工业机器人性能检测
实验室拥有众多大型仪器及各类分析检测设备,研究所长期与各大企业、高校和科研院所保持合作伙伴关系,始终以科学研究为首任,以客户为中心,不断提高自身综合检测能力和水平,致力于成为全国科学材料研发领域服务平台。
立即咨询工业机器人性能检测的核心价值与技术挑战
在智能制造快速发展的背景下,工业机器人已成为汽车制造、电子装配、金属加工等领域的核心生产力工具。其性能直接关系着生产线的运行效率、产品质量及企业成本控制。工业机器人性能检测通过系统性评估设备的运动精度、负载能力、可靠性等关键指标,为企业提供设备选型依据、故障预警和生产工艺优化方案。随着协作机器人、柔性制造单元等新型应用场景的拓展,检测体系需要兼顾ISO 9283、GB/T 12642等国际国内标准,同时应对高速动态响应、人机协同安全等新兴技术挑战。
核心性能检测项目体系
1. 定位精度与重复定位精度检测
采用激光跟踪仪、视觉测量系统等高精度仪器,在TCP(工具中心点)位置进行三维空间坐标采集。通过对比指令位置与实际到达位置的偏差,计算绝对定位精度(通常要求±0.05mm以内)。重复定位精度测试需进行50-100次循环运动,统计标准差以验证设备稳定性。
2. 运动轨迹精度检测
在直线/圆弧插补模式下,通过动态测量装置记录实际运动轨迹。重点评估速度波动(要求≤5%)、轮廓误差(复杂轨迹≤0.1mm)及拐角过冲等参数。对于焊接、喷涂等工艺机器人,还需检测姿态角偏差对工艺质量的影响。
3. 负载性能综合测试
使用六维力传感器进行额定负载、极限负载下的性能验证:
- 最大负载测试:持续运行时的扭矩输出能力
