工程机械蹄式制动器检测的重要性
蹄式制动器作为工程机械关键安全部件,其性能直接影响设备制动效能与作业安全。在矿山机械、起重设备、重型运输车等场景中,制动系统长期承受高温、重载和频繁启停的考验,易出现蹄片磨损、间隙异常、摩擦材料老化等问题。据统计,工程机械事故中约15%与制动系统失效直接相关。通过系统化检测可及时发现制动器潜在隐患,避免因制动失效导致的设备损坏、作业中断甚至人员伤亡。
核心检测项目及方法
1. 制动蹄片厚度检测
使用数显游标卡尺测量制动蹄摩擦材料剩余厚度,对比制造商标定值(通常不小于原始厚度50%)。重点检查蹄片端部是否存在偏磨现象,同一车轴两侧蹄片厚度差应控制在0.5mm以内。
2. 摩擦材料表面状态分析
采用工业内窥镜观察摩擦表面是否存在裂纹、烧蚀或油污污染。通过敲击法检测摩擦片粘接强度,出现空鼓声需立即更换。配合表面温度检测仪确认制动时温度是否超出材料耐热极限(常规石棉基材料≤250℃)。
3. 制动鼓配合尺寸检测
使用三维坐标测量仪检测制动鼓内径圆度误差(应≤0.05mm)和同轴度(≤0.1mm)。重点检查工作面是否有沟槽、热裂纹等缺陷,深度超0.5mm需进行镗削修复。
4. 调节机构功能测试
手动操作调节螺杆确认进退灵活性,测量单次调节行程是否符合设计值(通常2-3mm)。使用扭矩扳手检测调节机构锁紧力矩,确保防松装置有效。
5. 制动器整体效能试验
在专用试验台架模拟满载工况,检测制动力矩衰减曲线。要求连续10次紧急制动测试后,制动力矩下降不超过初始值的15%,制动响应时间≤0.3秒。
智能检测技术应用
当前逐步推广的智能检测系统集成了激光位移传感器、热成像仪和振动分析模块,可实时监测制动器工作状态。通过AI算法分析摩擦噪音频谱特征,提前3-6个月预警异常磨损,检测效率较传统方法提升40%以上。
检测周期建议
建议按设备类型制定差异化检测计划:土方机械每500工作小时检测一次,起重设备遵循月检制度,矿用车辆需每班次进行目视检查。雨季、高原等特殊工况应缩短检测间隔30%以上。
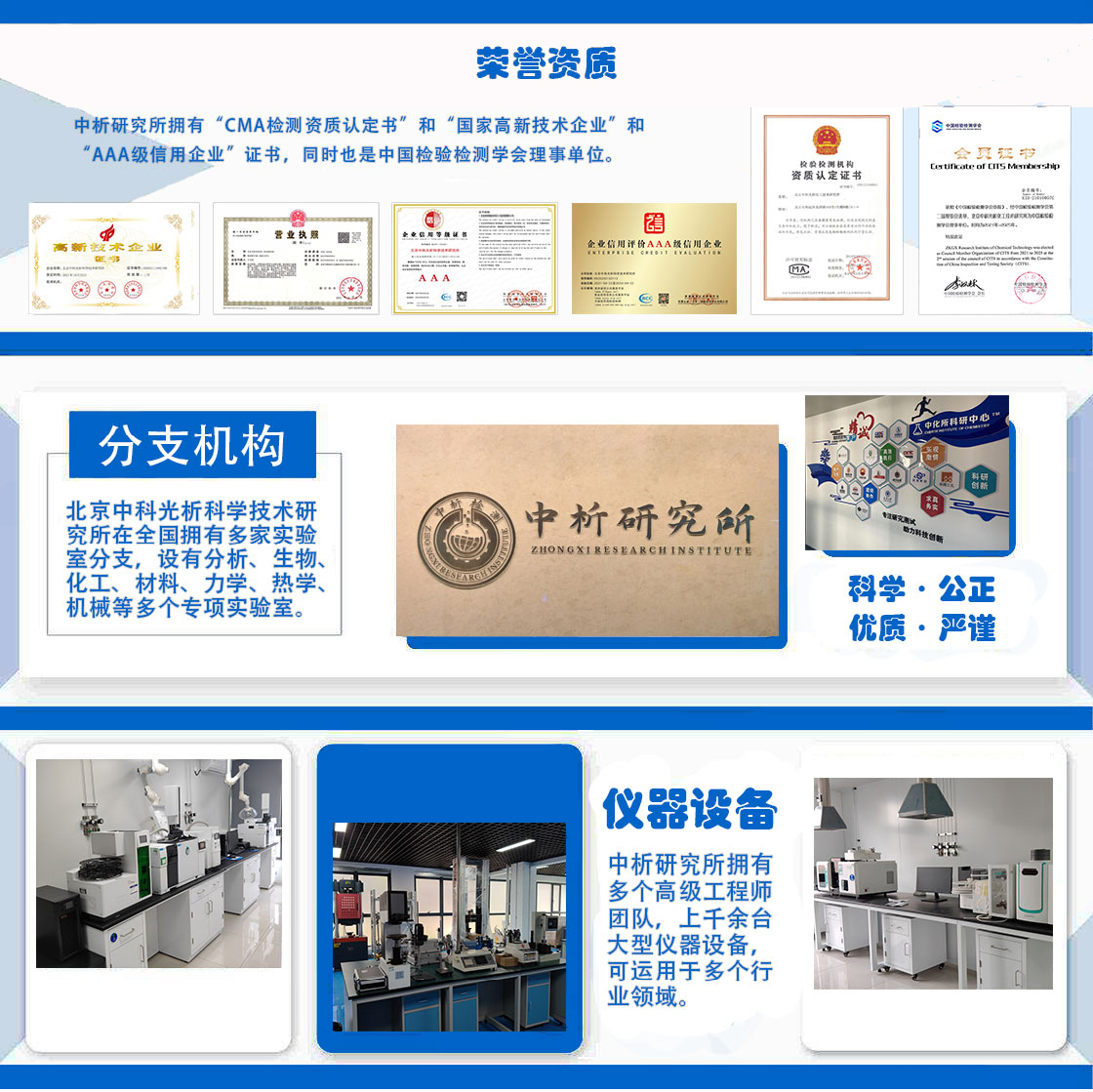
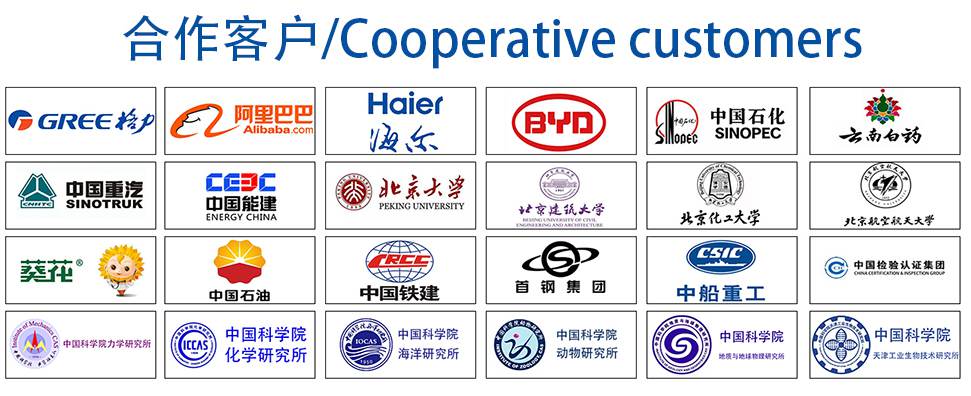