数控电火花微孔加工机床作为精密制造领域的重要装备,广泛应用于航空航天、医疗器械、精密模具等行业中微小孔洞的高精度加工。随着加工精度要求的不断提高,机床的稳定性、放电控制能力及加工效率成为行业关注的核心。为确保机床性能符合设计要求,并满足复杂工况下的长期可靠运行,对其进行系统性检测至关重要。检测项目需覆盖机械结构、电气系统、加工精度、能耗效率及安全防护等多维度指标,通过科学的数据采集与分析,为设备优化与工艺调整提供依据。
一、加工精度检测
加工精度是衡量数控电火花微孔加工机床性能的核心指标,需通过多维度检测项目验证:
1. 孔径尺寸精度:采用激光测量仪或三坐标测量机对加工后的微孔直径进行重复性测试,误差需控制在±2μm以内;
2. 孔位重复定位精度:通过预设网格化坐标点加工,验证机床坐标系统的定位稳定性;
3. 表面粗糙度:使用白光干涉仪检测加工面Ra值,评估放电能量控制系统的优化程度。
二、电极损耗监测
电火花加工中电极损耗直接影响加工质量和成本,检测重点包括:
1. 电极轴向损耗率:通过高倍率显微镜测量加工前后电极长度变化,计算单位时间的损耗量;
2. 侧向损耗均匀性:分析电极侧壁形貌,确保放电均匀性达到工艺要求;
