包装PET瓶坯注塑成型模具检测的关键项目与技术要求
PET(聚对苯二甲酸乙二醇酯)瓶坯作为饮料、日化用品等包装容器的核心组件,其成型质量直接关系到最终产品的密封性、外观精度及使用性能。注塑成型模具是生产PET瓶坯的核心装备,其精度、耐久性和设计合理性直接影响生产效率和产品质量。为确保模具满足工业化生产的严苛要求,从原材料选择到制造工艺,再到后期维护,均需通过系统性检测来验证其性能。特别是在高速注塑生产场景下,模具的微小缺陷可能导致瓶坯壁厚不均、合模线偏移或应力集中等问题,进而引发漏液、爆瓶等严重质量事故。因此,实施全面的模具检测不仅是质量控制的关键环节,更是企业降本增效的必要手段。
1. 尺寸精度检测
模具的尺寸精度直接决定瓶坯的几何形状与容积一致性。检测时需使用三坐标测量仪(CMM)对模腔、模芯、流道系统等关键部位进行三维扫描,重点验证以下参数:模腔直径公差(通常要求±0.005mm)、成型面轮廓度(≤0.01mm)、浇口位置偏差(<0.1mm)以及分型面的平面度(需控制在0.002mm/m以内)。对于多腔模具,还需通过光学投影仪比对各模腔的对称性,避免因加工误差导致注塑压力分配不均。
2. 表面质量与结构完整性检测
模具表面粗糙度需达到Ra≤0.2μm以保障瓶坯脱模顺畅,通过白光干涉仪或表面轮廓仪进行多点测量。同时需借助金相显微镜检查模具钢材的微观结构,确保无气孔、裂纹等铸造缺陷。针对高磨损区域(如浇口套、顶针孔),需使用硬度计验证表面硬度是否达到HRC52-56的设计标准,并利用超声波探伤仪检测内部是否存在疲劳损伤。
