啮合仪测量齿侧间隙(标准值0.15-0.25mm)和齿面接触斑点(应达到齿高60%、齿长75%以上)。重点检测差速器行星齿轮轴颈磨损量,超过0.08mm需立即更换。
3. 轴承与密封性检测
使用振动分析仪监测轮毂轴承的异常振动频谱,利用红外热像仪检测运行温升(正常工况不应超过80℃)。采用气压试验法验证桥壳密封性,在0.15MPa压力下保压3分钟,泄漏量需小于5kPa/min。
4. 润滑系统检测
取样分析齿轮油铁谱,当金属磨粒浓度超过150ppm时需预警。检查油液黏度变化范围(新油±15%以内),同步检测油道畅通性,确保各润滑点供油压力维持在0.2-0.4MPa区间。
5. 总成性能测试
在试验台架上模拟额定载荷工况,连续运转2小时后检测传动效率(应≥92%)、噪声值(≤85dB(A))及温升曲线。通过扭力测试验证半轴抗扭强度,其扭转角变形量不得超过1.5°/m。
智能化检测发展趋势
随着物联网技术的应用,新型驱动桥已集成振动传感器、温度监测模块和油液品质芯片,可实时传输关键参数至监控平台。基于大数据的预测性维护系统能提前3个月预判潜在故障,检测效率提升60%以上,标志着工程机械检测进入智能诊断新阶段。
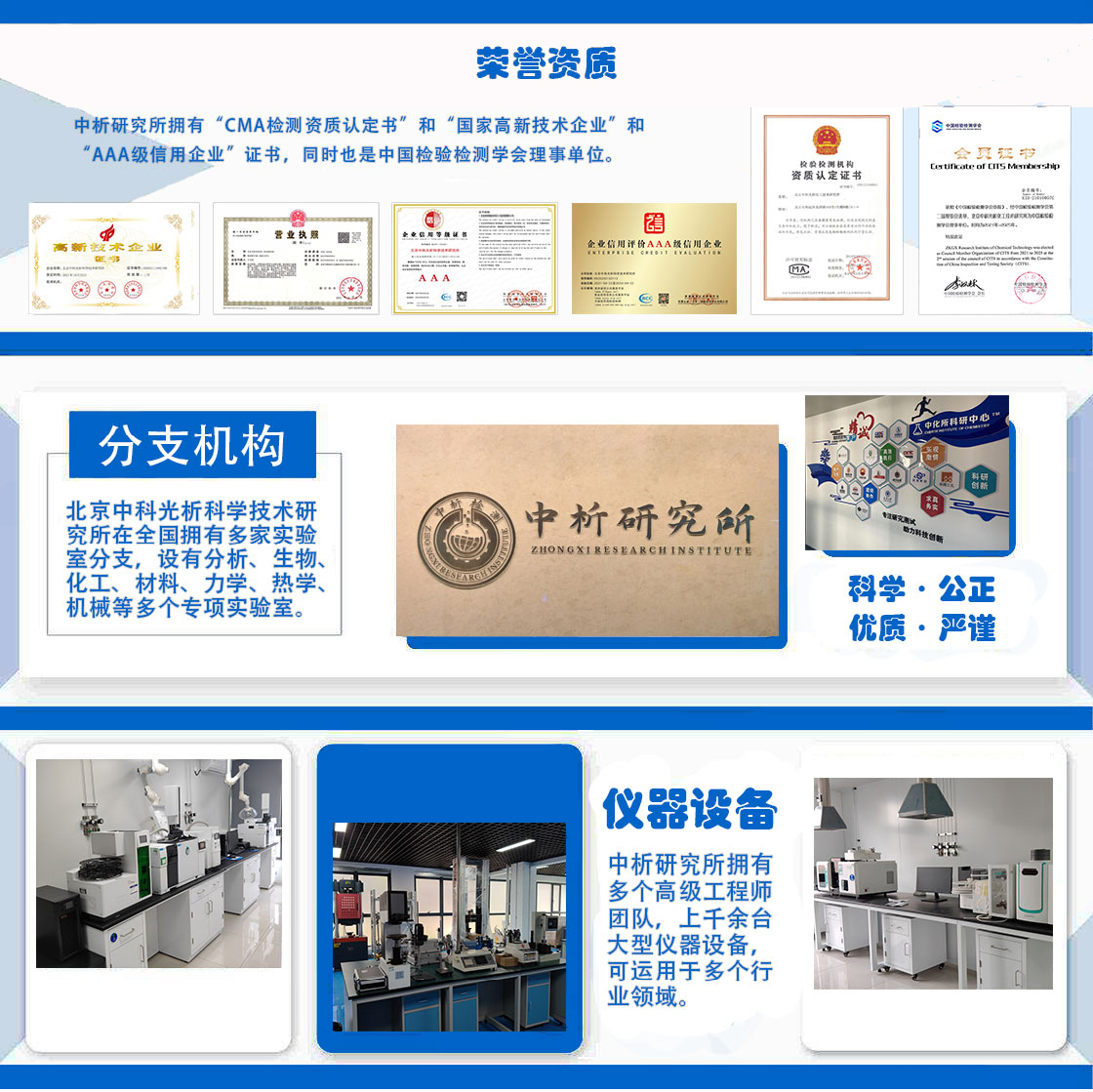
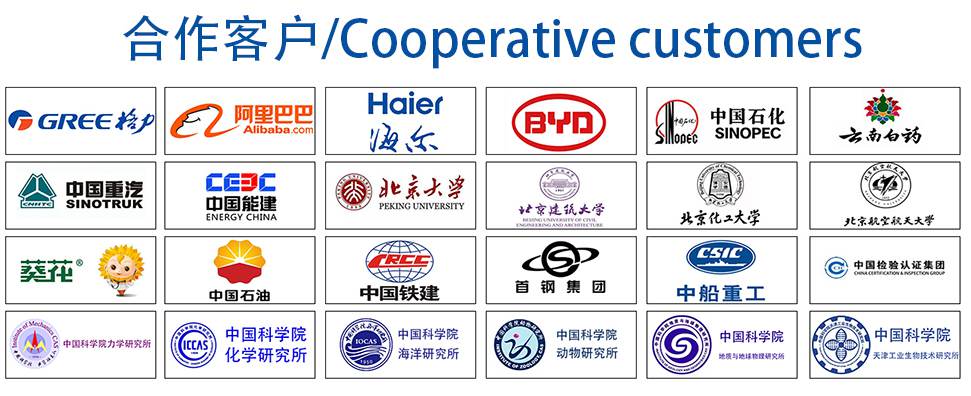