3. 材料适应性测试:针对不同电极材料(如铜钨合金、石墨)进行损耗对比试验。
三、放电状态分析
通过实时监测放电波形和能量分布,评估机床的放电稳定性:
1. 脉冲波形检测:采用示波器采集单脉冲波形,分析前沿时间、峰值电流等参数一致性;
2. 短路/电弧比例:统计加工过程中异常放电的发生频率,优化伺服控制算法;
3. 能量利用率计算:结合加工效率与能耗数据,建立能量转化效率评估模型。
四、设备稳定性评估
长周期运行的稳定性检测项目包含:
1. 温升变形测试:连续工作8小时后,测量主轴热位移量及床身变形量;
2. 振动频率分析:通过加速度传感器采集各轴向振动频谱,识别机械传动异常;
3. 介质过滤系统效能:监测工作液杂质含量变化对放电间隙稳定性的影响。
五、安全与环保检测
根据GB/T 5226.1等标准要求,重点检测:
1. 绝缘电阻测试:高压回路对地绝缘电阻值需≥10MΩ;
2. 废气处理效率:检测油雾收集装置对加工产生的有害气体的过滤效率;
3. 紧急制动响应时间:验证安全防护装置在突发情况下的动作可靠性。
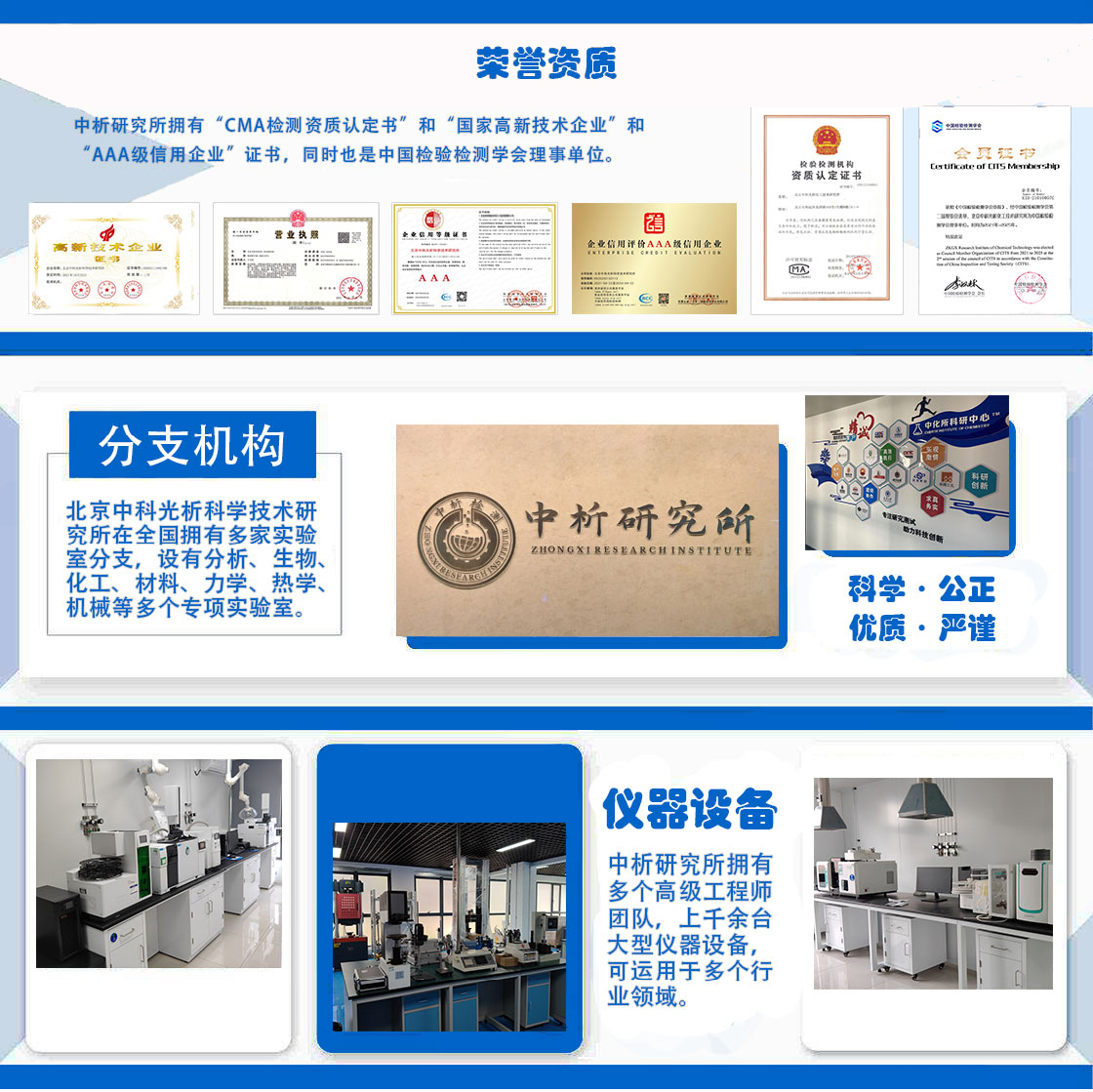
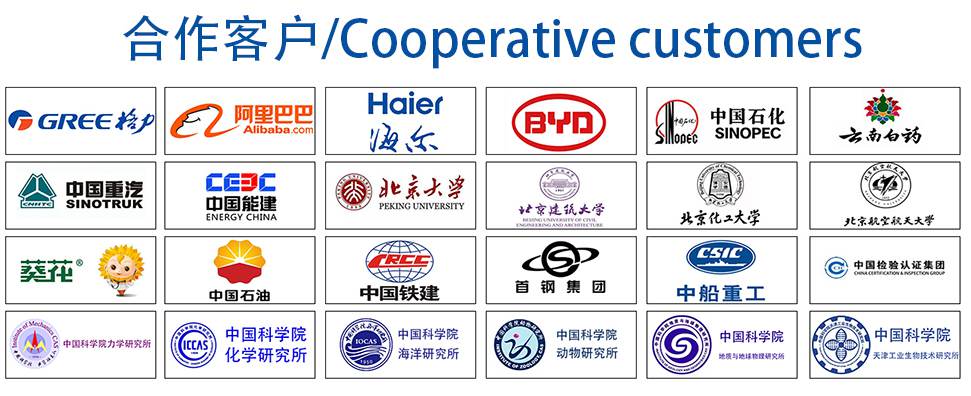