3. 冷却系统效能验证
冷却系统的设计直接影响瓶坯结晶度与成型周期。检测时需模拟实际生产条件,通过热成像仪监测各冷却水路温度分布均匀性(温差需<2℃),并使用流量计验证水流速是否达到8-12m/s的工艺要求。此外,需通过压力衰减测试排查管路泄漏风险,确保冷却水压稳定在0.6-1.0MPa范围内。
4. 材料性能与耐腐蚀性测试
针对模具钢材,需通过光谱分析仪验证其成分是否符合NAK80、S136等预硬钢的合金配比,并开展盐雾试验(72小时以上)评估耐腐蚀性能。对于表面镀层(如CrN、DLC涂层),需使用划痕试验机测试结合强度(临界载荷≥50N),并通过摩擦磨损试验机模拟长期使用下的耐磨表现。
5. 模具寿命与动态性能评估
通过注塑机搭载模具进行连续试模(≥10万次),监测分型面磨损量、顶针机构卡滞频率等指标。利用应变片和振动传感器记录模具在高速开合模(<1.5秒/周期)下的应力分布与共振特性,优化结构设计以避免疲劳失效。同时需建立模具维护周期模型,根据检测数据制定预防性维修计划。
通过上述多维度的检测体系,企业可实现模具全生命周期管理,将PET瓶坯的成型不良率控制在0.3%以下。未来随着工业CT、AI缺陷识别等技术的普及,模具检测将向智能化、在线化方向发展,进一步推动包装行业的质量升级。
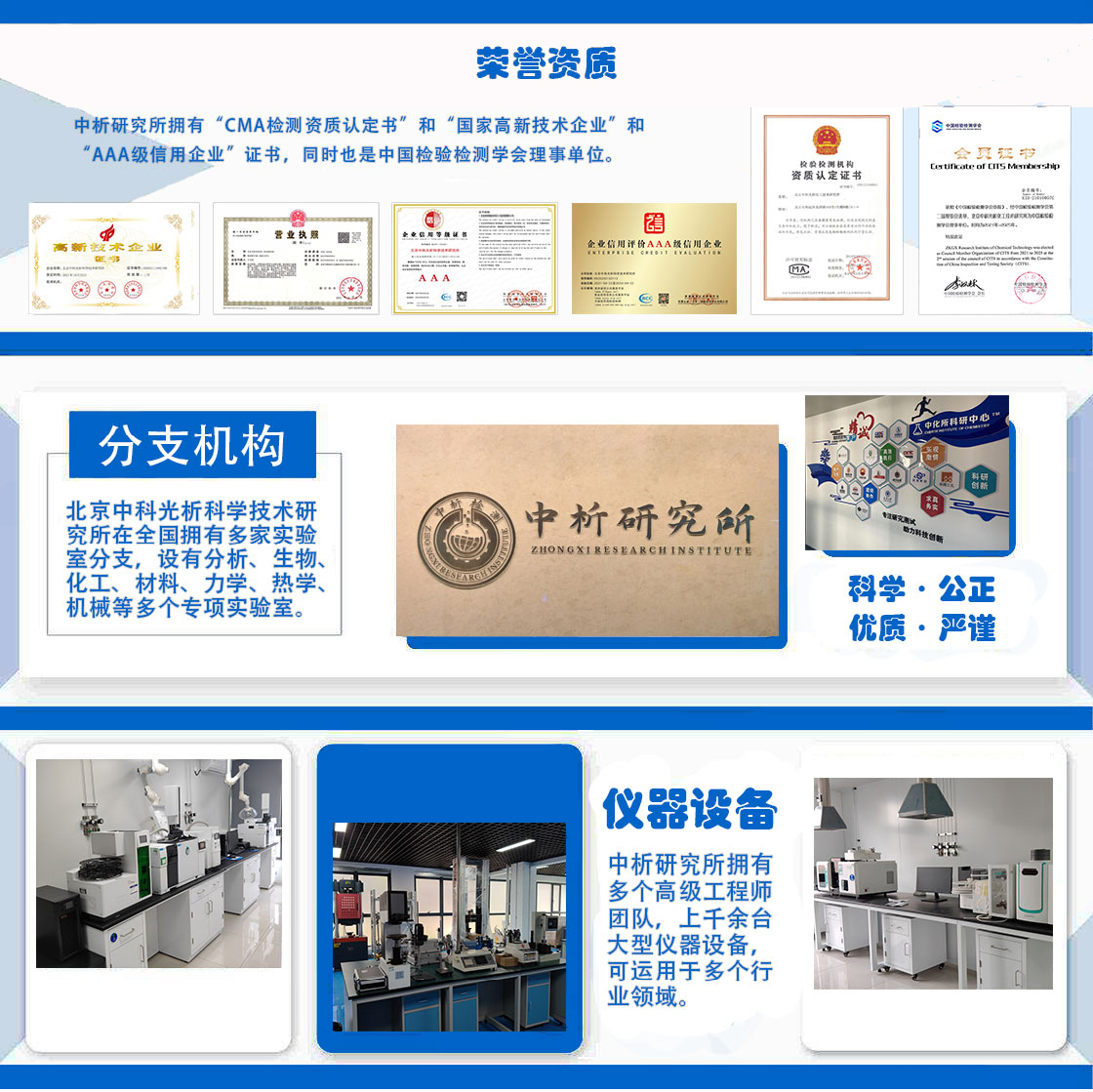
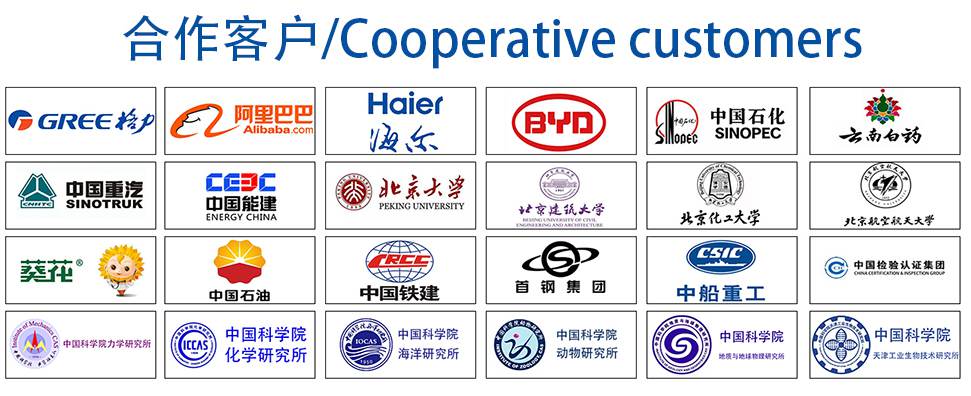