- 惯性负载测试:快速启停时的动态响应特性
- 偏载测试:非对称负载下的位姿保持能力
测试需覆盖所有关节在不同转速下的力矩-速度曲线特征。
4. 动态响应特性分析
通过阶跃响应测试获取系统调节时间(通常<0.5s)、超调量(<15%)等时域指标。频域分析需测定各轴谐振频率,确保机械结构刚性满足高速运动需求。振动测试要求末端抖动幅度在0.02mm以内。
5. 耐久性及可靠性验证
执行72小时连续运行测试,监测温升(关节电机<65℃)、噪声(<75dB)等参数变化。累计运行5000公里后检测传动部件磨损量,评估减速器背隙、谐波齿轮寿命等关键指标退化程度。
6. 环境适应性测试
在-10℃至50℃温度范围内测试定位精度衰减率,湿度95%RH条件下验证电气绝缘性能。防尘防水测试需达到IP54以上防护等级,振动测试模拟运输工况下的结构完整性。
7. 安全功能验证
依据ISO 10218标准,测试碰撞检测响应时间(<50ms)、安全限速功能、紧急停止触发可靠性。协作机器人还需通过ISO/TS 15066标准中的人体接触力测试,确保功率与力限制系统有效。
检测技术发展趋势
当前检测技术正向智能化方向发展,数字孪生技术可实现虚拟调试与性能预测,5G通讯支持远程实时监测,AI算法用于异常模式识别。随着协作机器人、移动复合机器人等新形态设备的普及,检测体系将面临更多维度、更高精度的技术挑战。
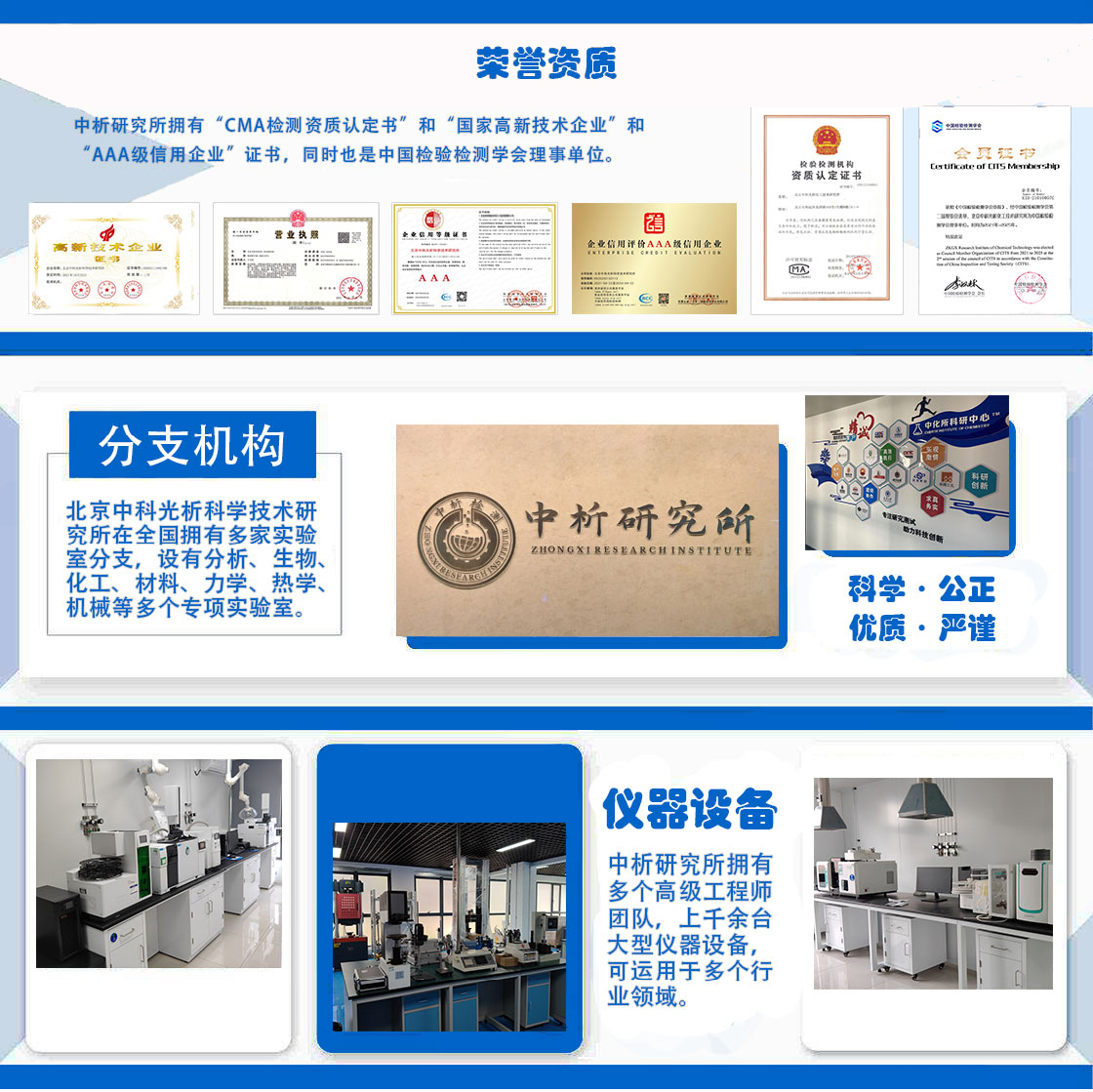
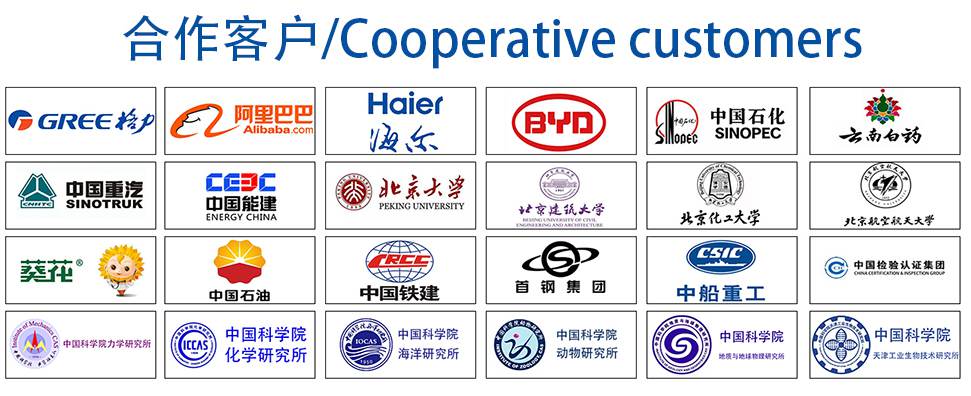